Main Responsibilities and Required Skills for Manufacturing Manager
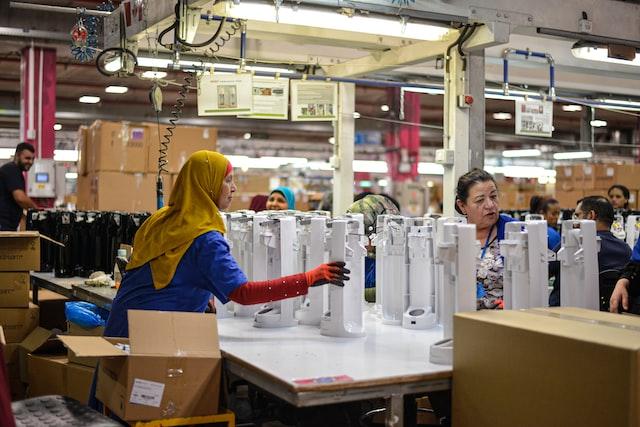
A Manufacturing Manager is a professional who leads, manages, trains, and develops production employees. They implement and administer production policies and plans and ensure quality standard are met. In this blog post we describe the primary responsibilities and the most in-demand hard and soft skills for Manufacturing Managers.
Get market insights and compare skills for other jobs here.
Main Responsibilities of Manufacturing Manager
The following list describes the typical responsibilities of a Manufacturing Manager:
Adhere to
Adhere to and enforces Occupational Health and Safety Act, Laws, Rules and Regulations.
Allocate
Allocate material, human and financial resources to implement organizational policies and programs.
Analyze
Analyze and reports to the General Manager on the effectiveness of plant manufacturing operations.
Analyze market conditions to identify new business opportunities and strategies.
Analyze workforce requirements.
Analyze work processes to ensure that staff capacity and equipment utilization are maximized.
Approve
Approve and oversee all sales / shipping orders.
Assess
Assess the skill sets and capabilities of areas of responsibility.
Assist in / Assist with
Assist Engineering team with the launch of new products into manufacturing.
Assist General Manager in forecasting manpower requirements.
Assist General Manager in forecasting manpower requirements, scheduling and overtime.
Assist Human Resources with recruitment and training of new employees.
Assist in quoting new custom and proprietary business.
Assist in resolving operational issues found during process testing.
Assist in supervisory training to maintain competence.
Assist in the development of standard product lines.
Assist the Marketing team to develop and implement new products along with marketing strategies.
Assist with the development of the Snacks internal Co-Man strategy and objectives.
Assure
Assure continuity and synergy of activities and projects between all the different shifts.
Assure the continuous improvement of processes, mainly by using problem solving tools.
Coach
Coach, Mentor and provide guidance.
Coach, manage and develop technical staff.
Conduct
Conduct a monthly report on staffing, manufacturing, safety, and costs.
Conduct equipment evaluation and recommends acquisition of new equipment.
Conduct and participate in staff meetings.
Conduct performance appraisals and provide coaching and guidance to all operations staff.
Confer
Confer with clients to determine design needs.
Coordinate
Coordinate action plans with Quality to ensure customer requirements are achieved.
Coordinate hand-offs between Assembly, Test, Paint, and QA to obtain green tags.
Coordinate internal and external resources to address issues and secure the supply chain.
Coordinate plant equipment final commissioning and start-up, first articles testing.
Coordinate pricing actions.
Coordinate schedule status and changes with planners daily.
Coordinate production activities with other departmental activities in Company.
Coordinate strategic initiatives as well as cost reduction initiatives.
Coordinate with field quality to ensure quality policies are met.
Create
Create and promote culture of safety within each department.
Define
Define and communicate overall vision and cascaded manufacturing objectives.
Determine
Determine amount of necessary resources.
Determine and set inventory levels.
Determine key deliverables, introduction schedules and processes that need to be put in place.
Develop
Develop and identify potential areas for operations process improvement.
Develop and implements daily schedule for each department.
Develop and Maintain company safety plan.
Develop and monitor Engineering department budget to achieve best results.
Develop and / or approves all plant operating policies.
Develop contracts for product orders with the CM.
Develop equipment maintenance schedules and recommend the replacement of machines.
Develop inventory controls.
Develop key performance standards and quality monitoring of our products.
Develop plans for efficient use of materials, machines, and employees.
