Main Responsibilities and Required Skills for Production Supervisor
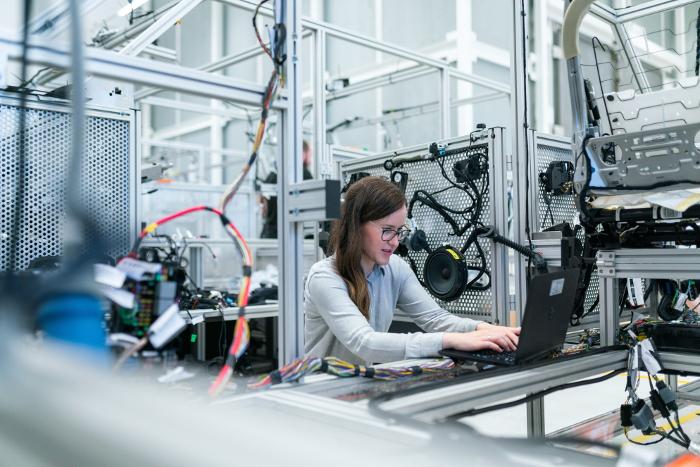
A production supervisor supervises the manufacturing of goods and services. In other words, they are in charge of ensuring that the process of developing a product from concept to completion runs smoothly and that all resources are appropriately utilized. In this blog post we describe the primary responsibilities and the most in-demand hard and soft skills for Production Supervisors.
Get market insights and compare skills for other jobs here.
Main Responsibilities of Production Supervisor
The following list describes the typical responsibilities of a Production Supervisor:
Accomplish
Accomplish manufacturing goals by communicating job expectations.
Accomplish manufacturing results by leading, directing, and communicating with staff.
Accomplish manufacturing staff result by communicating job expectations.
Accomplish manufacturing staff results by communicating job expectations.
Accomplish special project results by identifying and clarifying issues and priorities.
Achieve
Achieve better than 95% efficiency on all projects.
Achieve departmental goals – safety, quality, delivery and cost.
Achieve plant cost targets.
Adhere to
Adheres to production schedules, assigning staff to ensure that production goals are met.
Adhere to all applicable job procedures as outlined in SOP manual.
Adhere to all safety policies and procedures.
Adhere to GMPs, SQF and HACCP written Program.
Adhere to the OSHA safety code and company policies.
Administer
Administer all rules, programs, and procedures that pertain to direct reports.
Administer corrective disciplinary actions as needed.
Administer environmental policies and ensures regulations are followed.
Administer salary and budget programs.
Analyse
Analyse and complete required reports.
Analyze problems, take corrective measures to resolve, maintain standards.
Analyze and resolve work problems, or assists workers in solving work problems.
Anticipate
Anticipate and inform line management of existing and potential non-compliance events.
Anticipate needs for parts / materials / tools and follow up to ensure availability when required.
Approve
Approve and organize employee vacations.
Approve, compute, and record employee hours on time cards.
Assign
Assign people to work stations and inform supervisor of any absences and / or line problems.
Assign personnel and determines use of machines so as to achieve this goal.
Assist with
Assist assigned personnel in resolving on-the-job problems.
Assist in conducting physical inventories as required.
Assist in prioritizing actions to be taken and integrate best practices into daily operations.
Assist Operations Manager to develop a system for continuous improvement.
Assist operators in diagnosing complex machine issues.
Assist Plant Supervisor as required.
Assist the Plant Manager in planning space utilization to meet prescribed cost standards.
Assist / Troubleshoots problems and participates in resolution of issues as they arise on the shift.
Assist with and support team projects and duties as required.
Assist with interviewing new candidates.
Assist with the implementation of process improvements and / or capital projects as needed.
Attend
Attend and provide notes for weekly production meetings.
Attend weekly meetings for escalations, CAB and IRB.
Build
Build and maintain productive relationships that foster employee engagement and satisfaction.
Build positive relationships with others and conduct negotiation to establish win / win solutions.
Carry out
Carry out basic quality and testing checks.
Carryout the induction training specifically related to the Print / Production lines.
Carry out the start meeting of the shift with the staff.
Champion
Champion continuous improvement efforts throughout the facility.
Champion the deployment of business systems.
Check
Check charts on machines for accuracy.
Check production output according to determined quality specifications.
Coach
Coach necessity and use of Problem Solving tools.
Coach use of Standard Work to eliminate NVA work, coach link to effort reduction.
Communicate
Communicate and enforce company policies and procedures.
