Main Responsibilities and Required Skills for Line Lead
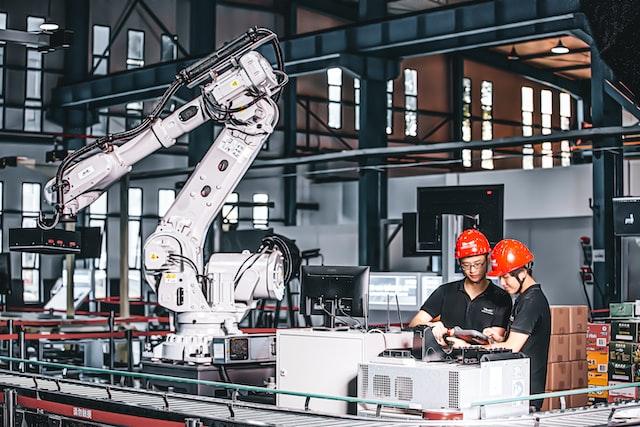
A Line Lead is a professional who has a supervisory role within a specific area or function of a business. They oversee production line, coordinate and assign tasks to the workers on the line, monitor the quality and efficiency of the production process, and ensure that production targets are met. In this blog post we describe the primary responsibilities and the most in-demand hard and soft skills for Line Leads.
Get market insights and compare skills for other jobs here.
Main Responsibilities of Line Lead
The following list describes the typical responsibilities of a Line Lead:
Address
Address performance concerns timely and professionally through appropriate disciplinary systems.
Administer
Administer a technically sound Environmental Monitoring Program, updating as appropriate.
Anticipate
Anticipate and drive proper alignment and prioritization between the lab and production teams.
Assign
Assign work to Line Workers and that they comply with policies and practices.
Assist in
Assist in maintaining an operating budget for the QA laboratories.
Assist in resource management processes and recruitment.
Assist operators on all operational equipment.
Assist with covering breaks at the line.
Assist with filler set up.
Assist with recruiting of staff and growth in Manchester office and Portland Maine office.
Assure
Assure materials are being properly handled, routed, and controlled.
Assure test methods are followed.
Attend
Attend plant MBR meetings to communicate and oversee lab issues.
Attend training's regularly.
Champion
Champion 5S and Operator Standard Work for assigned equipment.
Champion inbound freight and outbound transportation.
Champion warehouse personnel to ensure all functions are completed in an efficient manner.
Check
Check output to ensure highest quality.
Check overtime and adjust to planned hours.
Check tare weight of scale and ensure tare weight is being maintained during packaging process.
Check weight performance for over pack and B&R on line.
Clear
Clear the line of materials used on the finished run (unused labels, bags, etc.).
Collect
Collect accurate data for PRE, PROD, and POST production.
Collect all material and equipment needed to begin the process.
Communicate
Communicate and enforce company policies to workers including safety regulations.
Communicate and perform line work as assigned by the Plant Manager and / or Shift Supervisor.
Communicate these needs and work with third parties to address them.
Communicate to line personnel daily while maintaining a constant line presence.
Communicate to the Production supervisor issues with the line or personnel.
Communicate with Pour Technician to assure lines are in perfect operating condition.
Complete
Complete operational tasks in line with Standard Operating Procedures (SOPs).
Complete pre-operation inspection log on Daily Production Record.
Complete regular performance reviews utilizing clear Rapid Data (technical efficiency).
Comply with
Comply with company policies and procedures and maintains regular work attendance.
Conduct
Conduct Line Clearance as per SOP.
Conduct pre-shift huddles and provides feedback for Team Leaders.
Conduct QC tests disintegration, friability, hardness, weight variability & appearance.
Conduct regular project audits and reviews of final deliverables within the BC.
Contact
Contact Indirect Labor Material Handler to bring additional components for production line as needed.
Contact with vendors and / or their technical support staff.
Control
Control and implement job assignment / rotation plan for workers.
Coordinate
Coordinate activities related to shift starts and changes.
Coordinate execution of the Environmental Monitoring program.
Coordinate training and development of team.
Create
Create a positive and inclusive work environment that embraces diversity.
Create a positive work environment by developing a rewarding recognition program.
Demonstrate
Demonstrate ability to work safely.
Detect
Detect and report defective materials to the department supervisor.
Determine
Determine key differentiators that enable our value proposition.
Develop
Develop and lead execution of the Line 90-day plan to address losses and build capability.
Develop operations strategies to optimize processes and production.
Develop plans for efficient use of material, machines and labour.
Draft
Draft / deliver reports, projects, and presentations.
Drive
Drive a culture of engagement through the team and department.
Drive continuous improvement from the plant floor, providing support to associates.
