Main Responsibilities and Required Skills for Quality Engineer
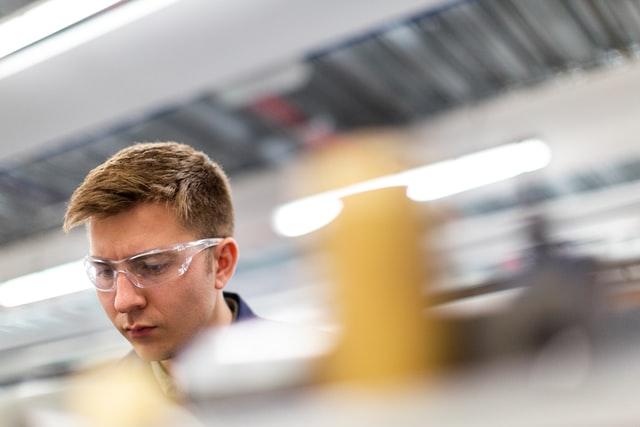
A Quality Engineer is responsible for managing the quality of a product. They ensure that the product meets industry standards through testing and inspections. In this blog post we describe the primary responsibilities and the most in-demand hard and soft skills for Quality Engineers.
Get market insights and compare skills for other jobs here.
Main Responsibilities of Quality Engineer
The following list describes the typical responsibilities of a Quality Engineer:
Address
Address systemic quality issues with suppliers or internal groups.
Administer
Administer the ECR and deviation process.
Align
Align with Supplier Quality Engineering on boundary samples.
Analyse
Analyse Quality data to understand challenges and areas of focus.
Analyze feature requirements and create test cases to validate new feature.
Analyze and report on process performance with emphasis on 'critical to' and 'cost of' quality.
Analyze causes of defects and recommend or leads teams who recommend corrective actions.
Apply
Apply knowledge of Design Control principles and quality.
Apply statistical methodology to analyze test data.
Approve
Approve checking fixture designs and final build approval.
Assess
Assess other quality documentation protocols and reports as required.
Assist in / Assist with
Assist Development team with process improvements to improve product quality.
Assist in the design and execution of validation protocols when required.
Assist in the evaluation and audit of Government Furnished Property across the business.
Assist in training operations.
Assist operations quality engineers as required.
Assist Quality Manager in establishing, implementing and maintaining the quality management system.
Assist supplier quality specialist with any supplier audits, or PPAP requirements.
Assist the development team in debugging code and implementing solutions for fixing them.
Assist with promoting and implementing company-wide quality improvement efforts.
Assist with staging, sandbox, and production releases.
Assist with supplier quality performance monitoring, reporting, and corrective actions.
Assist with the department metrics and works with others to ensure department goals are achieved.
Assist with the development / update of FMEA and Hazard Analysis.
Assist with third party and FDA quality audits as needed.
Assist with various projects as assigned by direct supervisor.
Assure
Assure data availability and integrity for all quality related data.
Audit
Audit existing and potential suppliers to determine capability of manufacturing and ensure.
Audit Site JLL documentation on Key controls, access card and issuing procedures.
Audit suppliers to IATF16949 requirements and identifies opportunities for improvements.
Automate
Automate tests using homegrown and / or open source test frameworks.
Build
Build and maintain regression test suites and frameworks.
Build Automation Frameworks.
Build meaningful and productive relationships with internal business partners.
Build object repository , Create new Page Objects To create and Maintain Automation scripts.
Build stable relationships internally across Design Assurance team and within project core teams.
Coach
Coach, and mentor non-exempt personnel.
Collaborate
Collaborate with suppliers to develop comprehensive process validation strategies.
Collaborate with BA's, SA's, Developers, PM's, TPO's and Business stakeholders.
Collaborate with customer to help determine root cause of customer issues.
Collect
Collect and analyze data, and generate technical reports and presentations.
Communicate
Communicate clearly with internal and external clients, both verbal and written.
Communicate efficiently and effectively in a professional manner.
Communicate fully with superiors, teammates, and others who have a need to know.