Develop production schedules and maintain an inventory of raw materials and finished products.
Develop QA / QC standards, oversee implementation, and monitor ongoing performance to standards.
Direct
Direct quality control inspections.
Direct supervision of Manufacturing Supervisors, Scientists and Technicians.
Draft
Draft new procedures and / or changes to SOP's to keep current or improve cGMP status.
Drive
Drive continuous improvement of engineering technical capabilities.
Drive overall improvements based on data from our OEE and Tableau systems.
Enable
Enable and assure collaboration across manufacturing areas, and shifts.
Enforce
Enforce production schedule by strategically allocating time and labor.
Ensure
Ensure all employee matters are handled in accordance with collective agreements.
Ensure all production activities comply with GMPS and regulatory requirements.
Ensure a safe work environment consistent with OSHA requirements and Abbott.
Ensure business adherence to contractual agreements.
Ensure compliance to policies, procedures and functional performance.
Ensure compliance to those processes, improve and revise processes as required.
Ensure daily production objectives, Ensure on-time delivery of post-cast departments.
Ensure lessons learned are implemented in future projects.
Ensure planned KPI's of efficiency and performance are met or exceeded.
Ensure project documents are complete.
Ensure quality standard are met.
Ensure safe working conditions within manufacturing.
Ensure teams are focused on continuous improvement to enhance team competences.
Ensure that management trust is not violated.
Ensure that Manufacturing operational capacity is maintained to meet the production forecast.
Ensure that relevant regulations are met and the production schedule is attained.
Ensure that the facility conforms to local, provincial, and federal government regulations.
Ensure the Company provides a safe and clean work environment at all times.
Ensure the team leads read customer specifications for all projects being built.
Ensure the utilization of the Company's e-maintenance software.
Ensure timely and accurate transfer of information with the suppliers.
Establish
Establish and maintain contact with suppliers.
Establish, communicate, implement and enforce safety programs and procedures.
Establish hiring practices and 30 / 60 day reviews.
Establish plant short and long-range strategic operating objectives.
Evaluate
Evaluate existing personnel, guide them, make changes if necessary and perform hiring functions.
Facilitate
Facilitate delivery of manufacturing training.
Help
Help determine time required to process different types and sizes at various stages of production.
Help establish budgets for operations and corporate plans for short, medium, long terms.
Hire
Hire and retain a diverse, highly qualified staff and provides ongoing performance feedback.
Hold
Hold regular staff meetings to ensure specific project goals and company goals are being met.
Identify
Identify training needs.
Identify and implement continuous improvement projects for area safety and efficiency.
Identify and recommend product improvements.
Identify, share and replicate best practices across the internal and external supply chain network.
Implement
Implement all build schedules determined by Evolv's Executive Team.
Implement and administer production policies and plans, adapting plans and priorities as necessary.
Implement and manage resource planning and project management tools.
Implement inventory policies and strategies in line with business growth strategies.
Improve
Improve overall performance of the technical team by measurable standards.
Influence
Influence and support senior leaders and key stakeholders across the Snacks business.
Input
Input to design and transfer of new products.
Inspect
Inspect equipment health and schedule maintenance.
Inspect machines and equipment to ensure specific operational performance and optimum utilization.
Lead
Lead employees in driving continuous improvement in processes.
Lead internal and external teams to manage cost and process improvement projects.
Lead life cycle management for existing products.
Lead team to use quality tools to do problem solving.
Liaise with
Liaise with corporate finance and procurement as required in completion of capital projects.
Maintain
Maintain a harmonious relationship with union representatives.
Maintain and improve production capacity to meet the business requirement.
Maintain an effective organization and positive working environment.
Maintain a safe and professional work environment.
Maintain conformance to budgetary limitations in all departments.
Maintain control over policy, inventory, and budget.
Maintain high ethics and values in the work place.
Maintain oversight of all inventory usage and storage.
Maintain positive and cooperative.
Maintain staffing schedule.
Manage
Manage absenteeism and turnover in each department.
Manage and evaluate machine and people resources to ensure productivity and minimal downtime.
Manage and implement cost reduction programs.
Manage both the quality and quantity of employee productivity.
Manage Co-Manufacturing packaging or raw formulation transformations and discontinuations.
Manage employees by ensuring quality, quantity, customer schedules and specifications are met.
Manage external manufacturing capacity and communicate risk and opportunities within the S& OP process.
