Main Responsibilities and Required Skills for Materials Manager
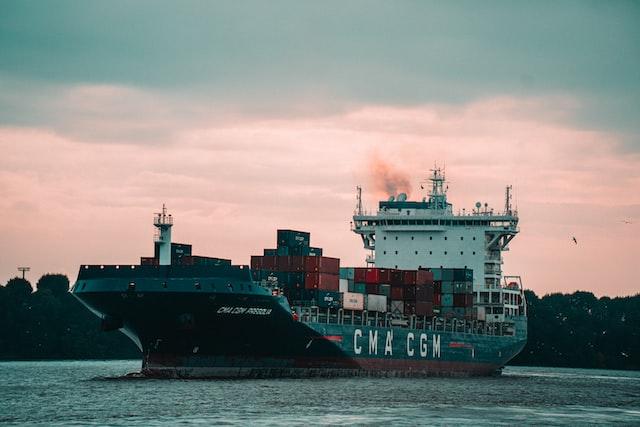
A Materials Manager is responsible for developing and implementing materials handling procedures. They plan and coordinate activities to schedule, procure, receive, and store materials and optimize material flow. In this blog post we describe the primary responsibilities and the most in-demand hard and soft skills for Materials Managers.
Get market insights and compare skills for other jobs here.
Main Responsibilities of Materials Manager
The following list describes the typical responsibilities of a Materials Manager:
Address
Address issues with employees and coworkers, as needed.
Analyze
Analyze inventory levels and work close with stakeholders to reduce inventory.
Analyze part specifications to resolve spec errors.
Assess
Assess and mitigate risk with regard to material development / selection.
Assist in
Assist Faculty and external instructors in preparing materials for online and distributed education.
Assist in development and continuous improvement of plant layout.
Assist in evaluating surgical supplies and equipment.
Assist in the evaluation of the effectiveness of designed materials.
Assist in the turnover of the operating room suites between cases.
Balance
Balance tactical day to day materials management with proactive future improvements.
Build
Build and maintain collaborative, working relationships with suppliers.
Calculate
Calculate and review annual KPI targets.
Capture
Capture pre-season and seasonal development costs related to raw materials.
Change
Change approach or method to best fit the situation.
Collaborate with
Collaborate to create the best outcome for our customers.
Collaborate with other managers to determine supply needs.
Communicate
Communicate and issue complaints to vendor and ensure corrective action and reimbursement.
Communicate effectively with others verbally and in writing.
Communicate materials team future state vision and executes development plans.
Complete
Complete annual reviews for staff and provides disciplinary action when necessary.
Consult
Consult clients on comprehensive Materials Management and Inventory Management Strategies.
Control
Control personnel, including performance management and team development.
Coordinate
Coordinate and supervise receiving and warehousing procedures.
Coordinate material allocation and consignment to maintain efficient inventory levels.
Coordinate materials management issues with Contractors, Suppliers, Client and project personnel.
Coordinate with customers, purchasing, project managers, operations managers and warehouse managers.
Create
Create and maintain optimal inventory stocking levels, ensuring product availability to all labs.
Create purchase orders for supplies and equipment as required.
Create Standard Operating Procedures for employee usage.
Create strategic solutions to improve material flow at multiple levels.
Deliver
Deliver top results in hours and days instead of weeks and months.
Develop
Develop a highly capable materials management function.
Develop and execute inventory cycle count process to assure high inventory accuracies.
Develop and implement a professional development program for materials personnel.
Develop and implement materials handling procedures.
Develop and maintain a plan for every part (PFEP) database.
Develop and maintain material and inventory control systems.
Develop and maintain metrics to evaluate performance of supply chain and production partners.
Develop and Maintain relationships with Suppliers.
Develop and manage inbound freight logistics.
Develop and manages critical performance goals (material.
Develop departmental best practices for delivering remote / distributed content.
Develop E&O processes including reporting and disposition.
Develop facility production schedule to achieve optimum operating cost and labor efficiency.
Develop, implement and maintains policies, procedures and material control systems.
Develop production and inventory control skills of the team.
Develop production plans that balance customer requirements and demonstrated capabilities.
Develop strategies for cost savings for all direct material purchasing.
Direct
Direct and supervise Shipping / Receiving along with Plate / Assembly / Pack.
Direct the processing and placement of all production and non‑production requisitions.
Drive
Drive cost efficiencies and timely, quality of supply.
Drive lean methodologies for warehouse management, inventory levels, and materials flow.
Drive operational saving initiatives in inventory and storage.