Communicate and work with maintenance on shutdowns and to meet Preventative Maintenance objectives.
Communicate daily / shift goals to workforce.
Communicate effectively with other supervisors to build teamwork and co-operation.
Communicate instruction clearly and effectively to eliminate all possibilities of misleading.
Communicate job expectations to shift employees and enforce systems, policies and procedures.
Communicate material requirement plans to suppliers and resolves conflicts.
Communicate operations plan in order to have better production, safe time and ensure goals are met.
Communicate Proactively and Effectively – Communicates clearly, candidly, directly and concisely.
Communicate with Customer Service to ensure on time delivery.
Complete
Complete and audit production documents, and maintain necessary usage, cleaning and calibration logs.
Complete and distribute a daily show flash (P&L) of every event.
Complete individual performance evaluations.
Complete one-on-ones and performance reviews with all employees.
Complete production plan by establishing priorities, scheduling and assigning personnel.
Complete quality inspections on all completed parts and products.
Complete robust annual performance review with each team member.
Complete tasks on time or notifies appropriate person with an alternate plan.
Conduct
Conduct daily kick off meetings with a discussion on safety and stress safety as a core value.
Conduct job specific orientation.
Conduct meetings to negotiate, explain, persuade, or present information.
Conduct regular employee communication meetings on shift.
Conduct training as required.
Contribute
Contribute and make recommendations to control and reduce departmental and overall costs.
Contribute towards efficiencies and improvements when possible.
Coordinate
Coordinate activities related to shift starts and changes.
Coordinate and align detailed schedule with product developers.
Coordinate and approve vacations.
Coordinate and complete weekly work schedules.
Coordinate and store inventory, conduct regular quality checks.
Coordinate and transfer of stock to the warehouse through the Warehouse Supervisor and Line Porters.
Coordinate cheese manufacturing processes and ensure compliance with production plans.
Coordinate orders to ensure on-time delivery to customers.
Coordinate, organize and schedule all comportment through Lead Hand to production lines.
Coordinate packaging needs (proper size, type, and timing) with appropriate batching person.
Coordinate process problems that involve deviation from standard conditions.
Coordinate the training and development of hourly members of the Paper Mill.
Coordinate with Production / Operations Manager and other departmental.
Create
Create and maintain employee files (i.e. training, attendance, and performance).
Create schedules and work to ensure that the team meets all milestones.
Detect
Detect and assist employees with performance issues.
Detect, assist and address employees with performance issues including terminations.
Determine
Determine appropriate action beyond guidelines.
Determine effective work processes.
Develop
Develop a collaborative and effective interface with all site resources as listed in the scope.
Develop and execute loss analysis, glide path and 90 day improvement plans for the line(s).
Develop and implement improvements in the areas of throughput, cycle time and inventory reduction.
Develop and maintain all safety and environment programs.
Develop and / or implement departmental reporting as required by production manager.
Develop and refine new and existing training materials for team.
Develop, communicate and ensure compliance with all policies and procedures.
Develop job engagement, work focus, and business understanding among employees.
Develop new processes that enable the company to turn over more mixers per day.
Develop personal growth opportunities for all employees.
Develop process and SOP for new products.
Develop short / long strategies to resolve problems / delays in labeling and packaging systems.
Document
Document all activities as required.
Document and measure each employee's performance and performs annual reviews.
Document processes to ensure overall project consistency.
Drive
Drive, commitment, self-motivation and high energy.
Drive continuous development to production, quality, cost, and delivery initiatives.
Drive culture of continuous improvement.
Drive and assure active team member involvement in TPM programs.
Drive and ensure all team members are engaged and focused on creating a safe work environment.
Ensure
Ensure accurate timekeeping.
Ensure all resources and assets are used efficiently and correctly.
Ensure all Safety and operating procedures are followed.
Ensure all the staff adheres to food safety, health & safety, and GMP requirements.
Ensure and implement safety programs.
Ensure area compliance with site EHS requirements and support site safety programs.
Ensure a safe work environment and that all team members follow company policies and procedures.
Ensure company policies are understood and followed.
Ensure company standards and operations are satisfied.
Ensure complete team / area adherence to SOPs, MBRs and any other instructions.
Ensure compliance to workplace policies according to safety objectives.
Ensure compliance with company guidelines and procedures.
Ensure compliance with environmental, process and product quality standards.
Ensure compliance with food quality, safety and defence requirements.
Ensure constant communication with employees (floor rounds, logbooks, etc.).
Ensure continuous improvement of work practice.
