Main Responsibilities and Required Skills for a Development Quality Engineer
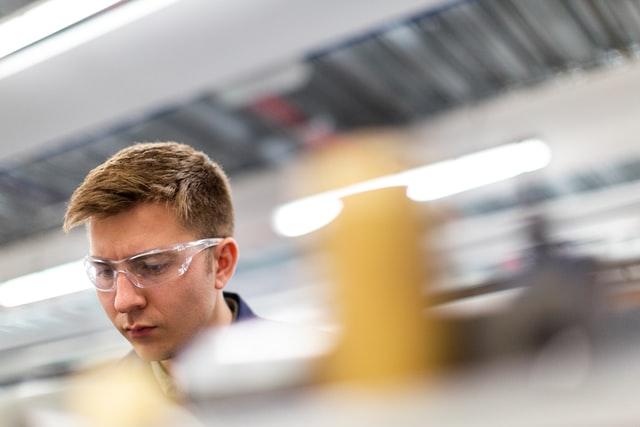
A Development Quality Engineer is a professional who plays a crucial role in ensuring the quality and reliability of software development processes and products. They are responsible for implementing and maintaining quality assurance measures throughout the development lifecycle. In this blog post, we will describe the primary responsibilities and the most in-demand hard and soft skills for Development Quality Engineers.
Get market insights and compare skills for other jobs here.
Main Responsibilities of a Development Quality Engineer
The following list describes the typical responsibilities of a Development Quality Engineer:
Advise
Advise and participate in root-cause analysis.
Analyze
Analyze and communicate product test results / conformance to specifications and standards.
Analyze incoming material defects.
Analyze product specifications and requirements.
Analyze quality audit findings and recommend modifications to products or standards.
Analyze quality standards for components, materials or services.
Assess
Assess potential new suppliers for technical, quality and manufacturing capabilities.
Assess supplier capabilities through direct visits, technical discussions, and directed testing.
Assist in
Assist in defining and measuring process capability, process controls, and process validation.
Assist in definition and completion of in vitro testing including applicable animal studies.
Assist in generating component specifications.
Assist in specifications and testing of sterilization methods.
Assist on-time completion of Design Control Deliverables.
Automate
Automate and streamline deployment processes.
Automate processes and software / systems testing.
Collaborate with
Collaborate with cross-functional teams to ensure quality standards are met.
Collaborate with customer support teams to address quality-related issues.
Collaborate with suppliers to develop comprehensive process validation strategies.
Communicate
Communicate issues to suppliers.
Complete
Complete Document Change Request Reviews in a timely and objective manner.
Conduct
Conduct internal quality audits and assessments.
Conduct phone calls with supplier as needed to expedite responses or answer questions.
Conduct risk assessments and mitigation strategies.
Conduct statistical analysis of test data and process anomalies.
Conduct supplier quality audits and evaluations.
Contribute to
Contribute and participate in supplier performance reviews.
Contribute to product design reviews, risk analyses, and document reviews.
Coordinate with
Coordinate with external certification bodies for product certifications.
Define
Define quality metrics and key performance indicators (KPIs).
Design
Design and conduct experiments for process optimization and / or improvement.
Design and conducts experiments for design and process optimization and / or improvement.
Design and execute test plans and test cases.
Design and perform acceptance testing on software systems.
Design change plan / reports.
Design input and output requirements / matrix.
Design input output trace matrix.
Design Review, Change & Transfer for Manufacturability.
Design specification reviews.
Design Verification and Validation activities.
Design verification and validation test planning.
Design verification and validation test protocols, execution and reports.
Design verification & validation.
Develop
Develop acceptance criteria for materials.
Develop and documents test plans, procedures, protocols and reports.
Develop and lead other team members.
Develop and maintain a monitoring system that overlooks our build landscape.
Develop and maintain quality documentation and records.
Develop and / or source inspection tools and equipment.
Develop corrective action plan where necessary.
Develop quality assurance plans and protocols.
Develop, test and maintain build system, CI / CD framework and deployment tools.