Drive quarterly Finance review on E&O analysis and disposition.
Drive continuous improvement to material and information flow.
Drive deviation authorizations through system approvals.
Encourage
Encourage everyone around them to to be tenacious and never settle.
Enforce
Enforce company and safety rules, document violations and propose necessary disciplinary actions.
Engage
Engage employees and involve them in the business.
Enhance
Enhance customer service levels possible by balancing supply and demand.
Ensure
Ensure all employees under his or her supervision receive all mandated safety training.
Ensure appropriate learner access to resources.
Ensure inventory levels are sufficient to meet customer requirements and timelines.
Ensure inventory management plans achieve Corporate targets.
Ensure materials team is fully trained on ERP / MRP system and utilizes it to the fullest capability.
Ensure private data is handled according to UBC Data Privacy and Security guidelines.
Ensure project teams are fully compliant with any materials scope of work.
Ensure prompt and accurate updating of the computer systems.
Ensure that finished goods inventory levels are within the min / max targets.
Ensure that new employees are trained on department hazards and safe operation of equipment.
Ensure that production requirements and schedules are properly communicated to the production floor.
Ensure there is an effective process for supplier selection across the business.
Ensure the submissions meet tight deadlines.
Establish
Establish and maintains levels and related controls of supplies and equipment for the Center.
Establish and maintains PAR stock levels in all areas, with the cooperation of staff members.
Establish and maintain strong relationship with customer.
Establish a procedure to archive material and provide access to learners when required.
Establish procedures for conducting and valuing year-end inventory.
Evaluate
Evaluate and trains shift personnel using on the job training methods.
Execute
Execute / monitor Material Requirement Planning calculations and messages.
Execute strategic direction on a tactical level, manages a team, develops site's supply policies.
Facilitate
Facilitate progress and enable optimization, both in terms of process and the way we work.
Facilitate the local SIOP process.
Generate
Generate annual cost savings in storage and inventory value.
Hire
Hire, train, develop and evaluate staff on a timely basis and in accordance with company policy.
Identify
Identify and study problems relative to the flow of supplies.
Identify material planning, MRP, and Kanban training.
Identify recurring issues related to the management of curriculum materials.
Identify and mitigate any supplier risks, ensuring there are ‘Plan Bs' in place.
Implement
Implement a Continuous Improvement Plan.
Implement Key Performance Indicators (KPIs) and enhance them as the business requirements change.
Influence
Influence material availability improvement activities throughout the organization.
Initiate
Initiate disciplinary action if necessary.
Inspire
Inspire the trust of others.
Keep
Keep abreast of industry standards, regulations, and laws applicable to the material controls.
Keep detailed records on procurement activity, materials quantity, specifications etc..
Lead
Lead a cross functional local process around innovation and new product development.
Lead and manage annual inventory process as well as auditing plant scrap.
Lead, manage, and direct all materials related processes.
Maintain
Maintain and upgrade applicable job skills as identified and required.
Maintain build plans for Engineering validation, NPI, and sustaining production.
Maintain consistent leadership for materials planning and inventory.
Maintain knowledge base and utilization of contract pricing, keeping current.
Maintain relationships and negotiate with suppliers.
Maintain relationships with suppliers and drive resolution of delivery issues.
Maintain supplier relationships.
Manage
Manage accurate inventory records for all parts within Android's ERP system (QAD).
Manage activation and deactivation of part numbers.
Manage all aspects of Shipping and Receiving and inside / outside warehouse operations.
Manage and monitor the activities of subordinates accuracy and integrity of all materials.
Manage and order Sanitation items as needed.
Manage Data input and analysis of material usage, supplier and COO shifts.
Manage engineering change process.
Manage inventory at all locations.
Manage issues for determination and resolution.
Manage master data accuracy within the systems (e.g. SAP / Excel).
Manage material level testing with both YETI internal and external testing labs.
Manage material movement from vendors and across multiple manufacturing locations.
Manage Materials and Distribution personnel.
Manage materials planning to support production and new product launches.
Manage members of the Raw Material Management group.
Manage monthly and annual physical inventories at all supported sites.
Manage organization and company policies, procedures and material control systems.
Manage reporting, budgets and KPI metrics for regional sales and marketing activities.
Manage scrap business for all PPHC facilities.
Manage suppliers, materials and inventory.
Manage the data and maintain the Bill of Material Database.
Manage the Material Review Board to ensure timely transactions of material movements.
Manage the staffs daily schedule, and operational changes.
Manage warehouses and warehouse staff.