Ensure employees are trained on procedures relating to safety, production, and quality.
Ensure employees complete all company required training including but not limited to ServSafe.
Ensure employees completion of all required safety training.
Ensure excellent quality across all areas of production.
Ensure HACCP / SQF and Health & Safety polices are respected.
Ensure In-Process samples are properly handled.
Ensure machinery and equipment are in safe working order.
Ensure material is handled and used properly without any loss.
Ensure operation of equipment by fixing repairs and maintiang machines.
Ensure operation of equipment & notifies Ops Manager for any safety issues and or repairs needed.
Ensure pick tickets and staged materials for jobs are ready for fabricators.
Ensure production flow of processes by reducing / eliminating bottlenecks on a shift by shift basis.
Ensure production meets the established schedule and shipments can be made accurately and on-time.
Ensure production targets and quality standards are maintained.
Ensure proper handover between shifts to optimize productivity and respect production schedule.
Ensure proper safety records, accident reports, etc. are promptly reported and investigated.
Ensure Quality Control measures are met at line start up and through-out the production run.
Ensure technician adherence to detailed assembly instructions, processes, policies and procedures.
Ensure that all employees both newly hired and current are properly trained.
Ensure that all safety norms are followed.
Ensure that an effective communication system is in place through all levels of the process.
Ensure that equipment is utilized in the most efficient manner.
Ensure that performance standards are met on a continuous basis.
Ensure that proper chemicals levels are being used and proper procedures are being followed.
Ensure that safe conditions exist at all times within the work environment.
Ensure that they are being followed by members of team.
Ensure that training and qualifications are current for all employees in the Shift / Department.
Ensure the accuracy of operation parameters and provide MRP values.
Ensure the appliance is produced to Quality specifications and standards.
Ensure the effective use of manpower, equipment, material and others production resources.
Ensure the efficient management of operations of a multiple shift production facility.
Ensure the proper functioning of equipment and identify potential problems.
Ensure the safe use of equipment and schedule regular maintenance.
Ensure the timely reporting of process KPIs and other information as necessary.
Ensure use of machinery, chemicals and tools are used in accordance with company policies.
Ensure work is performed safely.
Ensure work requests issued for any defects.
Establish
Establish an optimal work schedule for his group in relation to the operational needs of the factory.
Establishs and maintain effective working relationships.
Establishe, and where necessary, adjusts work procedures to meet production schedules.
Establishe a working environment that fosters participation within and between teams.
Establishe or adjusts work procedures to meet production schedules.
Establish priorities when faced with multiple projects.
Establish procedures, metrics, and processes.
Follow
Follow instructions, responds to management direction.
Follow policies and procedures.
Foster
Foster a culture of open communication, collaborative engagement, and team development.
Foster an environment that promotes teamwork and inclusion.
Foster a continuous improvement performance culture.
Help
Help develop and roll out an operational strategy in line with his / her sector's business strategy.
Help production staff succeed through performance management.
Help to install complex systems and conduct inspections of equipment with guidance.
Help train new employee's.
Hold
Hold employees accountable to their job duties in a fair, consistent and professional manner.
Hold regular scheduled meetings with reports.
Hold safety meetings and shift meetings as needed to keep the department functioning.
Identify
Identify and capably address safety hazards.
Identify and document absences, delays or behavioral problems and apply intervention required.
Identify process / equipment improvements to drive continuous improvement actions.
Identify training needs of staff regularly.
Identify training requirements.
Implement
Implement and maintain company policies.
Implement and maintain quality inspection procedures.
Implement Company and plant procedures and policies.
Inspect
Inspect all materials and equipment to detect malfunctions.
Inspect and make production decisions regarding acceptability of the glass products.
Insure
Insure individual and team levels of performance meet or exceed goals and expectations.
Insure Preventative Maintenance (PM) is being performed routinely and 6S principles are.
Keep
Keep product moving through the system in a timely, efficient manner.
Keep all work areas safe, clean and in good condition.
Lead
Lead and coach employees by implementing and maintaining good work and safety standards.
Lead and / or support Kaizen Events as related to production.
Lead departments to achieve goals and ship orders on time according to the production.
Lead manufacturing problem resolutions (i.e. labor standards, line balancing).
Lead, mobilize, develop and train his / her personnel.
Lead and carry safety and quality process auditing.
Lead and facilitates continuous improvement projects.
Lead a team of 20 - 25 production associates.
Leads immediate problem solving at the front line and minimizes repeat mistakes.