Manage investigations for manufacturing product / process nonconformities.
Manage manufacturing services overhead and capital budgets.
Manage manufacturing support within budget constraints.
Manage material inventory and overseas component supply chain.
Manage multiple projects / priorities simultaneously and prioritize based upon business needs.
Manage project deadlines and monthly due dates.
Manage SAP transactions and information flow to EM's.
Manage small maintenance department which repairs, upgrades and installs new equipment.
Manage special projects from manager and manage / oversee subcontractors.
Manage the overall capital budget within the product category.
Manage the team of supervisors of the post cast departments.
Monitor
Monitor and evaluate project and department progress and results.
Monitor operation expenses and research ways to reduce costs while maintaining product quality.
Monitor scheduling and make adjustments based on personnel, machine issues or customer needs.
Optimize
Optimize production staffing plan to maximize effective cost structure.
Oversee
Oversee plant operations and ensures compliance with federal and state regulations.
Oversee responsibilities of supervisory staff.
Oversee the recruitment, development and performance reviews of manufacturing staff.
Own
Own customer relationships including resolution of complaints / issues / concerns that may arise.
Own and manages Department procedures and processes to maximize productivity and organization.
Participate in
Participate in and support initiatives and corrective actions related to safety.
Participate in cross-functional teams.
Participate in negotiation bids.
Participate in the ECR process, insuring proper documentation, approvals and action.
Plan
Plan and implement changes to machinery and equipment, production systems and methods of work.
Plan, organize, direct, control and evaluate daily operations.
Plan schedules, goals and objectives.
Plan production operations, routings and priorities for manufacturing products.
Prepare
Prepare departmental budgets and control expenditures to stay within spending limits.
Promote
Promote a strong safety culture in the shops.
Promote teamwork, employee morale and an overall positive work environment.
Provide
Provide all product delivery schedules and production output schedules.
Provide leadership for the successful day-to-day operation.
Provide leadership to TMVR / TAVR tissue valve engineering staff.
Provide routine communications with cross functional peers to assure awareness.
Provide support as needed for a 24 hour 7 day a week blow molding operation.
Provide technical support for mold processing and improvement.
Provide timely performance & developmental evaluations of departmental staff.
Recommend
Recommend and implement improvements to current manufacturing processes.
Report
Report progress on a regular basis to senior management.
Report safety hazards, unsafe acts, and any accidents as per company procedures.
Report team metrics and performance measurements.
Resolve
Resolve HR concerns as they arise.
Respect
Respect the values and code of ethics of the company.
Review
Review, analyze, and drive manufacturing improvements to meet aggressive client expansion plans.
Review and write production MMRs and SOPs.
Run
Run floor meetings and get commitments on production milestones and hold group leaders accountable.
Schedule
Schedule plant operation to meet production plan.
Seek
Seek constant internal as well as external "client” feedback.
Solve
Solve issues with the CM including material shortages, vendor problems and rejected materials.
Support
Support and manage any sales / marketing initiatives both administratively & fiscally.
Support client-centered delivery performance results.
Support continuing production, process development and new product introductions.
Support development testing of all assembled units, panels and data systems as required.
Support long range planning for space, equipment, and staffing needs.
Support pillar leaders in the development of the individual Pillar Strategies.
Take
Take personal responsibility for quality of products or services rendered.
Track
Track key manufacturing KPIs.
Train
Train employees on improvements such as 5S, Work Cells and Inventory accuracy.
Upgrade
Upgrade present ERP software to enable production scheduling which is done manually at present.
Use
Use of project management tools.
Walk
Walk and check the flow of the value stream daily.
Work with
Work closely with president, sales manager and office.
Work cross functionally in identifying and resolving technical issues.
Work in collaboration with Sales department to bring to market new products.
Work on the Production Floor as well as in an Office Environment.
Work with leads to match skill development of team members with project / customer needs.
Work with Production Control to meet Production Schedule.
Work with project management team to meet project needs.
Write
Write new procedures for specific production jobs.
Most In-demand Hard Skills
The following list describes the most required technical skills of a Manufacturing Manager:
Most In-demand Soft Skills
The following list describes the most required soft skills of a Manufacturing Manager:
Written and oral communication skills
Leadership
Organizational capacity
Problem-solving attitude
Interpersonal skills
Analytical ability
Attention to detail
Build positive relationships
Constructive feedback
Improve business results
Planning
Presentation