Minimize
Minimize inventory levels on balance out parts.
Monitor
Monitor and control the fiscal expense budget of the Materials Department.
Monitor and measure supplier performance.
Monitor material flow between Suppliers, Android, and the customer.
Monitor operations in assigned areas to keep expenditures within acceptable budget limits.
Monitor progress to the shipping targets.
Monitor the 'MRP to consumption' flow of materials from receipt to issuance.
Negotiate
Negotiate blanket / reoccurring orders, etc. with long-term suppliers.
Negotiate to yes and finds win-win outcomes to complex supply problems.
Operate
Operate and execute with an extreme sense of urgency.
Optimize
Optimize material flow and customer readiness.
Oversee
Oversee distribution of supplies in the organization.
Oversee management and updates of the digital and physical fabric library.
Oversee MRP (material requirement planning) and DRP (distribution requirements planning).
Oversee and supervise Production Controllers / Schedulers and Cycle Counter.
Oversee traffic, purchasing, planning, and logistics staff.
Own
Own and manage excess and obsolete inventory (E&O) to minimize financial impact.
Perform
Perform impact analysis on BOM changes relating to assigned commodities.
Perform regular assessment and updates to existing online modules and educational materials.
Perform regular workplace inspections.
Plan
Plan and coordinate activities to schedule, procure, receive, and store materials.
Plans manage, and maintain department budget.
Plan, organize, direct, and control activities related to manufacturing related procurement.
Prepare
Prepare annual department staffing and expense budgets.
Prepare reports on inventory, material usage and efficiency.
Procure
Procure all raw and packaging materials for the plant.
Provide
Provide coaching and training support to team to create a positive working environment.
Provide for the proper shipping and documentation of finished goods.
Provide leadership and direction to assist the team in creating high-quality raw materials.
Provide leadership, coaching and development for a dedicated Purchasing team of four.
Provide leadership, direction and execution of asset performance.
Provide part time cover for material scheduling team.
Provide purchasing support to internal teams.
Provide timely feedback to Management of potential supplier delivery and quality problems.
Purchase
Purchase supplies and materials according to specifications.
Read
Read / understand required cleaning schedule at the start of every shift.
Recommend
Recommend disposition within established guidelines.
Remain
Remain continuously cognizant of supplier delivery performance.
Report
Report and develop reporting structure for all direct material throughout PPHC.
Represent
Represent the company in Client's workshops and Meetings.
Resolve
Resolve labor and material shortages, backlogs and other potential schedule interruptions.
Review
Review and set ABC and safety stock schedule.
Review calculated weekly schedule adherence.
Review, identifies, and minimizes obsolete inventory.
Review, plans and approves purchase orders and change notices.
Review purchase order claims and contracts for conformance to company policy.
Run
Run external team meetings with CMs and suppliers to align build schedules.
Schedule
Schedule / maintain deliveries to optimize receiving of material.
Set
Set and monitor site strategic inventory holding targets and spend by area.
Set blanket orders annually for vendors who qualify.
Supervise
Supervise and review the work of materials engineering technicians and other team members.
Support
Support Quality Assurance to qualify and manage suppliers of materials.
Support SAP activities to assure the End to end process flows properly.
Support team with Receiving Dock, Shipping Dock, and material storage issues.
Take
Take decisive action, and confidently changes course if unsuccessful.
Travel
Travel to client sites, both onshore and offshore, as required.
Troubleshoot
Troubleshoot different issues based on data analytics.
Understand
Understand and skilled at managing manpower, machines and materials.
Understand various sets of data for quality & process control and decision-making process.
Understand Warehouse and Purchasing requirements for SOX controls.
Use
Use honest communications.
Use of relevant data & analytics.
Use thinking and reasoning to solve problems.
Validate
Validate Fabric data on PLM and ensure approvals on time.
Work with
Work with customers and category managers to identify appropriate inventory levels.
Work with Global Technical packaging community for sharing practices, building common processes.
Work with leadership team members to support company and facility goals.
Work with technical and quality resources to establish secondary sources of supply for material.
Work with the team to develop recovery and / or gap closure plans.
Most In-demand Hard Skills
The following list describes the most required technical skills of a Materials Manager:
Business
Manufacturing
MRP
Most In-demand Soft Skills
The following list describes the most required soft skills of a Materials Manager:
Written and oral communication skills
Problem-solving attitude
Analytical ability
Leadership
Interpersonal skills
Organizational capacity
Flexible
Management
Negotiation
Team player
Time-management