Main Responsibilities and Required Skills for a Calibration Technician
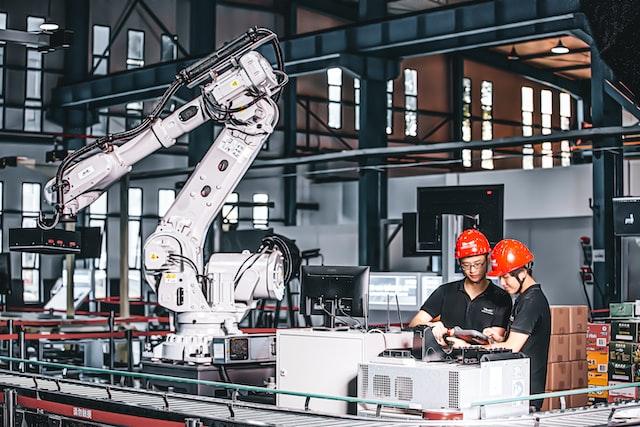
A Calibration Technician is a professional who ensures that measurement instruments and equipment are accurate and reliable. They play a crucial role in various industries where precise measurements are essential, such as manufacturing, engineering, and scientific research. In this blog post, we will describe the primary responsibilities and the most in-demand hard and soft skills for Calibration Technicians.
Get market insights and compare skills for other jobs here.
Main Responsibilities of a Calibration Technician
The following list describes the typical responsibilities of a Calibration Technician:
Adapt
Adapt existing work methods to different situations.
Adhere to
Adhere to all policies and procedures as applicable for functional area.
Adhere to ethical standards and confidentiality requirements.
Adjust
Adjust / repairs instruments to meet instrument manufacturer and calibration standards.
Analyze
Analyze calibration data to identify trends and patterns.
Anticipate
Anticipate and solve complex production / operational problems.
Assist in
Assist in the selection and procurement of new calibration equipment.
Assist with identification, purchase, and organization of calibration standards.
Attend
Attend all mandatory training and maintain training forms and files.
Build
Build customer relationships by offering assistance beyond your daily task list.
Calibrate
Calibrate and adjust measurement instruments to ensure accuracy.
Calibrate electrical instruments in the laboratory and at customer sites as part of a team.
Calibrate new components according to written protocols.
Calibrate and repair Law Enforcement and Sports related speed measuring devices.
Carry out
Carry out calibrations in a safe and timely manner.
Carry out duties in compliance with established business policies.
Champion
Champion Safety through all customer and operations activity.
Collaborate with
Collaborate with engineers and technicians to resolve calibration-related issues.
Collaborate with external vendors for calibration services.
Collect
Collect, record, and summarize, data during calibration.
Communicate
Communicate calibration results and recommendations to stakeholders.
Communicate effectively to Operations, and scheduling personnel.
Communicate with Leadership concerning any problems with product testing equipment.
Communicate with operations when equipment is needed for repairs and calibration.
Complete
Complete a report for the calibration of each unit.
Complete assigned projects.
Complete basic calibration procedures with minimal supervision.
Complete calibration assessments for instrument related changes.
Complete maintenance request work orders for regulated and un-regulated systems.
Complete regulatory and compliance verifications on sites.
Conduct
Conduct audits to ensure adherence to calibration standards.
Conduct preventative maintenance on calibration equipment.
Contribute to
Contribute to the improvement of the quality assurance system.
Coordinate
Coordinate and perform in-house equipment calibration verifications according to written procedures.
Coordinate shipping, receiving and work order completion for equipment calibrated offsite by vendors.
Coordinate with customers / end users to schedule calibrations.
Coordinate with departments across the facility to schedule calibrations.
Coordinate with equipment users to schedule calibrations.
Create
Create and implement calibration and repair procedures.
Create calibration certificates and data reports.
Create calibration certificates and data reports using Fluke metrology software.
Create, update and maintain calibration documentation.
Deliver
Deliver results by analyzing situations to determine the best solution for issues at hand.
Design
Design calibration fixtures.
Develop
Develop and maintain calibration procedures and guidelines.
Develop skills necessary to perform calibrations independently.
Disassemble
Disassemble, clean, repair, and replace defective parts of test equipment.
Document
Document and report any deviations or non-conformities.
Document calibration tasks.
Document work using good documentation practices and enter data into SAP database.
