Main Responsibilities and Required Skills for a Director of Manufacturing
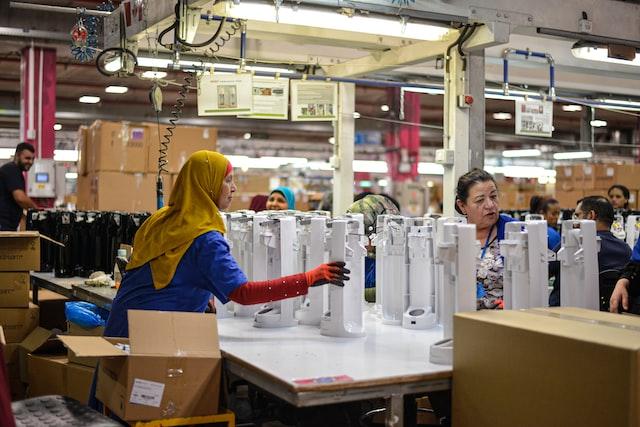
A Director of Manufacturing is a professional who holds a key leadership position in an organization's manufacturing operations. They are responsible for overseeing and managing all aspects of the manufacturing process, ensuring efficiency, quality, and productivity. In this blog post, we will delve into the primary responsibilities and the most in-demand hard and soft skills for Directors of Manufacturing.
Get market insights and compare skills for other jobs here.
Main Responsibilities of a Director of Manufacturing
The following list describes the typical responsibilities of a Director of Manufacturing:
Allocate
Allocate resources effectively to meet production targets and deadlines.
Analyze
Analyze production data and generate reports to inform decision-making.
Apply
Apply lean six sigma manufacturing methods to drive continuous improvements and process optimization.
Assess
Assess and improve partner and licensee readiness and capability.
Collaborate with
Collaborate with cross-functional teams to coordinate production schedules and ensure timely delivery of products.
Collaborate with our Sales team to help create exceptional offerings for our customers.
Communicate
Communicate any and all issues or company complaints to the Chief Executive Officer directly.
Conduct
Conduct performance evaluations and provide feedback to the manufacturing team.
Consult with
Consult with Human Resources Department as appropriate.
Contribute to
Contribute to the product development design process.
Control
Control and minimize labor overtime, premium freight and repair expenses.
Coordinate with
Coordinate with the night Director of Manufacturing.
Create
Create quality meetings and drive quality issues for improved higher yields.
Design
Design and deliver validated solutions for global manufacturing execution, shop-floor.
Develop
Develop and control profits, plans, budget, and process improvement initiatives.
Develop and implement strategic plans to achieve manufacturing objectives.
Develop and lead operational leaders as well as achieving plant and company objectives.
Develop and maintain strong relationships with suppliers and vendors.
Develop and manage quality assurance and acceptance processes.
Develop and manage the manufacturing and supply chain budget and operating plans.
Develop and manage the plant budget and operating plans.
Develop automation and machine improvements to result in savings and improved profit margins.
Develop risk assessment and mitigation strategies for the manufacture of key portfolio products.
Direct
Direct internal and external resources to successfully execute group goals.
Drive
Drive continuous improvement and process optimization through LEAN or Six Sigma.
Drive employee engagement.
Drive proactive operational improvement to identify and adapt best-in-class operational practices.
Drive the development and scaling of manufacturing lines.
Enable
Enable, support, drive and monitor key Operational Strategy initiatives as required.
Ensure
Ensure compliance with current federal, state and local regulations.
Ensure compliance with industry regulations and safety standards.
Ensure compliant and accurate use of the state cannabis track and trace system (METRC).
Ensure customer satisfaction throughout the entire manufacturing experience.
Ensure employees have everything they need.
Ensure plant performance is closely linked to customer requirements.
Ensure production targets / goals are met.
Ensure product is made to specification and passes CM and RISE acceptance testing.
Ensure the achievement of manufacturing and supply chain key metrics.
Ensure the timely manufacture of quality products meeting applicable regulatory requirements.
Ensure the timely manufacture of quality products, meeting applicable regulatory requirements.
Establish
Establish and enforce standard operating procedures to maintain consistency and quality.
Establish and monitor overall plant performance for production and quality standards.
Evaluate
Evaluate and improve manufacturing processes to drive continuous improvement.
Evaluate capacity / forecast for infrastructure planning.
Evaluate equipment for process technologies.
Foster
Foster a culture of continuous learning and development within the manufacturing team.
Identify
Identify and implement technology advancements to enhance manufacturing capabilities.
Implement
Implement lean manufacturing principles to eliminate waste and improve efficiency.