Communicate status and progress.
Communicate with customers as required.
Compile
Compile and present final determination to management.
Compile and write training material and conduct training sessions on quality control activities.
Compile quality data sends to customer prior to shipment.
Complaint
Complaint Evaluation - Investigates complex complaints with management oversight.
Complaint Rate (Cost of Non-Quality, Recalls, Complaints, DEFOA).
Complete
Complete site inspections.
Conduct
Conduct design verification test to meet product requirements and specifications.
Conduct internal quality audits and ensure corrective actions are timely and sufficient.
Conduct, lead & support CAPA projects and ensure effective solutions.
Conduct new factory assessment in quality areas.
Conduct regular Quality Review Meetings with key suppliers and report on same.
Conduct risk assessments following established risk procedures for identifying areas for improvement.
Conduct statistical data analysis for new flavor formulations.
Conduct Supplier reviews / audits to ensure the supplier processes meet our requirements.
Consider
Consider financial impacts of quality process controls and inspections.
Contact
Contact Window to handle customer and market quality issue compliant and feedback.
Contribute
Contribute as a Department Contributor for Advanced Quality Planning (AQP).
Contribute to and maintain full and robust automation of CI / CD pipeline.
Contribute to software design & code reviews.
Contribute to test automation infrastructure by writing and augmenting test libraries and services.
Control
Control, Manufacturing Technical Support, Facilities Engineering, or Automation.
Coordinate
Coordinate all Quality requirements as they relate to the program.
Coordinate and assigns programming tasks to other programmers as needed.
Coordinate Design Control, Design.
Coordinate the introduction to the plant of new products, processes and packages.
Create
Create and issue internal Corrective Action or Supplier Corrective Action Requests.
Create and maintain automated tests.
Create and maintain quality department documentation as necessary.
Create and manages field corrective action project schedules.
Create and optimizes test automation frameworks and use of test automation tools.
Create dashboards and metrics to monitor data quality.
Create detailed test scripts.
Create, edits, and maintain requisite documentation.
Create high quality automated functional tests.
Create, improve, and automate test plans.
Create Performance Test Plans for MasterCard products.
Create, revise and optimize quality documentation to improve training efficacy throughout operations.
Create test specifications and test environments as per plan.
Decompose
Decompose requirements into exhaustive test cases and create tests within TestRail.
Defect
Defect and trend tracking, reporting, and analysis.
Define
Define overall test strategy for assigned features.
Define team's deliverables, content and quality metrics.
Define the characteristics to be measured using SPC, and control limits.
Design
Design and Execute Manual Test cases.
Design Control, Design Verification and Process Validation.
Design Control & Product Development.
Design detailed and comprehensive test plans and test cases.
Design Input / Output Characterization & Specification.
Design Review, Change & Transfer for Manufacturability.
Design and implements product and process documentation, including inspection plans.
Design Software (AutoCAD, Solid Works).
Determine
Determine and executes appropriate material disposition strategies to support commercial demands.
Develop
Develop a continuous improvement plan with supplier and track / reporting progress.
Develop and delivers quality-related training.
Develop and execute automated API / UI / Unit tests to enable continuous delivery.
Develop and execute automated test cases.
Develop and gain approval of rework plans.
Develop and implements plant Quality Engineering Programs for designated product lines.
Develop and implement statistical incoming and in-process sampling / control plans.
Develop and leads execution of process validations and tests.
Develop and lead training for QA systems.
Develop and maintain a proven spirit of partnership.
Develop and maintain company inspection plans.
Develop and maintain inspection procedures for Receiving Inspection.
Develop and / or revision of PPAP documentation.
Develop and review process control plans to identify areas for process improvement.
Develop and Validate test methods for evaluation of product requirements.
Develop an understanding of our reporting products from the user perspective.
Develop audit plans and associated supplier communications.
Develop / create inspection plans for site equipment and setting up maintenance plans in SAP.
Develop, Document and maintain a supplier rating system and report on same.
Develop, execute, and analyze quality reporting measures.