Lead the continuous improvement of production operations and procedural documentation.
Lead the execution of the validation master plan for newly transferred or existing products.
Lead team activities to improve goals.
Lead technical support staff in troubleshooting and enhancing production processes.
Lead the effective and efficient utilization of operating personal on a day to day basis.
Maintain
Maintain accurate computerized inventory control and cycle counts.
Maintain a current knowledge of product, design and assembly techniques.
Maintain a high level of awareness on safety, environmental and process compliance.
Maintain an acceptable attendance record.
Maintain and improve production.
Maintain and / or improve quailty programs.
Maintain a proactive attitude towards your own personal and professional development.
Maintain a safe environment and ensure all GMPs are followed.
Maintain compliance, cleanliness and orderliness of operational areas per appropriate SOPS.
Maintain continuity for all main employees through planning and training.
Maintain correct inventory records for warehouse and workflow areas.
Maintain daily production records and required documentation.
Maintain established safety and health policies and regulations.
Maintain GMP and cleanliness throughout plant.
Maintain inventory on materials and sterile items used in the at SPM facility.
Maintain positive employee-relations (Employee reviews done timely and constructively).
Maintain production schedules and arrange for production adjustments as required.
Maintain proper discipline in production area.
Maintain records and verify accuracy of inbound / outbound paperwork.
Maintain regular communications with Production Manager and the GM.
Maintain staff attendance records.
Maintain staff by recruiting, selecting, orienting, and training employees.
Maintain thorough knowledge of all processes and equipment.
Maintain time and production records.
Maintain training and conformance to all ISO procedures.
Maintain work procedures or modify production methods as needed.
Make
Make and communicate decisions that are appropriate for level of accountability.
Make changes when necessary.
Make recommendations to improve productivity and product quality.
Make sure production targets are met.
Make sure the people safety by means of wearing required PPE.
Manage
Manage active employees files in coordination with HR.
Manage all aspects of FreshTAP's keg operations and work with relevant metrics.
Manage and prioritize work to a profitable completion.
Manage and supervise union employees.
Manage a team of 30 during peak.
Manage department KPI's, operational metrics and report on results.
Manage employee attendance, scheduling, overtime and payroll.
Manage employee performance, address employee relation issues and administration of discipline.
Manage employee relations on shift.
Manage labour cost to budget targets.
Manage material stock levels and as required ordering new materials from suppliers.
Manage operator testing and leveling program in compliance with Kuraray policies and procedures.
Manage or facilitate continuous improvement projects (Lean Six Sigma, Kaizen, GI).
Manage Product Control including, but not limited to, product design and development.
Manage production associates.
Manage production schedules.
Manage / secure appropriate line staffing.
Manage shift work assignments and manning.
Manage site compliance to management systems.
Manage the training of team members on new or revised packaging related documents and procedures.
Manage work flow balancing - - the division of responsibilities amongst employees on each shift.
Manage the needs of assigned production areas.
Manage within labor and operating expense budget.
Manage workflow, maintain schedules, monitor job performance, and resolve problems.
Monitor
Monitor all phases of the production line and quality of product being produced.
Monitor and approve employee time & attendance records.
Monitor and direct daily production activities.
Monitor and drive the cross-skilling of all - Shift leaders & Operators.
Monitor and ensure efficiency of plant equipment and resources.
Monitor and record downtime of all equipment.
Monitor and report current input / output specifications.
Monitor emaply performance and make recommentations.
Monitor employee attendance.
Monitor scheduling and make adjustments based on needs.
Monitor shop floor safety.
Monitors operations to meet pre-established production and quality standards.
Monitor staffing on the floor and recommend staffing changes as required.
Monitor standard of work and provide support or training where required.
Monitor the line for any safety issues (i.e. Ergonomics, guarding etc.).
Monitor the performance of your team to ensure that targets and objectives are met in full.
Motivate
Motivate and lead team members; and coordinate with support groups to accomplish area objectives.
Motivate production staff.
Motivate and energizes personnel to obtain top performance.
Motivate staff and create fun work environment.
Organize
Organize and complete work as scheduled.
Organize and lead the focus on improved productivity.
Oversee
Oversee and ensure proper sanitation procedures for all plant (HACCP, Safety Food policies, etc.).
Oversee distributor pick-ups.
Oversee project calendars of the shows in development and production.
Oversees lean implementation program identifying wastes and improving efficiencies.
Oversee staff and ensure smooth, and QUICK workflow.
Oversee the training of new employees and when assigning new tasks.
