Main Responsibilities and Required Skills for a Manufacturing Production Manager
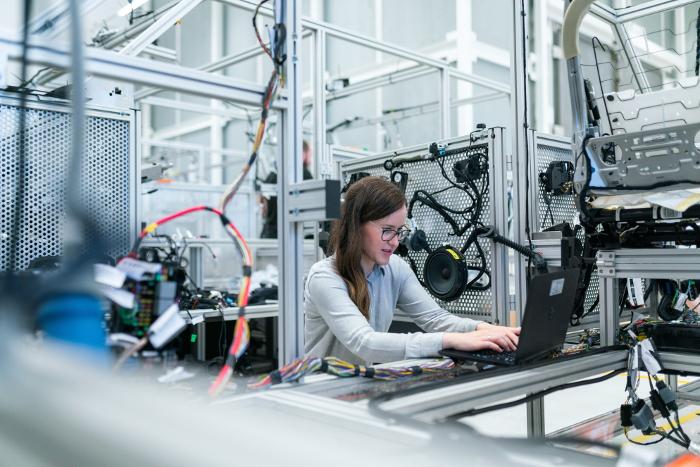
A Manufacturing Production Manager is a professional who oversees and manages the production processes within a manufacturing facility. They are responsible for planning, coordinating, and optimizing production operations to ensure efficient and timely delivery of products. In this blog post, we will describe the primary responsibilities and the most in-demand hard and soft skills for Manufacturing Production Managers.
Get market insights and compare skills for other jobs here.
Main Responsibilities of a Manufacturing Production Manager
The following list describes the typical responsibilities of a Manufacturing Production Manager:
Address
Address employees' issues or grievances.
Administer
Administer plant policies in a fair and consistent manner.
Allocate
Allocate resources effectively and fully utilize assets to produce optimal results.
Analyze
Analyze and manage work order releases with respect to capacity planning and material requirements.
Analyze production data and generate reports for management review.
Collaborate with
Collaborate with engineering and maintenance teams for equipment maintenance and repairs.
Collaborate with leadership.
Collaborate with shipping staff and scheduling to resolve issues that arise.
Collaborate with the research and development team for new product introductions.
Collect
Collect and analyze data to find places of waste or overtime.
Commit
Commit to plant safety procedures.
Communicate with
Communicate with internal and external customers and vendors regarding ongoing operations.
Conduct
Conduct other responsibilities as required by management.
Conduct performance evaluations and provide feedback to production staff.
Conduct regular inspections to ensure adherence to quality standards.
Coordinate with
Coordinate with purchasing to source and purchase materials for jobs.
Coordinate with shipping for the incoming materials and outgoing orders.
Coordinate with suppliers and vendors to ensure timely delivery of materials.
Coordinate with various departments to ensure timely availability of resources and materials.
Create
Create, update, review, and maintain production-related SOPs.
Design
Design fixtures and manufacturing tools.
Develop
Develop and implement training programs for production staff.
Develop and manage budget performance for areas of responsibility.
Develop equipment maintenance schedules and recommend the replacement of machines.
Develop production plans and schedules to meet customer demands.
Develop production schedules and maintain an inventory of raw materials and finished products.
Develop schedules and manpower requirements for assigned areas.
Drive
Drive continuous improvement initiatives in production processes.
Ensure
Ensure all production operations meet established quality standards.
Ensure all SOP's and GMP's related to both device and reagent manufacturing are followed.
Ensure assigned areas have all necessary resources, tools, equipment, and supplies.
Ensure compliance with health, safety, and environmental regulations.
Ensure compliance with production schedules and deadlines.
Ensure manning in assigned areas is adequate to support production requirements.
Ensure optimal performance.
Ensure records of critical process parameters and documentation are maintained.
Ensure target production numbers are met and cGMP documents are completed in a timely manner.
Establish
Establish a working environment that fosters participation within and between teams.
Establish operational plans and implement policies and strategies.
Evaluate
Evaluate and maintain new and existing manufacturing equipment.
Evaluate and recommend process improvements and automation opportunities.
Follow
Follow all companies policies and procedures.
Foster
Foster a positive and motivating work environment for production teams.
Hire
Hire, train, develop, discipline and discharge production operators and engineers.
Identify
Identify and implement continuous improvement opportunities.
Identify and resolve production issues and bottlenecks.
Identify, implement, and track improvements in safety, quality, delivery, cost, and morale.
Implement
Implement and maintain production documentation and records.
Implement and monitor key performance indicators (KPIs) for production processes.
Implement and monitor quality control measures to achieve product standards.
Implement and optimize production workflows and procedures.
Implement lean manufacturing principles to improve efficiency and reduce waste.
Interact
Interact with vendors and suppliers.
Lead
Lead teams from vendors and other functional areas).
Lead the continuous improvement of production operations and procedural documentation.