Ensure
Ensure all activities are executed following quality and regulatory standards.
Ensure all calibration results are properly recorded in the Computerized Asset Management System.
Ensure all calibrations are performed within organization's target time frame.
Ensure all health and safety policies and procedures are followed.
Ensure compliance with quality and regulatory standards.
Ensure customer satisfaction.
Ensure efficient coordination of projects and tasks as assigned by C&M Supervisor.
Ensure schedule adherence to meet cGxP compliance.
Ensure that all calibrations are performed on time according to schedules.
Ensure that Standards utilized for calibrations are accurately maintained.
Ensure the safety and proper handling of calibration equipment.
Enter
Enter said reports onto company provided laptop.
Escalate
Escalate issues that could present a cGxP noncompliance or an unsafe work environment.
Escort
Escort contractors through facility for routine deliveries or inspections.
Establish
Establish priorities of work assignments.
Follow
Follow calibration procedures and specifications.
Follow safety rules and keeps area and equipment in a clean and orderly condition.
Follow set up and calibration procedures, interpret technical schematics.
Foster
Foster Collaboration and Teamwork.
Generate
Generate and review out-of-tolerance reports.
Generate equipment specification documents for calibration standards.
Identify
Identify and implement improvements in calibration processes.
Identify opportunities for program and process improvement.
Implement
Implement NPI (New product introduction) to extend our instrument calibration range.
Include
Include any external interactions as appropriate.
Initiate
Initiate and provide guidance with out of tolerance reports.
Inspect
Inspect, calibrate and certify dispenser / pump meters at retail and commercial locations.
Interpret
Interpret P&ID's, equipment layouts, writing diagrams, user manuals and specifications.
Lead
Lead others in seeking out ideas and information to improve customer service.
Lead with Integrity and Respect.
Learn
Learn and comply with regulatory requirements such as APHIS, VMD & OSHA.
Maintain
Maintain accurate written and calibration records.
Maintain a clean and organized calibration laboratory.
Maintain a clean and safe worksite.
Maintain all documentation in an organised and controlled manner in compliance with regulations.
Maintain a strong focus on customer satisfaction and service quality.
Maintain calibration records and documentation.
Maintain calibrations scheduling database.
Maintain calibration standards.
Maintain company documentation and assets by electronic and written manual reports.
Manage
Manage and organize calibration inventory.
Manage projects independently.
Manage the workflow for IC2 products in conjunction with the production schedule.
Mentor
Mentor less senior employees in work group and offer counsel.
Monitor
Monitor and control environmental conditions for calibration processes.
Monitor the Fleet Complete System, and ensure all equipment is operational.
Oversee
Oversee and coordinate vendor work for on-site calibrations where external vendors are utilized.
Participate in
Participate in continuous improvement initiatives.
Participate in on-call rotation for equipment and facility after hours response.
Participate in proficiency testing and inter-laboratory comparisons.
Perform
Perform additional duties and responsibilities as assigned by the Calibration Supervisor.
Perform all necessary tests efficiently and accurately by following established written procedures.
Perform analysis for repair prevention.
Perform automatic software-controlled and manual instrument calibrations.
Perform calibration adjustments and repairs as necessary.
Perform calibrations, diagnostics, and maintenance of inspection, measuring and test equipment.
Perform Calibration test of the Temperature Services equipment.
Perform data analysis and report on equipment measurement studies.
Perform inspections and tests on equipment to identify potential issues.
Perform maintenance, troubleshooting and repair of precision equipment.
Perform minor meter repairs for gas, diesel, lube oil, and DEF meters.
Perform minor repairs on retail petroleum equipment.
Perform multi-discipline calibrations and simple measurement systems.
Perform multi-discipline calibrations on measurement systems.
Perform normal repairs and maintenance.
Perform other duties consistent with skills and training as assigned by C&M Supervisor.
Perform pre work inspections.
Perform relatively complex assignments and solves problems that may have a variety of solutions.
Perform RF characterization measurements such as.
Perform work in a manner to ensure safety of co-workers, equipment and self.
Perform work throughout site.
Prepare
Prepare accurate and legible calibration reports including test data.
Process
Process ownership for IC2 calibration and quality output result.
Promote
Promote a quality mindset and quality excellence approach to all activities.
Promote a safety culture.
Promote Safety within the Team.
Promote teamwork, cooperation and commitment to "Total Customer Satisfaction” among team members.