Diagnose
Diagnose issues and potentially fix issues on the CSDK code base.
Direct
Direct and controls the activities of quality engineers in support of core team objectives.
Document
Document and generate failure analysis reports in the Complaint Handling System.
Document and report quality assurance findings and recommendations.
Drive
Drive design quality, reliability, and compliance to standards and regulations.
Drive for accountability within self and project team.
Drive improvement and corrective action in the quality of components sourced from outside suppliers.
Drive process optimization initiatives to improve efficiency and quality.
Ensure
Ensure adherence to design control procedures and protocols.
Ensure and maintain a safe and professional work environment.
Ensure compliance with regulatory requirements and industry standards.
Ensure DHF content integrity, completeness, and regulatory / standards compliance.
Escalate
Escalate resource issues, constraints and delays to the quality director.
Establish
Establish priorities of individual or project assignments.
Evaluate
Evaluate and prioritize incoming reports.
Evaluate product design to identify potential design issues and drive technical decisions.
Execute
Execute and / or reviews tests according to various protocol requirements.
Execute and support on-time completion of Design Control Deliverable.
Execute and support on-time completion of Design Control Deliverables.
Execute on-time completion of design control deliverables.
Facilitate
Facilitate corrective and preventive action (CAPA) processes.
Generate
Generate and maintain incoming inspection procedures.
Generate essential requirements checklists & reports.
Identify
Identify supplier contacts and solicits required documents from suppliers.
Implement
Implement quality control processes throughout the product development lifecycle.
Implement quality management systems (QMS) and continuous improvement methodologies.
Implement statistical process control (SPC) techniques.
Initiate
Initiate or maintains schedule for projects and project milestones.
Interact with
Interact internally with peers to negotiate and resolve conflicts.
Investigate
Investigate customer complaints and implement corrective actions.
Investigate field failures related to supplier materials.
Investigate internal and external audit findings and write responses.
Investigate / troubleshoots.
Lead
Lead and / or support on-time completion of Design Control deliverables.
Lead efforts in automation, continuous deployment, build, and configuration management.
Lead identification of essential outputs and generate Essential Output reports.
Lead on-time completion of Design Control deliverables.
Lead or support Risk Management activities from product Concept through Commercialization.
Lead quality improvement projects and initiatives.
Lead Risk Management activities from product concept through commercialization.
Lead the investigation, permanent resolution and prevention of supplied component nonconformances.
Maintain
Maintain high standards for content completion, integrity, and regulatory & standards compliance.
Make
Make your mark in the fight against cancer.
Manage
Manage approval of supplier changes as a project leader.
Manage / conducts special analyses and / or staffing of projects as required by the business.
Manage development of supplied product inspection procedures and first article requirements.
Manage the development of supplied product inspection procedures and first article requirements.
Mentor
Mentor and develop other team members.
Monitor
Monitor and evaluate production processes for quality deviations.
Monitor and track quality metrics and trends.
Participate in
Participate in design reviews and product validation activities.
Participate in team activities providing quality and release engineering evaluation.
Perform
Perform both white-box and black-box testing and diagnosing on both the CSDK itself and client apps.
Perform Failure investigations of CRM product returns.
Perform re-assessment of suppliers each year per a defined schedule.
Perform re-evaluation of suppliers each year per a defined schedule.
Perform root cause analysis for quality issues and defects.
Perform Software Configuration Management tasks.
Plan
Plan and organize project assignments of substantial variety and complexity.
Plan development, and vendor qualifications.
Prepare
Prepare and submits required quality records and documents for closure and filing.
Provide
Provide assistance with audit support activities.
Provide CAPA guidance and assistance.
Provide supplier quality support for new product development teams.
Provide technical leadership to the business unit.
Provide technical support for the introduction of components from a new supplier.
Provide technical support in the selection of suppliers.
Provide training and guidance on quality standards and best practices.
Review
Review and approves all supplied product drawings and component quality plans.
Review and approves supplier qualification and validation plans.
Review and approve supplied material drawings and component quality plans.
Review current Quality Agreements and determines need to revise.