Engage
Engage in drafting own goals, lead the process of development of team goals and growth planning.
Enhance
Enhance and stand for quality, integrated design, collaborative practice and design excellence.
Ensure
Ensure all employees abide by the safety regulations.
Ensure all records are completed appropriately.
Ensure
Ensure cleaning and sanitizing procedures are done correctly.
Ensure colleagues have right skills to run the line they are assigned.
Ensure completion of required training for all employees.
Ensure compliance with all HR policies and procedures.
Ensure disposition of finished goods in accordance with the California Operation.
Ensure Health & Safety standards are maintained.
Ensure labour standards are met and applied on the line.
Ensure pallets are neatly stacked.
Ensure production runs are executed efficiently, with high quality and minimal waste.
Ensure product rotation process meets corporate guidelines.
Ensure that all required documentation for production records is completed according to policies.
Ensure that all required operator certifications are complete and current.
Ensure that products and goods manufactured meet quality standards obtainable in the industry.
Ensure that the manufacturing personnel follow the appropriate procedures.
Ensure the area meets required GMP hygiene standards.
Ensure thorough and accurate completion of new hire training and onboarding.
Ensure timely and relevant communications to and from all levels of the organization.
Escalate
Escalate production issues to Area Manager or Production Manager as needed.
Escalate production issues to Shift Lead / Production Manger as appropriate.
Exercise
Exercise general responsibility for production, equipment & personnel safety.
Exercise judgment within defined procedures and practices to determine appropriate action.
Facilitate
Facilitate others participation in the continuous improvement program.
Follow
Follow all company policies / procedures.
Follow escalation protocol to ensure timely resolution of issues.
Generate
Generate business value for the Group and deliver best-in-class solutions to our Customers.
Guide
Guide, motivate and develop direct subordinates within HR policies.
Identify
Identify and communicate some preventive maintenance needs.
Identify correct alloy material used for each operation.
Identify new local growth opportunities expanding on existing Where to Play and How to Win choices.
Identify quality problems for corrective action.
Implement
Implement and maintain standards and processes that eliminate waste throughout the department.
Initiate
Initiate, manage, and make decisions which impact production scheduling.
Initiate, manage, and make decisions which impact product quality.
Inspect
Inspect product to ensure high quality.
Inspect machines and equipment to ensure specific operational performance and optimum utilization.
Interface with
Interface with store leadership regarding inventory discrepancy and product flow issues.
Lead
Lead and drive the relationship with the key stakeholders, COE and Regional CC and ITS CC teams.
Lead and / or Execute Improvement Projects to eliminate losses with the Operation.
Lead are responsible production line employees.
Lead Factory Operating System (FOS) line meeting to set clear plan for their line team.
Lead workshops resulting in tangible key performance indicator improvements.
Line
Line specific coordination of personnel assigned to area of responsibility.
Maintain
Maintain 100% ad in stock throughout the Grocery and General Merchandise areas.
Maintain accurate records.
Maintain a clean and organized workstation and line.
Maintain a high level of product quality and traceability during product assembly.
Maintain and store cleaning supplies and equipment.
Maintain and sustain right first-time batch culture, by following BOM's and weighing out correctly.
Maintain and update Huddle / OpEx boards for line.
Maintain a safe and clean work environment by educating and directing personnel on proper GMP.
Maintain a safe work environment with 100% training and compliance to applicable procedures.
Maintain back room organization in Grocery and General Merchandise areas.
Maintain clean work environment keeping floor and isle was clear of all trash and obstacles.
Maintain clean work environment (Production Floor).
Maintain equipment in good condition.
Maintain established studio development standards and practices.
Maintain high sanitation levels throughout sales floor and backroom.
Maintain individual work area / equipment in a neat, orderly manner.
Maintain proper staffing levels on production shift.
Maintain store appearance, product presentation and company standards.
Maintain tools and keep equipment clean and in a proper state of repair.
Make
Make and communicate decisions that are appropriate for level of accountability.
Manage
Manage budget accountability for Headcount, Overtime, and direct expenses for a shift and / or line.
Manage challenging customer escalations and non-conformities.
Manage / leads front line employees as well as potentially exempt employees.
Manage production assembly lines.
Maximize
Maximize line efficiency with minimal direction.
Maximize time to achieve department goals and productivity.
Measure
Measure product before and after production.
Meet
Meet customer specifications with metal.
Meet daily goals of Quality, Productivity and Delivery.
Mentor
Mentor, coach, and counsel employees on performance and leadership behaviors.
Monitor
Monitor and maintain all safety equipment and tools.
Monitor break times of operators on line.