Develop, implement and participate in training to build quality awareness.
Develop long-term Supplier relationships, generate and implement cost reduction ideas.
Develop new and unique ideas.
Develop or ensures the development of accurate and thorough forecasts.
Develop procedures for inspecting and testing of finished products.
Develop processes and packaging to maintain quality integrity during the APQP process.
Develop / promote excellent team attributes for both Qualitest / client employees.
Develop Quality Communications to promote Quality Mindset (Voice of Quality).
Develop quality control standards for Production and for suppliers.
Develop scripted manual tests.
Develop, track and report performance metrics and key quality indicators.
Direct
Direct reviews of requirements, tools and technologies for improving quality and reducing costs.
Direct and control the activities of quality engineers in support of core team objectives.
Distribute
Distribute, assign and ensure completion of workstream responsibilities.
Document
Document effective coverage of requirements by verification techniques.
Document resolution, findings and actions via memos, reports.
Document and executes simple software components of larger architectures.
Document and work to resolve complex problems.
Drive
Drive automation innovation and streamline overall testing processes.
Drive for accountability within self and project team.
Drive innovative improvements to team processes.
Drive optimization and continuous improvement of the Quality Management System.
Drive quality and process improvement at assigned suppliers.
Drive (RCCA) Root Cause.
Drive the initiative to achieve ISO 9001 quality standards.
Educate
Educate and train quality assurance inspectors and other staff.
Embrace
Embrace change and innovation and initiate new and improved ways of working.
Engage in
Engage in applying / leading Quality tools in Product Delivery Process (PDP) teams.
Enhance
Enhance the test framework as appropriate to ensure coverage of new product functionality.
Enhance / Update / Debug test related code, libraries efficiently.
Ensure
Ensure all quality records are maintained whether that's on paper or electronically.
Ensure compliance to quality procedures / processes.
Ensure compliance with company standards and government regulatory requirements.
Ensure compliant documentation in cross-functional areas of support.
Ensure content and structure of all Testing documents / artifacts is documented and maintained.
Ensure data are available according to company QO guidelines.
Ensure data is relevant to executive leadership reports as well as localized program reporting.
Ensure initiatives are successfully implemented.
Ensure PAP execution for new products and modified products for both suppliers and BTRE inside.
Ensure products meet the organization's and customers' quality and product integrity requirements.
Ensure suppliers' compliance with Sourcing and KONE policies, processes and procedures.
Ensure that all the deliverables are met.
Ensure that quality reporting (e.g. incoming and in-process quality trends.
Ensure that vendors' PFMEAs are compliant with ISO 13485 and FDA cGMP requirements.
Ensure that workflows, processes, and products comply with safety regulations.
Ensure the confidentiality and integrity of the information being accessed.
Ensure the project complies to internal and regulatory requirements.
Ensure the readiness of internal and / or external audits including the support as Audit Prescriber.
Escalate
Escalate to superior if no progress or delay on the closure and to avoid potential client escalation.
Establish
Establish an effective Management Review process, including routine reporting.
Establish processes, artefacts and policies for ensuring high standards of quality.
Estimate
Estimate, prioritize, plan automation testing efforts related project work.
Evaluate
Evaluate incoming materials, and supplier processed materials into production.
Evaluate raw materials, components and other inputs to the production process.
Evaluate supplier data to initiate process improvement opportunities along the supply chain.
Execute
Execute manual test cases, document actual results, and evaluate compared to expected results.
Execute the appropriate test scripts and update the results within the Test Management Tool.
Facilitate
Facilitate resolution and communication across functional groups on issues and decisions.
Facilitate Analytics / Metrics Programs and provides consultation on leading indicators.
Find
Find, document, and track defects through complete Jira workflow.
Focus
Focus on jobs-to-be-done and defining the KPI's that define success for customers and the business.
Follow
Follow all safety policies, precautions, and procedures.
Follow agreed approach & advises of any deviation from direction agreed.
Follow scrum principals and values.