Oversee the production of delicious meals (>.
Oversee the purchase and use of any tools, or supplies used in various areas.
Participate in
Participate in and support the Health & Safety Committee in the fulfilment of its mandate.
Participate in emergency response drills and be part of the plant Emergency Response Team.
Participate in establishing, monitoring, and achieving plant operational targets and goals.
Participate in his area Quality / Safety investigations, changes & ensure implanting actions on time.
Participate in new-product-launch meetings.
Participate in Operational Health & Safety Committee meetings / events.
Participate in performance management including progressive discipline when required.
Participate in the QRMP audit and assist in the development of procedures and corrective actions.
Perform
Perform activities of workers supervised.
Perform basic equipment maintenance.
Perform duties of the assigned employees when necessary.
Perform key communication role between customer service, purchasing and production departments.
Perform other duties as assigned by immediate supervisor and upper management.
Perform professional or management work regularly across multiple Manufacturing disciplines.
Perform regular process observations and conducts root cause analysis for variances.
Plan
Plan, organize, integrate, and measure work performed within the department.
Plan and coordinates work, trains and motivates, monitors and evaluates performance of associates.
Plan daily work schedules.
Plan for production operations.
Plan schedules for teams.
Prepare
Prepare and conduct team meetings as necessary for proper communications and development of teams.
Prepare and submit daily reports on production, individuals, and overall shift performance.
Prepare exemptions report documents when necessary.
Prepare management reports for the Production Manager.
Prepare inventory and production reports.
Prepare the production plan daily and schedule work for at least one week ahead of schedule.
Provide
Provide assistance with training and demonstration on lean tools and methodology.
Provide candid feedback on expectations and performance to all members of team on regular basis.
Provide challenging work assignments and development opportunities.
Provide daily feedback to workers on performance and conduct performance reviews with direct reports.
Provide guidance and feedback for team members in accomplishing tasks and goals.
Provide leadership, direction and coaching to hub associates regarding production activities.
Provide managerial support to assure environmental issues are addressed.
Provide overall support to shift teams and plant production personnel.
Provide program management support as required.
Provide recommendations to management regarding procedural and organizational changes.
Provide supervision and leadership for the training of hourly employees.
Provide technical / operational advice to project teams.
Provide training and guidance to manufacturing staff.
Recommend
Recommend measures to improve production methods, equipment performance and quality of product.
Recommend measures to improve production methods, equipment performance and quality of products.
Recommend personnel actions such as hiring and promotions.
Recommend and implement continuous improvement ideas.
Recommend improvements to production methods, equipment performance and quality of product.
Recommend opportunities for improved efficiency and performance.
Recommend process improvements and supports.
Recommend staffing deployment and operating improvement in work methods, standards and procedures.
Report
Report any non-compliance or missed deadlines.
Report food quality related issues to the supervisor.
Report safety issues and accident investigations in a timely manner.
Report out on incidents / accidents, supports investigations and corrective actions.
Report recurring performance issues to their Manager.
Resolve
Resolve conflicts where identified.
Resolve worker grievances or submit unsettled grievances to Human Resources Manager for action.
Review
Review and assist in the follow-up on any Good Manufacturing Practices or production audit items.
Review, and submits all training documentation to the department manager for review and approval.
Review, improve, and maintain SSOPs and Written Instructions.
Review requirements to make sure you have them before applying.
Review the production schedule, scrap, downtime and quality results.
Revise schedules and manage rush and special orders as needed.
Schedule
Schedule and cover weekly and weekend overtime when required.
Schedule equipment and employees to ensure production requirements are met on time.
Schedule repair, maintenance, and installation to ensure continuous production operations.
Set
Set production team goals, and facilitate team meetings.
Sets and achieves challenging goals.
Set and achieves performance standards with regards to safety, line utilization and quality.
Set clear performance standards and hold people accountable for results.
Set team goals and ensure POs are on schedule.
Supervise
Supervise and assist technical and workflow issues for English Editors and Coordinators.
Supervise and coordinate activities of machine operators on their assigned shifts.
Supervise and ensure that product is ready for scheduled deliveries.
Supervise and manage ALL operations on 2nd shift.
Supervise and manage employees and all aspects of production activities during assigned shift.
Supervise and oversee 40-50 employees.
Supervise a production team composed of approximately 10 forklift operators.
Supervise daily activities and personnel engaged in manufacturing of products.
Supervise output and maintain production rates set forth for all machines.
Supervise production line operation in accordance with plant policies and procedures.