Monitor manufacturing processes, automation, and equipment to ensure quality operations.
Operate
Operate a barrel-lifter to replenish the lines.
Operate and monitor sewing equipment and replenish materials as needed.
Operate equipment to cover for operator absence.
Operate forklift, if forklift-operating requirements met.
Operate line equipment in accordance with Safety and Standard Work guidelines.
Oversee
Oversee that employees are working within safety guidelines and using required PPE at all times.
Own
Own deliverable for deviations / CAPA's / ICC's / RPC's.
Own incident RCA and supports countermeasure execution.
Pack
Pack finished goods into correct packages and boxes.
Participate in
Participate in equipment dismantling and set-up in the appropriate sequence.
Partner
Partner with the Maintenance Mechanic to troubleshoot mechanical problems and repairs.
Pay
Pay attention to product being packaged.
Perform
Perform all tasks involved in the production of products.
Perform automatic weight checks.
Perform code reviews with the team.
Perform daily T2 huddle as required.
Perform general cleaning in the plant as assigned.
Perform hourly checks on tables and tracks progress of workers.
Perform in-process checks and inspections within specified time frames.
Perform periodic checks on product yield / recovery during the run.
Perform root cause analysis and resolve problems.
Prepare
Prepare line set-ups for following shifts, including quality first offs.
Prioritize
Prioritize work and independently seek out relevant information.
Promotes
Promotes team concepts, collaboration, respect and leadership.
Provide
Provide feedback in a timely manner to colleagues in a spirit of continuous improvement.
Provide timely coaching, counselling and feedback.
Publish
Publish Service Line dashboard on a regular basis.
Pull
Pull samples for testing and performs testing as needed (i.e. tensile testing).
Reach
Reach with hands and arms.
Read
Read and comprehend instructions and follow established procedures.
Read ingredients and count how many bags are on a pallet.
Read, understand and complete quality paperwork at specific intervals.
Read / understand MAP as well as deviations if necessary.
Report
Report all unsafe work areas.
Report and market engagement activities and statistics.
Report on issues, malfunction or defective parts.
Report to line ~15 minutes early.
Resolve
Resolve personnel issues on-line.
Review
Review daily schedules to work load.
Review sales goals, supply costs, stock loss / shrink results and goals.
Review total labour charges for line.
Solicit
Solicit regional insights.
Stack
Stack bags / cans of product as it comes off the various production lines.
Supervise
Supervise store operations overnight.
Supervise, train, and develop subordinates.
Support
Support quality system expectations; and ensure adherence to cGMPs.
Support the training department on the training of new manufacturing personnel to the team.
Support trials and engineering per area plan and OEE target.
Take
Take that first one by applying to be a Line Lead.
Train
Train new hires to ensure efficiencies set for the day are met.
Train new production line workers on all lines.
Understand
Understand all operations support system including traceability and documentation systems.
Understand and adhere to Good Manufacturing Practices.
Understand equipments on his / her line and troubleshooting some mechanical problems.
Understand training needs and implement a training plan.
Update
Update production metrics on hourly production whiteboard.
Use
Use and knowledge of all hand tools as needed.
Use of all hand tools as needed and ability to utilize hand jack when necessary.
Valuate
Valuate and maintain cost drivers of the Service Line.
Verify
Verify packaging work orders.
Verify components on work order to ensure correct number of components are available for production.
Work with
Work as middleman between workers and management to create healthy communication.
Work closely with Global Analytics & Insights.
Work Independently as well as lead small production team.
Work toward achievement of KPIs.
Work well with multiple departments.
Work with cross-functional groups to identify, address and evaluate impact of distressed inventory.
Work with industrial manufacturing equipment on production line.
Work with shift foremen to have consistency on all shifts.
Most In-demand Hard Skills
The following list describes the most required technical skills of a Line Lead:
Manufacturing Environment
Business
Manufacturing
Health And Safety Regulations
Lead & Direct All Production Line Operators
Operate Various Machines
Products Manufactured
Use Various Machines And Practical Skills
Wax Types & Characteristics
Production
Quality Control
Continuous Sitting For Prolonged Periods
Deliver On Challenging Objectives
High Volume Manufacturing Environment
Manual Lifting Up To 50Lbs
Math Skills
Most In-demand Soft Skills
The following list describes the most required soft skills of a Line Lead:
Written and oral communication skills
Interpersonal skills
Leadership
Organizational capacity
Problem-solving attitude
Attention to detail
Deliver valuable teamwork
Follow and execute instructions
Time-management
Accountable
Coaching
Confident
Inspire others
Love a challenge
Motivated leader
Teamwork
Collaborative
Identify issues quickly and implement solutions
Identify root cause
Respect