Follow standard methodologies for testing, profiling and releasing high quality software.
Formulate
Formulate and / or assist in creating quality control policies and procedures.
Formulate procedures, specifications, and standards for the company products and processes.
Gather
Gather all testing results and ensure that the expected results resolve the issues.
Generate
Generate, manage and drive to closure SCARs opened for CMs.
Generate positive energy – motivate others to build a positive team spirit.
Generate test data and maintain test environments throughout the development lifecycle.
Generate validation protocols using templates.
Guarantee
Guarantee product compliance with company and customer standards.
Guide
Guide – related to the new QMS including examples and clarifications b.
Guide the conceptualization of new methodologies, materials, machines, processes or products.
Help
Help developers write good and repeatable unit tests.
Help identify root cause of issues found, assist development teams with troubleshooting issues.
Help Integrate POS with payment hardware and configuration.
Help drive and promote understanding of the need for change through the organization.
Hire
Hire and mentor new engineers, maintaining a culture of innovation, teamwork and self-improvement.
Host
Host external audits (ISO, regulatory, etc).
Host & support Customer, Internal and Third Party Audits as required.
Identify
Identify and document automation requirements.
Identify and record any problems relating to the product, process or system.
Identify areas of improvement or concern and works with the engineering team to address them.
Identify, initiate, lead and monitor continuous quality and business improvement projects.
Identify opportunities to apply SPC analysis.
Implement
Implement and approve Supplier Quality Audits.
Implement checks and balances independently to minimize impact of mistakes.
Implement and maintain effectiveness of ADD s Quality System.
Improve
Improve baseline performance relative to cost, quality, cycle time and customer satisfaction.
Incorporate
Incorporate Division Quality Assurance standards into working manufacturing procedures.
Initiate
Initiate implementation of Supplier proposed changes through HPNE's Change Control Process.
Initiate and follo up on manufacturing-related CAPA and QNC for BCC Wet Wipes platform.
Initiate the Corrective Action Reports (CAR) for official, unofficial and internal investigations.
Interface with
Interface and provide technical support on quality issues with the customer as needed.
Interface with all departments as applied to the Policies and Procedures.
Interface with customers to understand real-life usage, build test cases.
Interface with internal and external customers.
Investigate
Investigate (and correct) customer issues and complaints relating to quality.
Lead
Lead all automation efforts for Functional Scrum Teams (e.g. API, Web, Native).
Lead and mentor software system owners in the execution of SDLC project deliverables.
Lead Interior and Exterior Harmony Review with cross functional team for the appearance approval.
Lead in the completion and maintenance of risk analysis.
Lead investigations to resolve and troubleshoot supplier processing or packaging issues.
Lead PPAP and start up training sessions for suppliers.
Lead projects supported by cross functional teams related to Quality.
Lead Risk Management activities from product Concept through Commercialization.
Lead root-cause analyses and implementation of corrective actions as appropriate.
Lead CFT to determine root cause and solve problems.
Lead in the evaluation and approval of supplier requested changes or improvements.
Lead process control and monitoring of CTQ parameters and specifications.
Lead Risk Management activities.
Lead with Integrity and Respect.
Lead the effort to add multiple points of presence globally.
Lead the team through execution of the DevOps / QE roadmap for Core Banking System Portfolio.
Leverage
Leverage knowledge of engineering through American Society for Quality.
Maintain
Maintain 100% compliance to Kestra Medical processes and procedures.
Maintain a culture of Quality as it pertains to Accuray products and services.
Maintain and improve Quality System in accordance with FDA Regulations and ISO 13485 requirements.
Maintain and monitor Customer Manuals, Engineering specifications and Industry standards.
Maintain a satisfactory record of completion of PLS requirements.
Maintain a sense of purpose, value and ownership of current skill level compared to current job.
Maintain a working knowledge of government and industry quality codes and standards.
Maintain good communication with leadership, team members and customers.
Maintain quality surveillance of suppliers.
Maintain quality system program requirements, e.g., record retention and destruction, legal hold.