Review test protocols and test results provided by another functional group.
Select
Select methods and techniques to lead a project to completion.
Stay updated on
Stay updated on industry trends and advancements in quality assurance practices.
Support
Support and ensure internal & external audit responses and on-time product re-certifications.
Support and ensure objective component specification definitions, supplied.
Support and ensure on-time product re-certifications.
Support and ensures internal & external audit responses.
Support audits and quality system improvement activities.
Support CAPAs in the Corrective Action System.
Support design test and inspection method development, and execute method validation activities.
Support development, execution and analysis of biocompatibility and sterilization qualifications.
Support DHF content completion, integrity, and regulatory & standards compliance.
Support execution of bio-compatibility and sterilization qualifications.
Support internal and external audit responses and on-time product re-certifications.
Support internal & external audit responses.
Support manufacturing process development & qualification for new product and design changes.
Support new product introduction and validation activities.
Support product re-certifications.
Support R&D product builds for bench testing, animal lab, and clinical activities.
Support, reviews and approves Document Change Order and CAPA records.
Support Risk Management activities from product Concept through Commercialization.
Support test method development and lead test method validation activities.
Support the Continuous Integration build platform to deliver CSDK releases on time.
Support the development and review of biocompatibility and sterilization validations.
Support the establishment of objective, measurable, and verifiable product requirements.
Test
Test Method / Inspection Method Development and Validation.
Track
Track supplier responses and conduct follow-up and escalation as necessary.
Track supplier responses and conducts follow-up and escalation as necessary.
Train
Train inspectors to these procedures.
Understand
Understand and works to improve effectiveness of the BD matrix.
Utilize
Utilize testing tools and methodologies to validate product functionality.
Validate
Validate and verify software and hardware components.
Work with
Work closely with development / manufacturing / quality.
Work effectively with cross-functional team members, utilizing effective time management skills.
Work with design engineering in the completion of customer / system / product requirements.
Work with design engineering in the completion of product verification and validation.
Work with Manufacturing engineering to assess and address purchased product issues.
Most In-demand Hard Skills
The following list describes the most required technical skills of a Development Quality Engineer:
Proficiency in quality management principles and methodologies.
Knowledge of regulatory requirements and standards (e.g., ISO, FDA).
Experience with quality assurance tools and software (e.g., JIRA, HP Quality Center).
Understanding of statistical analysis techniques (e.g., Six Sigma, Lean).
Familiarity with risk management processes (e.g., FMEA, DFMEA).
Ability to interpret technical drawings and specifications.
Skill in using testing equipment and instruments.
Knowledge of validation and verification processes.
Competence in root cause analysis and problem-solving methodologies.
Experience with quality auditing and inspection techniques.
Proficiency in data analysis and interpretation.
Understanding of manufacturing processes and methodologies.
Knowledge of software testing principles and methodologies.
Familiarity with quality documentation and record-keeping practices.
Ability to perform reliability testing and analysis.
Skill in using quality management software systems (e.g., SAP QM).
Understanding of product lifecycle management (PLM) principles.
Experience with conducting supplier quality assessments.
Proficiency in using Microsoft Office Suite for documentation and reporting.
Knowledge of electronic quality management systems (eQMS).
Most In-demand Soft Skills
The following list describes the most required soft skills of a Development Quality Engineer:
Strong communication and interpersonal skills.
Attention to detail and accuracy in work.
Critical thinking and analytical abilities.
Problem-solving skills to address quality issues effectively.
Teamwork and collaboration with cross-functional teams.
Adaptability to changing project requirements and priorities.
Time management and organizational skills.
Leadership and project management abilities.
Customer focus and commitment to quality excellence.
Continuous learning mindset to stay updated on quality trends and practices.
Conclusion
Development Quality Engineers holds a crucial role in ensuring the quality and reliability of software development processes and products. They are responsible for a wide range of tasks, from analyzing requirements to conducting thorough testing, and implementing quality assurance measures. In addition to technical skills like programming, test automation, and performance testing, soft skills such as problem-solving, communication, and adaptability are equally important for success in this role.