Promote the sale of the company's service products and company's liquid handling.
Provide
Provide and enhance technical skills training in-line with current innovation.
Provide a superior level of customer support to bridge strong customer relations.
Provide excellent communication and service to customers, both internal and external.
Provide formal training to equipment users and other calibration technicians.
Provide on-site technical consulting with customers and help them to minimized downtime.
Provide responsive customer support with emphasis on customer satisfaction.
Provide technical expertise to various departments (Productions, QA, Sales).
Provide technical support and guidance to colleagues.
Provide training and guidance regarding the calibration program with other departments as needed.
Recommend
Recommend facility improvements to meet OSHA safety, ISPE or FDA guidelines.
Refer
Refer to our website for more detailed comprehensive product / Service coverage.
Repair
Repair or replace broken or malfunctioning components of petroleum pumps and metering.
Report
Report work carried out in compliance with site-based reporting tools.
Research
Research and answer user technical measurement questions.
Research calibration standards.
Research simple repair situations and determine action steps.
Resolve
Resolve unusual, nonstandard problems.
Review
Review work of lower-level employees for quality and content.
Schedule
Schedule self-performed work assigned at beginning of month and due by end of month.
Schedule sending out calibration standard for re-calibration.
Serve as
Serve as a mentor when assisting less experienced staff in solving more complex problems.
Stay updated with
Stay updated with the latest calibration techniques and technologies.
Test
Test instruments to ensure conformance to factory specifications.
Track
Track and manage calibration schedules.
Train
Train and mentor junior calibration technicians.
Travel
Travel may be required to other manufacturing sites to provide support.
Travel
Travel to customer locations to perform calibration services, UPT's and sweeps.
Troubleshoot
Troubleshoot and diagnose problems with calibration equipment.
Troubleshoot and repair instruments.
Troubleshoot and repair or replace out of tolerance devices.
Troubleshoot and solve challenges.
Troubleshoot equipment and perform necessary repairs.
Troubleshoot equipment and system malfunctions or arrange for repair as appropriate.
Use
Use a laptop with proficiency.
Use and maintain all applicable Safety and PPE as required by Crystal Glass.
Use and order tools and specify and order parts with attention to safety precautions.
Use approved fall prevention devices when performing elevated tasks as required.
Use automated electronic calibration processes.
Use computer software specific to calibration.
Use hand tools, power tools and delicate testing equipment in performance of duties.
Work with
Work schedule will be determined by work load and equipment availability.
Work with other laboratory technicians to learn calibration fundamentals.
Write
Write calibration procedures, prepares documentation, inputs data, and generates reports.
Most In-demand Hard Skills
The following list describes the most required technical skills of a Calibration Technician:
Proficiency in calibration techniques and methodologies.
Knowledge of measurement principles and standards.
Familiarity with metrology and calibration equipment.
Ability to read and interpret technical drawings and specifications.
Experience with calibration software and data management systems.
Understanding of statistical analysis and uncertainty calculations.
Knowledge of electrical, mechanical, and dimensional calibration.
Competence in using precision measuring instruments.
Proficiency in troubleshooting and diagnosing calibration issues.
Familiarity with regulatory requirements and quality standards.
Ability to perform mathematical calculations accurately.
Proficiency in using calibration standards and reference materials.
Knowledge of industry-specific calibration requirements.
Understanding of calibration traceability and accreditation.
Experience with calibration procedures and documentation.
Competence in using calibration software and hardware tools.
Familiarity with electronic and computerized calibration systems.
Ability to perform equipment performance tests and validations.
Knowledge of safety protocols and procedures.
Proficiency in using laboratory and calibration equipment.
Most In-demand Soft Skills
The following list describes the most required soft skills of a Calibration Technician:
Strong attention to detail and accuracy.
Excellent problem-solving and analytical abilities.
Effective communication and interpersonal skills.
Ability to work independently and in a team.
Strong organizational and time management skills.
Adaptability and flexibility to changing priorities.
Commitment to quality and precision.
Professionalism and integrity in work ethics.
Continuous learning and self-improvement mindset.
Customer-focused approach and service orientation.
Conclusion
Calibration Technicians are responsible for ensuring the accuracy and reliability of measurement instruments and equipment. They possess a combination of technical skills related to calibration techniques and equipment, as well as soft skills that enable them to effectively communicate