Maintain Supplier Quality Program to ensure compliance on all levels.
Manage
Manage a cross-functional team which may consist of senior level individual contributors.
Manage all internal and external quality issues from both customers and suppliers.
Manage and maintain compliance to CFR 21 Part 11 requirements for electronic records.
Manage department to budget.
Manage inspection and controls to ensure supplier provided material quality levels.
Manage multiple priorities and tasks in a dynamic work environment.
Manage nonconformance and failure investigations and conduct periodic trend analysis.
Manage PDCA log, QPR log, Cash Issues and CS databases for assigned customer non-conformance issues.
Manage and maintain quality inspection and product release programs.
Manage assigned DMRs to ensure forms are complete prior to closure.
Manage CAPA and other related QMS processes.
Manage feasibility studies of the design to determine if capable of functioning as intended.
Manage Supplier / CM through continuous improvement activities.
Manage supplier qualification and documentation process.
Measure
Measure (CMM Machine) and improve machine and process capability.
Mentor
Mentor or provide inputs for supplier process validation.
Monitor
Monitor relevance performance.
Monitor, respond, initiate corrective actions, follow up, close and track customer complaints.
Monitor the implementation of unit safety policy, processes, procedures and guidelines.
Motivate
Motivate the development process for efficiency and performance.
Navigate various complex FDA Quality System.
Negotiate
Negotiate pricing and contractual terms to close upsells as required.e.
Observe
Observe Product testing and map it to Risk Index.
Oversee
Oversee quality performance of assigned work cells.
Own
Own on-call schedules, alerting, monitoring and build / deploy system used by the entire team.
Own Quality goals and metrics and drive continuous improvements of products and processes.
Own your personal development and support the development of others.
Participate in
Participate and provides input in design reviews.
Participate / conduct self-inspection / audit walkthroughs.
Participate in and / or lead formal risk assessments.
Participate in bug scrubs and prioritization sessions.
Participate in department regulatory related CAPAs and audit responses.
Participate in new business reviews, customer programs and supplier development.
Participate in operations meetings.
Participate in plant wide Continuous Improvement activities.
Participate in the CAPA process as an as action owner and quality reviewer.
Participate in the development of requirements, software design, and software test design.
Participate in the maintenance, improvement and deployment of the Quality Management System.
Participate in supplier Quality System Improvement Plans.
Perform
Perform and document regression testing and focused system testing on all custom implementations.
Perform assessment on the design / architecture on suitability for the quality criteria.
Perform customer required PPAP's.
Perform documentation activities in eDMS and work with departments on documentation needs.
Perform effective Root Cause Analysis, 5S, 5Y, 8D, etc..
Perform failure mode analysis on new or existing products.
Perform internal departmental audits to ensure adherence to the quality management system.
Perform other duties as assigned based on business needs.
Perform other related duties and responsibilities as assigned.
Perform periodic / scheduled GEMBA walks to maintain adherence to 5S / 6S..
Perform pre and post review and approval of all SDLC project deliverables.
Perform Preliminary review (if qualified) of Quality Notifications as required.
Perform product failure investigations and other CAPA related activities.
Perform product inspections, document results and findings.
Perform qualifications assigned.
Perform quality analysis and testing.
Perform Quality validation / verification of new material and / or machines.
Perform Root Cause Corrective Action investigations.
Perform statistical analysis such as capability, gage R&R, and statistical process control.
Perform supervisor activities to Quality Technicians or Quality Engineers, if required.
Perform supplier audits for risk and capabilities.
Perform supplier visitations / audits as deemed necessary.
Perform tolerance analysis on mechanical and electrical assemblies.
Perform training regarding new technologies, policies and procedures.
Perform verification activities in the power area.
Prepare
Prepare and communicate recommendations and respective action plans.
Prepare and perform training for new and current team members, as required.
Prepare audit checklists and reports as well as present corrective action reports.
Prepare and submit required quality records for closure and filing.
Prepare product and process reports by collecting, analyzing, and summarizing data and trends.
