Main Responsibilities and Required Skills for Production Manager
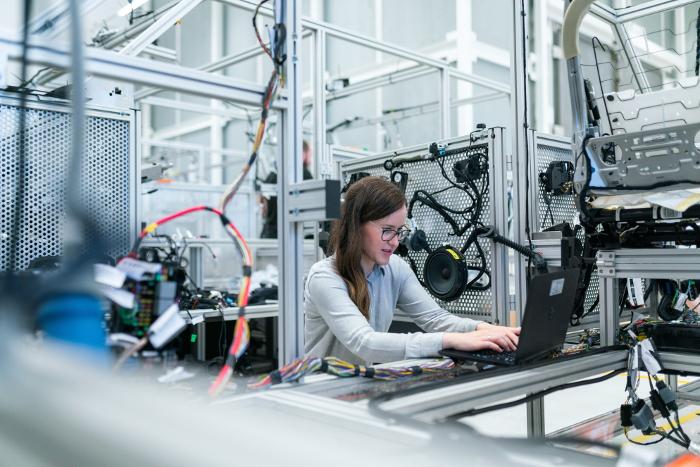
A Production Manager is a professional who monitors the production processes and adjusts schedules as needed. They develop and maintain teamwork effectiveness in production and ensure compliance to company policies and government regulations. In this blog post we describe the primary responsibilities and the most in-demand hard and soft skills for the primary responsibilities and the most in-demand hard and soft skills for Production Managers.
Get market insights and compare skills for other jobs here.
Main Responsibilities of Production Manager
The following list describes the typical responsibilities of a Production Manager:
Adhere
Adhere to all security procedures for ensuring confidentiality of donor information.
Administer
Administer ERP / MRP system, creating BoMs, Work Orders, Operations, etc. as needed.
Analyze
Analyze, optimize, and control production costs.
Analyze Production Coordinators production reports.
Analyze sales trends and patterns to anticipate future needs.
Anticipate
Anticipate and communicate issues with potential solutions or dependencies.
Apply
Apply and executes policies and standards.
Approve
Approve worker performance metrics and results.
Assist with / Assist in
Assist engineering with problem-solving.
Assist Supervisors in any situations that arise requiring additional assistance or approval.
Assist with vetting and interviewing new production hires as needed.
Attend
Attend occasional press checks for printed material.
Attend press checks (as needed).
Audit
Audit and report inventory while making recommendations on which items to order and restock.
Begin
Begin the day with inspection of par levels and ingredients.
Build
Build production books & timelines (e.g. post schedule, shoot request calendars).
Build Purchase Orders for talent, directors and other service providers.
Coach
Coach and train existing and new supervisors.
Coach Shift Supervisors as needed.
Co-chair
Co-chair publication meetings.
Co-develop
Co-develop, analyzes and improves financial models to support profitability.
Co-lead
Co-lead Safety Committee program.
Collaborate
Collaborate with fulfillment team to ensure accurate on hand inventory levels.
Collaborate with H.R. Manager to enforce policies and procedures.
Collaborate with leadership.
Collaborate with supply chain on the production schedule to meet demand.
Communicate
Communicate changes to all applicable people.
Communicate with maintenance for proper set-up of equipment.
Communicate with other employees to ensure production is completed on time and efficiently.
Conduct
Conduct daily meetings with plant group to review any plant or customer issues.
Conduct other responsibilities as required by management.
Confirm
Confirm crew & equipment rentals.
Control
Control labor and raw material costs.
Controller
Controller and schedule as directed.
Coordinate
Coordinate and execute resourcing plans as it relates to staffing, equipment, and raw materials.
Coordinate and manage shipments to various channels alongside the supplier.
Coordinate communications which lead to positive results.
Coordinate reviews and edits of marketing materials between internal client and design teams.
Coordinate with key internal and external production stakeholders.
Coordinate with shipping for the incoming materials and outgoing orders.
Create
Create and maintain inventory and maintenance log.
Create, manages, and provides weekly reporting on efficiency, timeliness and quality.
Create mutual communication and collaboration on projects, processes and initiatives.
Create procedures and a culture that rewards smooth, fast, safe and quality work.
Create production schedules.
Define
Define required supplies, tools and equipments for operations.
Deliver
Deliver weekly, monthly and quarterly forecasts and metrics.
Determine
Determine effective work processes.
Develop
Develop and coach employees in order to retain and grow organizational talent.
Develop and implement cost reduction initiatives.
Develop and maintain effective cross functional working relationships and partnerships.
Develop and maintain metrics that drive improved quality.
Develop and maintain teamwork effectiveness in production.
Develop and motivate direct reports with consistent feedback and recognition.
Develop key metrics to measure success and communicate performance to the team.