Lead the execution of the validation master plan for newly transferred or existing products.
Lead the on-going analysis and support of newly transferred and existing products.
Maintain
Maintain appropriate inventory of production supplies and materials.
Maintain a safe environment by ensuring all safety regulations and rules are followed.
Maintain a safe working environment by complying with procedures, rules, and regulations.
Maintain / assist in the development of records.
Maintain plant safety and housekeeping standards.
Make
Make budgetary recommendations on capital expenditures and direct / indirect labor.
Manage
Manage and coordinate daily production activities.
Manage inventory levels to optimize production and minimize stockouts.
Manage maintenance, turnover, and availability of inventory to meet production demands.
Manage team of production operators and engineers.
Monitor
Monitor and control production budgets and expenses.
Monitor and control production costs to meet budgetary requirements.
Monitor production processes to ensure efficiency and quality.
Optimize
Optimize production layouts and workflows for maximum efficiency.
Organize
Organize and lead initial and on-going training of new and existing personnel.
Participate in
Participate in and / or lead investigations, root cause analyses, and action plans.
Participate or lead product tech transfer to outsource partners.
Plan
Plan and administer procedures and budgets.
Plan and implement changes to machinery and equipment, production systems and methods of work.
Plan and manage the establishment of departmental budget.
Plan, organize, direct and run optimum day-to-day operations to exceed our customers expectations.
Plan, organize, direct, control and evaluate daily operations.
Propose
Propose modifications to functional operating policies and day-to-day processes.
Provide
Provide tactical and / or operational leadership and coaching.
Read
Read blueprints and drawings.
Receive
Receive assignments in task and objective oriented terms.
Recommend
Recommend and aids in the implementation of production line efficiencies.
Represent
Represent manufacturing on launch teams focused on design and process transfer.
Resolve
Resolve conflicts and address employee concerns in a timely manner.
Revise
Revise production schedules and priorities as result of equipment failure or operating problems.
Schedule
Schedule and oversee maintenance and repairs to all production equipment and production facilities.
Schedule the production of jobs (based on incoming of raw materials) and provide lead time on jobs.
Select
Select and develop personnel to ensure the efficient operation of the production function.
Set
Set production goals and targets to meet operational objectives.
Share
Share a trusting relationship with workgroup and recruit, manage and develop plant staff.
Stay updated on
Stay updated on industry trends and advancements in manufacturing technology.
Stay up to date with latest production management best practices and concepts.
Strive
Strive for continuous improvement and consistency in deliverables.
Supervise
Supervise and provide guidance to production staff.
Supervise the assembly, disassembly, cleaning, and storage of manufacturing equipment.
Supervise the cleaning of the clean room facility.
Use
Use the ERP system to forecast and plan upcoming needs.
Utilize
Utilize tools like Gage R& R, Cp, Cpk, and SPC to improve processes.
Write
Write reports and protocols.
Most In-demand Hard Skills
The following list describes the most required technical skills of a Manufacturing Production Manager:
Proficiency in production planning and scheduling software.
Strong knowledge of manufacturing processes and techniques.
Experience with lean manufacturing principles and methodologies.
Knowledge of quality management systems, such as ISO 9001.
Familiarity with production data analysis and reporting tools.
Proficiency in using enterprise resource planning (ERP) systems.
Understanding of supply chain management principles.
Knowledge of manufacturing cost analysis and control.
Experience with production optimization and process improvement techniques.
Proficiency in using computer-aided design (CAD) software.
Familiarity with product lifecycle management (PLM) systems.
Knowledge of safety regulations and procedures in manufacturing environments.
Experience with production equipment maintenance and troubleshooting.
Understanding of Six Sigma methodologies and tools.
Proficiency in using statistical analysis software, such as Minitab.
Knowledge of regulatory compliance in manufacturing, such as OSHA standards.
Familiarity with automation and robotics in manufacturing.
Understanding of production line balancing and capacity planning.
Proficiency in using productivity and efficiency tracking tools.
Knowledge of material requirements planning (MRP) systems.
Most In-demand Soft Skills
The following list describes the most required soft skills of a Manufacturing Production Manager:
Strong leadership and team management abilities.
Excellent communication and interpersonal skills.
Problem-solving and decision-making capabilities.
Ability to work under pressure and meet tight deadlines.
Strong organizational and time management skills.
Attention to detail and commitment to quality.
Analytical thinking and data-driven mindset.
Adaptability and flexibility in a dynamic manufacturing environment.
Collaboration and teamwork abilities.
Effective conflict resolution and negotiation skills.
Conclusion
Manufacturing Production Managers play a crucial role in ensuring the smooth and efficient operation of production processes. By possessing a combination of technical expertise, strong leadership, and effective communication skills, these professionals contribute to the success and competitiveness of manufacturing companies.