Supervise 8 - 20 hourly employees in a manufacturing environment.
Supervise all functions of the work area including safety and training.
Supervise and coordinates activities of workers engaged in molding.
Supervise direct reports and ensures training needs are met and Ensure proper staffing of all line.
Supervise subcontractors and crews to implement uniform and efficient building procedures.
Supervise the assembly, disassembly, cleaning, and storage of manufacturing equipment.
Supervise the regrind department.
Supervise the activities of associates in Service Bureau production department.
Supervise the checking of outgoing and incoming freight for proper counts and codes.
Supervise the starting process of production lines.
Supervise, train and mentor operators & material handlers on scheduled shift.
Supervise up to 10 employees in production.
Support
Support and represents directives from the studio and / or production leadership.
Support classified needs from a staffing and execution standpoint for all mechanical operations.
Support Corrective and Preventive Action (CAPA) investigations, planning and implementation.
Support, enforces and complies with all company policies and procedures.
Support everyone s efforts to succeed.
Support product development in producing "sample” products.
Support quality system expectations; and ensure adherence to cGMPs.
Support sales team with management of promotional, trade show & POS material or equipment.
Support SQF requirements and QA department.
Support the company business plan.
Support the development maintenance programs for process equipment systems.
Support the Shipping Manager by completing visual performance board.
Track
Track employee performance & productivity goals and communicates status to the Production Manager.
Track productivity week to week for measured shift efficiency and improvement.
Train
Train and evaluate employee job duties.
Train new employees and report on their progress to The Production Manager.
Train or arrange for training.
Trais hourly machine operators, trainers and team leaders.
Train staff / workers in job duties, safety procedures and company policies.
Train subordinates to properly perform their job.
Troubleshoot
Troubleshoot process and operations problems utilizing structured problem-solving techniques which.
Troubleshoot and correct product defects and line problems.
Troubleshoot work problems with employees.
Understand
Understand and adhere to Good Manufacturing Practices.
Understand steel powder paint preparation processes, blasting and related surface prep.
Understand the needs of the business to run or shut down production lines.
Understand the technical infrastructure, hardware, processes, and offerings of key customers.
Understand workload and balance personnel to accommodate production schedule.
Update
Update and assess employee-training matrix at all times.
Update and maintain tracking documents and work management tools.
Update the Oracle (ERP) system transactions.
Verify
Verify daily / weekly results and communicate to all associates.
Verify production planning and manage priorities.
Verify the availability of equipment, material, and personnel and identify production priorities.
Work with
Work with and support other department goals.
Work with engineering to ensure that processes are robust and monitor processes per standard work.
Work with fellow line supervisors on cross skilling operators across other production lines.
Work with HR and plant personnel to ensure fairness and consistency and workplace harmony.
Work with Maintenance Leader and shift mechanics regarding mould and machine maintenance.
Work with Payroll Manager to define standards and best practice processes.
Work with planning and purchasing as well as program management to understand upcoming work.
Work with Planning to balance factory plan and resources.
Work with quality to proactively analyze trends for process improvements.
Write
Write and conduct yearly performance reviews.
Write clearly and informatively.
Write work orders, downtime reports, changeover forms, employee reviews.
Most In-demand Hard Skills
The following list describes the most required technical skills of a Production Supervisor:
Supervisory
Manufacturing Environment
MS Excel
MS Word
Lean Manufacturing
Microsoft Office
Outlook
Management
Operations Management
Food Science
Safety
SAP
HACCP
Line Management
Production
Mechanical Aptitude
Supervisory / Management
Project Management
Quality
Business Administration
Continuous Improvement
Gsuite
MS Powerpoint
Production Environment
Computer Literacy
Logistics
Process Improvement
Most In-demand Soft Skills
The following list describes the most required soft skills of a Production Supervisor:
Written and oral communication skills
Leadership
Interpersonal skills
Organizational capacity
Problem-solving attitude
Analytical ability
Time-management
Planning
Attention to detail
Accountable
Bilingualism
Critical thinker
Coaching
Embrace new ideas
Initiative
Consistency
Follow-through
Work effectively
Self-motivated
Flexible
Autonomous
Results-oriented
Team spirit
Team player
Quickly changing environment
Conflict resolution
Multi-task
Teamwork
Work with minimum supervision
Detail-oriented
Management
Decision-making skills
Team leadership
Collaborative
Integrity
Priority management
Work under pressure
Work in a fast-paced environment
Think independently
Accuracy in work