Prioritize
Prioritize and manage part and product quality issues.
Prioritize, develop, and maintain project schedules.
Process
Process Control & Yield / Trend Monitoring.
Process Qualification & Validation.
Produce
Produce "client' and "internal' status reports.
Produce technical reports to support product changes or quality assurance investigations.
Propose
Propose enhancements in the existing features & functionalities.
Propose opportunities to further improve the NPI process.
Provide
Provide consultation and direction to the plant in relation to all validation and CAPA matters.
Provide Design Control lifecycle, procedure and policy training as necessary.
Provide direction to environment artists for aesthetic and technical considerations.
Provide direct support to Quality personnel regarding operation of Quality Assurance function.
Provide expertise and support to the business unit on matters affecting safety.
Provide guidance on statistical process control implementation.
Provide guidance on the principles of applicable standards as.
Provide ideas for improvement in areas such as quality, productivity, and safety.
Provide input and support to human factors engineering documentation.
Provide input for team decisions.
Provide inspection support to machine operators.
Provide leadership for sterilization validation and biocompatibility testing.
Provide liaison to various regulatory bodies.
Provide Process / Quality Engineering support to product development teams, helping.
Provide Quality Engineering.
Provide quality support to Integrated Warehousing and Distribution functions.
Provide recommendations for procedure updates to support EU MDR compliance.
Provide risk analysis leadership for all departments.
Provide strong testing, debugging and documentation skills.
Provide technical and statistical expertise to teams.
Provide technical guidance to management and leads a variety of technical project teams.
Provide technical leadership to adopt and implement Global Wealth quality automation.
Provide technical support in the selection of suppliers.
Provide technical support to QA Inspectors and / or other departmental personnel as required.
Provide training to all levels of organization and suppliers.
Provide updates on project status and support team meetings with customers.
Recommend
Recommend appropriate action.
Recommend delivery methodologies and frequency while balancing the QA practitioners' needs.
Recommend disposition of product quality related issues.
Recommend solutions to identified problems.
Recommend solutions to complex issues.
Report
Report audit findings and summaries to the leadership, and close the necessary actions.
Report to Executive Management on quality systems operation.
Represent
Represent Quality on cross-functional teams.
Research
Research and evaluate new industry standard tools.
Research, develop, and deploy advanced automated testing methodologies.
Research and implement best practices for competency and QA skill development.
Research, evaluate and come up with test requirement in release process.
Research problems and recommend solutions.
Review
Review and Approval of designated project documentation in product creation projects.
Review and approval of development documentation.
Review and approve quality system documentation as necessary.
Review and coordinate all necessary changes performed by service / other departments.
Review and enhance company quality policy procedures and standards.
Review and evaluate policies and procedures include SOPs and BCPs.
Review and / or update all Supplier files on an annual basis.
Review and verification of documentation and metrics) at Product Realization Process milestones.
Review CMM or inspection data for the qualification of new product and production tooling.
Review GD&T and gauging methodologies for assigned programs.
Review new design specifications and provides input from quality and manufacturability perspective.
Review product concepts, testing, evaluates results using appropriate statistical analysis tools.
Review project related documentation to ensure its accuracy.
Review software design, change specifications, and plans against process requirements.
Review tooling requirements and perform IQ / OQ / PQ as necessary.
Run
Run sprint planning meetings for DevOps and Quality Engineering projects.
Run tests and Report results.
Set up
Set and track quality assurance goals.
Set up and maintain test configurations for end-to-end / system testing.
Set up environment to do product testing, and defect verification.
Supervise
Supervise QE Technicians in daily responsibilities / priorities.
Support
Support and complete warranty reduction projects as a member of assigned commodity teams.
Support and contribute in Lean Sigma programs and activities towards delivery of the set target.
Support and ensure on-time product re-certifications.
Support and lead FMEA / Risk Management processes and activities.
Support and mentor problem solving and root cause analysis activities.
Support CAPA program requirements to assure timely closure.
Support CAPA, SCAR and NCR investigation and administration.