Develop production program and guidelines to support company objectives.
Drive
Drive a continuous improvement culture by instilling Plan, Do, Check, Act methodology.
Drive continuous improvement roadmap, increasing build productivity.
Drive Lean Initiatives, Continuous Improvement and 5S.
Drive operational performance and challenge team to meet goals and objectives on time.
Drive unit performance through effective use of meetings, KPIs and resolution of variances.
Empower
Empower, coach direct staffs for people development.
Enforce
Enforce Studio policies and protocols on-set in conjunction with production management.
Ensure
Ensure accident investigations are competed in a timely manner.
Ensure compliance to company policies.
Ensure compliance to government regulations, farm practices and SOPs.
Ensure employee compliance of all policies and procedures.
Ensure machine inspection reports are being completed.
Ensure overall management of the day to day operations and maximizes productivity.
Ensure planned KPI's of quality, efficiency and performance are met or exceeded.
Ensure regulatory compliance across a range of federal, state, and local agencies.
Ensure staff training records are complete and current.
Ensure that all products are dated coded according to company procedures.
Ensure that safe conditions exist at all times within the work environment.
Ensure training of staff according to training plans and to continue to develop their competencies.
Establish
Establish and maintain high standards in relation to Environmental Health & Safety work practice.
Establish procedures, metrics and processes to drive productivity and optimization.
Evaluate
Evaluate practices, procedures and facilities to assess risk and adherence to the law.
Execute
Execute logistics plan to move products and packages to reach destinations on schedule.
Hire
Hire crew and cast for all shoots.
Identify
Identify and Implement New Proccess, Technologies and Systems.
Identify and implement operational improvements.
Identify criteria and use customer-centric methods to prioritize backlog items.
Identify production issues and proactively loopback this information to the producer.
Implement
Implement and maintain production standards and quality controls.
Implement effective problem-solving systems.
Improve
Improve upon existing metrics as appropriate.
Influence
Influence and provide innovative ideas to continuous improvement.
Inform
Inform the team on the advancement of the deliverables (planned versus actual) and address gaps.
Insist
Insist on ethical conduct and maintain the values that underlie the corporate culture.
Interact
Interact with vendors and suppliers.
Interpret
Interpret specifications and make judgments about the acceptability of production process.
Investigate
Investigate production issues and develop resolutions.
Keep
Keep a weekly synopsis of discipline and / or sequence accomplishments and next steps.
Keep your "finger on the pulse” of the production floor.
Lead
Lead and coach employees, while supporting all training initiatives.
Lead and motivate a team of production workers.
Lead development of new creations in keeping with traditional lines.
Lead projects and key initiatives, set standards, and train staff.
Learn
Learn, over time, how to operate all plant machines, and how to trouble shoot including PLC etc..
Look
Look for continuous improvements to ensure customer satisfaction.
Maintain
Maintain accurate vendor records, following Purchase Ordering Systems.
Maintain and operate the machines.
Maintain and promote strong work ethics and uphold all KTP policies and procedures.
Maintain and update departmental Safety Data Sheets (SDS).
Maintain a safe, clean and organized workplace.
Maintain / assist in the development of records.
Maintain employee engagement through communication and team building.
Maintain focus on KPIs including safety, quality, and on time delivery to manage the business.
Maintain functional knowledge of all production equipment operation.
Maintain par level for raw ingredients.
Make
Make great tasting speciality coffee accessible to coffee lovers across the UK.
Make sure governance rules are followed and responsibilities are carried out.
Make sure production targets are met.
Manage
Manage all stakeholder communication between other ILM sites and with productions.
Manage and motivate subordinates, encourage communication, and create harmony in workplace.
Manage and report all issues and challenges to the Head of Operations.
Manage and train employees to execute day-to-day responsibilities.
Manage approximately 2 direct report supervisors and indirectly 4 leads and 20 to 35 employees.
Manage budget of assigned department in accordance with annual productivity improvement targets.
Manage client, vendor and team communication.
Manage, develop and guide a team of six Supervisors.
Manage High Precision Assembly of Electro-Mechanical Components.
Manage production budget, comparing the budget to actual variances and gross margin targets.
Manage project flow and workload with retouchers and prepress throughout the production process.
Manage strategic Instructor photo shoot booking around class programming.
Manage weekly time sheets, production output and bonus structure for production team members.
Manage workflow across the creative and marketing teams to ensure a seamless process.
Meet
Meet and greet clients & talent during auditions and at start of sessions.
Monitor
Monitor and deliver improvement plans based on Key Performance Indicators.
Monitor ANDON occurrences.
Monitor content production with the internal studio, publish and liaise with the media agency.
Monitor crew attendance and managing vacation requests.