Implement quality control measures to ensure product integrity.
Implement technical solutions to complex problems.
Lead
Lead and grow our manufacturing infrastructure.
Lead and participate in cross-functional projects to drive process improvements.
Lead a team of innovative and motivated engineers to continue to scale our integrated.
Lead key vendor interactions and relationships.
Lead production planning and assembly efforts to ensure on-time and efficient end products.
Maintain
Maintain existing plant facilities and equipment.
Maintain product quality while increasing volume and lowering cost.
Maintain records and reporting systems for coordination of manufacturing operations.
Make
Make recommendations based off findings and drive implementation efforts.
Make recommendations based off findings and drive the implementation effort.
Manage
Manage and mentor manufacturing staff, providing guidance and support.
Manage capital asset maintenance.
Manage resources to meet organizational capacity requirements.
Manage the introduction of new products and formulations developed by R&D..
Meet
Meet plant operating plan objectives and comply with all regulatory requirements.
Mentor
Mentor and develop production and operation teams.
Monitor
Monitor all manufacturing in the building.
Monitor and control manufacturing costs to achieve budgetary goals.
Monitor production processes and optimize them for maximum efficiency.
Oversee
Oversee a 24x7 organization including on-site support, on-call rotations and issues escalations.
Oversee inventory management to maintain optimal stock levels.
Oversee lean implementation program identifying wastes and improving efficiencies.
Oversee the manufacturing process, ensure production meets or exceeds key performance indicators.
Oversee the timely development of CMC regulatory documents.
Participate in
Participate in creating and reviewing master and executed batch records.
Participate in ongoing and new tooling, materials, or equipment qualification.
Perform
Perform troubleshooting activities, as needed.
Plan
Plan future site initiatives.
Prepare
Prepare DFM, prepare formal DFM reports and communicate the design discrepancies.
Provide
Provide direction, development and leadership to plant's operating staff.
Provide leadership and training to accomplish the company goals and objectives.
Reduce
Reduce manufacturing unit cost and increase contribution to gross margins.
Replace
Replace or make adjustments to plant facilities and equipment when necessary.
Report
Report CMC group progress, challenges to executive management.
Resolve
Resolve production issues and address any operational challenges.
Run
Run a competitive and stringent process to select a contract manufacturing partner.
Spearhead
Spearhead new product introduction programs.
Stay updated with
Stay updated with industry trends and advancements to drive innovation.
Support
Support all Human Resource policies and practices fairly and consistently, including.
Support / manage tooling budgets and project implementation costs.
Support the achievement of plant-level KPI's in areas of safety, quality, delivery and inventory.
Troubleshoot
Troubleshoot process defects and drive toward problem resolution.
Understand
Understand the local, state, and federal rules and regulations regarding cannabis.
Update
Update job knowledge by participating in conferences and educational opportunities.
Work with
Work collaboratively as a member of the Senior Leadership Team.
Work to improve the productivity and quality of Mechanical Assembly builds.
Work with Engineering to mature RISE's DFM process.
Work with quality to prepare manufacturing presentations for customer audits.
Work with R&D during development to ensure product manufacturability, scalability, and excellence.
Most In-demand Hard Skills
The following list describes the most required technical skills of a Director of Manufacturing:
Lean manufacturing and Six Sigma methodologies.
Production planning and scheduling.
Supply chain management.
Quality management systems (e.g., ISO standards).
Manufacturing automation and robotics.
Inventory management and optimization.
Process optimization and efficiency improvement.
Cost control and budget management.
Data analysis and interpretation.
Enterprise resource planning (ERP) systems.
Manufacturing software and tools.
Project management.
Regulatory compliance.
Root cause analysis and problem-solving.
Capacity planning and utilization.
Continuous improvement methodologies (e.g., Kaizen).
Change management.
Environmental health and safety.
New product introduction (NPI) processes.
Supplier management and contract negotiation.
Most In-demand Soft Skills
The following list describes the most required soft skills of a Director of Manufacturing:
Strong leadership and decision-making abilities.
Excellent communication and interpersonal skills.
Strategic thinking and long-term vision.
Team management and motivation.
Conflict resolution and negotiation.
Collaboration and cross-functional teamwork.
Adaptability and flexibility.
Analytical and critical thinking.
Emotional intelligence and empathy.
Problem-solving and troubleshooting.
Conclusion
The role of a Director of Manufacturing is vital in driving the success of manufacturing operations. By fulfilling their primary responsibilities and possessing the right combination of hard and soft skills, Directors of Manufacturing can lead their teams to achieve operational excellence, optimize production processes, and ensure the delivery of high-quality products.