Support CAPA Teams that are addressing manufacturing or design related issues.
Support compliance and continued certification to ISO 13485 Quality Systems Standard.
Support customer, supplier or internal quality audits - develop any required corrective actions.
Support external audits and inspections as directed.
Support First Article Inspections.
Support key processes as subject matter expert.
Support Major Quality System investigations (i.e. CAPAs, HHEs, StopShip, etc.).
Support new product launch, the development of FMEA, CP and APQP.
Support project team, determining goals and objectives for the projects.
Support quality improvement and cost reduction initiatives.
Support sterilization and environmental monitoring activities.
Support submissions to regulatory agencies (MDR / Vigilance system).
Support supplier change as required, ensuring quality requirements are meet.
Support Supplier evaluation and related records.
Support the development of others by means of coaching, training.
Support the identification of risks to product quality and the development of mitigation plans.
Support the manufacturing team with product quality and reliability testing.
Support various process changes, design.
Teach
Teach, train, and lead work-cells in adopting continuous process improvement initiatives.
Test
Test Method Development and Inspections.
Track
Track and report on quality metrics, highlight opportunities and drive improvement.
Track and trend CAPA metric data and create presentations for management review.
Track internal processes effectiveness, and customer complaints.
Track timelines and facilitating the required Quality Engineering deliverables.
Understand
Understand and monitor customer usage.
Understand industry trends.
Understand, meet and exceed internal and external customer expectations to create positive impact.
Understand Okta backwards and forwards from core products to service infrastructure.
Understand problem-solving and quality improvement tools and techniques.
Understand the value of Accessibility and use creativity in finding accessible solutions.
Update
Update or create work instructions to document current processes.
Uphold
Uphold and contribute to testing best practices in agile environment.
Utilize
Utilize Design of Experiments (DOE) , Statistical Process Control.
Utilize the concepts of continuous improvement including Lean.
Validate
Validate manufacturing processes, test methods, and quality processes as required.
Work with
Work closely with Product Owners to identify and capture non-happy path requirements.
Work closely with technical support to understand and resolve customer issues.
Work well with others, especially across a variety of functional groups.
Work with AH to develop field repair techniques.
Work with cross-functional teams to complete all assigned tasks.
Work with engineering in the completion of product verification and validation.
Work with other Engineers in test across the organization to share knowledge and improve your skills.
Work with project teams to determine the change control approach for complex projects.
Work with QA practices and approaches, including CI / CD practices.
Work with software development team to troubleshoot and resolve test defects.
Work with Software Quality Engineers (SQE's) to prioritize script development.
Work with suppliers and in house production team to ensure and enforce quality requirements.
Write
Write and present technical reports.
Write quality procedures / Write Laboratory documents.
Most In-demand Hard Skills
The following list describes the most required technical skills of a Quality Engineer:
Medical Device
FDA
Manufacturing
Selenium
Quality Assurance
Technical Field
Keyboard Use
Python
GMP
Excel
Iso 14971
Jenkins
Risk Management
GIT
Jira
SQL
Agile
Design
Javascript
Test Automation
Word
Six Sigma
Root Cause Analysis
Use Of Quality Tools / Methodologies
Iso 9001
ISO
Fmea
SPC
C#
Statistical / Data Analysis
Report Writing
Powerpoint
Mechanical Engineering
ASQ CQE
Manufacturing Environment
Software Development
Most In-demand Soft Skills
The following list describes the most required soft skills of a Quality Engineer:
Written and oral communication skills
Problem-solving attitude
Analytical ability
Organizational capacity
Interpersonal skills
Attention to detail
Leadership
Work independently with little direction
Communicate at multiple levels in the organization
Presentation
Self-starter
Team player
Time-management
Detail-oriented
Resolve quality-related issues in a timely and effective manner
Self-motivated
Creative
Quick learner
Collaborative
Independently mobile
Critical thinker
Flexible
Multi-task
Highly motivated
Ability to manage multiple tasks
Adaptable to changes
Decision-making
Organized
Planning
Teamwork