Monitor pre-construction deadlines & liaise with internal departments.
Monitor production levels and pick rates for associates.
Monitor productivity of the injection molding process and production scrap.
Monitor standard work for OSS / Team Leads and operators.
Monitor the production processes and adjust schedules as needed.
Optimize
Optimize your supplier's capabilities with the product strategy.
Organize
Organize and develop staff to ensure a high performing team.
Oversee
Oversee daily performance against established standards and schedules.
Oversee department payroll by scheduling, approving and processing hourly employee hours.
Oversee the stores operation including the supervision of the Stores supervisor.
Oversee the corrigenda process in conjunction with the Production Assistant.
Oversee the planning, setup and leading of these productions.
Oversee the uploading of content / Proofreading and compliance with deadlines and client brief.
Oversee the workforce of production supervisors and their teams in all aspects of manufacturing.
Participate in
Participate actively with knowledge & improvement ideas to continuous improvement program.
Participate in continuous improvement process.
Participate in planning personnel safety and plant protection activities.
Participate in product teardowns for root cause failure analysis, DOE, 5Y, 8D, etc..
Perform
Perform any other related duties as required.
Perform method analysis with the supervisors and implement lean concepts wherever possible.
Perform proactive cost comparison and analysis as requested.
Perform special projects as needed.
Pitch
Pitch, plan, shoot and edit videos independently and as a team.
Prepare
Prepare and conduct weekly Safety Meetings and Safety Inspections.
Prepare and distribute clash reports to facilitate the coordination process.
Prepare reports to update upper management on food production activities.
Prioritize
Prioritize opportunities to improve the service and drive improvement initiatives.
Process
Process and cleaning validation strategy.
Provide
Provide coaching and performance communication to support development.
Provide input and support in creation and furtherance of capital projects.
Provide motivation, support, and guidance to all team members.
Provide regular formatted reports to management.
Provide training and coaching to ensure compliance with Safety standards and incident prevention.
Purchase
Purchase of raw material and special items.
Receive
Receive assignments in task and objective oriented terms.
Recognize
Recognize potential problems and recommends solutions.
Report
Report back to Executive Producer & Series Producers.
Represent
Represent MAC Renovations in a professional and respectful manner.
Request
Request capital expenditures where appropriate.
Resolve
Resolve issues as needed to construction sites within the division.
Review
Review, communicate and respond to Social Media reviews.
Review locations, models, and styling of all photoshoots to ensure high-quality production.
Review, streamline and implement new processes.
Supervise
Supervise and motivate a team of workers.
Supervise and manage all plant operations and activities related to the manufacturing processes.
Supervise special projects that relate to loan production arena.
Support
Support client-centered delivery performance results.
Support Supervisors and Leads in managing crew.
Support the Head of Supply Chain with special projects as needed.
Support the team as challenges arise or when volume demands.
Tag
Tag photo and video assets for public facing channels with an eye towards SEO.
Take
Take ownership for the customer service resolution process in their departments.
Train
Train and supervise production staff.
Train and monitors employees on proper work procedures to ensure.
Travel
Travel locally to visit clients and vendors as and when necessary.
Update
Update cost information in price file.
Work with
Work across disciplines to find smart ways to deliver on the product's promise.
Work closely with Maintenance Department to ensure ongoing assessment for equipment.
Work closely with online course providers to ensure successful delivery of our online courses.
Work on every aspect of the product, being responsible for the production process.
Work with departments to implement social distancing protocols for office / work spaces.
Work with editors and authors on data visualization projects.
Work with management staff to improve performance of the unit.
Work with management team to implement the company's policies and goals.
Most In-demand Hard Skills
The following list describes the most required technical skills of a Production Manager:
Manufacturing
Management
Manufacturing Environment
Supervisory
Production
Outlook
MS Office
Lean Manufacturing
Line Management
Animation
Operations Management
Health And Safety
Change Management
Shotgun
Materials Management
Bending
Business Objectives Alignment
Customer Service
Product Management
Plant
VFX
Wearing Steel Toe Shoes
Extended Periods of Prolonged Standing
Lifting
Reaching
Working on your Feet
Most In-demand Soft Skills
The following list describes the most required soft skills of a Production Manager:
Written and oral communication skills
Leadership
Organizational capacity
Problem-solving attitude
Interpersonal skills
Attention to detail
Time-management
Organized
Analytical ability
Planning
Detail-oriented
Team player
Multi-task
Decision-making
Positive
Team leadership
Presentation
Resourceful
Innovative
Creative
Negotiation
Self-starter
Ability to manage multiple tasks
Entrepreneurial mindset
Flexible
Self-motivated
Driven
Innovation
Bilingualism
Decision-making skills