Main Responsibilities and Required Skills for a Manufacturing Supervisor
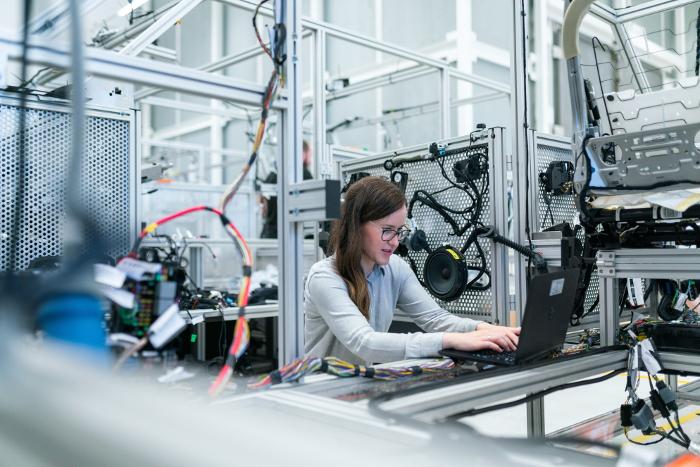
A Manufacturing Supervisor is a professional who plays a crucial role in overseeing and managing the production process within a manufacturing setting. They are responsible for ensuring smooth operations, maintaining quality standards, and coordinating the efforts of the production team. In this blog post, we describe the primary responsibilities and the most in-demand hard and soft skills for Manufacturing Supervisors.
Get market insights and compare skills for other jobs here.
Main Responsibilities of a Manufacturing Supervisor
The following list describes the typical responsibilities of a Manufacturing Supervisor:
Accomplish
Accomplish manufacturing staff results by communicating job expectations.
Achieve
Achieve weekly production schedules and department goals.
Address
Address areas of concern with employees to promote excellent performance.
Address performance issue as necessary.
Address safety issues immediately with Manager.
Administer
Administer union collective bargaining agreement and site and Company policies.
Alleviate
Alleviate pain, restore health and extend life.
Analyze
Analyze operations, functions, finished products.
Analyze production data to identify trends and areas for improvement.
Analyze the current situation and propose ideas for improvement (DMAIC).
Assess
Assess the impact of proposed decisions and initiates appropriate actions.
Assign
Assign daily work assignments and responsibilities to the team and stakeholders as required.
Assign tasks and schedules priorities to achieve the greatest production with the best efficiency.
Assign work according to production schedule.
Assist with
Assist Manager with employee rating forms in their designated area.
Assume
Assume the lead on cross functional teams / projects.
Assure
Assure all team members are appropriately trained.
Attend
Attend and participate in staff meetings of manufacturing.
Carry out
Carry out basic quality and testing checks.
Change
Change working positions from standing, sitting, bending and lifting up to 30lbs of parts and boxes.
Coach
Coach new packaging employees on new equipment, procedures, regulations, etc..
Coach teams, provide guidance, direction, training, resources, and time.
Coach unsafe behaviors of production workers.
Collaborate
Collaborate with other departments to optimize production efficiency.
Collaborate with suppliers and vendors to ensure timely delivery of materials.
Communicate
Communicate daily performance of the shift and any issues to management team.
Communicate production goals, results, quality, and operation observation with employees daily.
Communicate to employees on a timely basis.
Communicate with Supervisor of next shift on current production issues.
Communicate work center / department objectives and results.
Complete
Complete Batch Production Records under cGMP, and documents in detail.
Complete job requisitions and submits for approval.
Complete proper production reporting for the area.
Conduct
Conduct performance reviews and recommend training or development opportunities.
Conduct regular inspections to ensure equipment functionality.
Confer
Confer with interdepartmental personnel to discuss production procedures and resolve problems.
Consolidate
Consolidate and optimize team skills, by motivating and coaching the staff.
Contribute to
Contribute to the definition and application of control and follow-up measures for his team.
Coordinate
Coordinate and manage material flow and accuracy, quality, and maintenance support requirements.
Coordinate and oversee the work of production staff.
Coordinate day to day activities.
Coordinate TM duties with necessary departments.
Coordinate with engineering teams for process optimization.
Coordinate with maintenance personnel for equipment repairs and maintenance.
Counsel
Counsel employee on attendance to improve performance.
Create
Create a climate of trust and respect within the group.
Create a realistic development plan.
Create, develop, or improve new or existing SOPs related to the department.
Define
Define and communicate clear and realistic expectations, deliverables, limitations and resources.
Demonstrate
Demonstrate and train team on proper manufacturing production processes, practices, and procedures.
Determine
Determine needs for additional training, overtime to meet production schedule.
Develop
Develop and implement safety protocols.
Develop and maintain production reports and records.
Develop and maintain relationships with key stakeholders.
Develop comprehensive operating plans and monitors achievement of business and financial goals.
Develop reporting procedures and systems.
Develop schedules and labor requirements for assigned areas.
Develop schedules and manpower requirements for assigned areas.
Develop World Class People.
Direct
Direct day-to-day activities of the warehouse.
Document
Document / Record cGMP data and information for processing steps and / or equipment activities.
Drive
Drive continuous improvement activities.
Drive positive results in operational Key Process Indicators.
Encourage
Encourage team to be involved in decisions, encourages talent development.
Enforce
Enforce plant rules, monitors attendance and provides corrective action as necessary.
Enforce policies, practices, procedures and tracking for production operations.
Ensure
Ensure alignment to the regulatory, corporate and customers' requirements.
Ensure all packaging procedures are being performed at the highest standard by leads.
Ensure compliance with environmental regulations.
Ensure compliance with safety program.
Ensure compliance with safety regulations and quality standards.
Ensure daily all electronic and paper-based logs are filled out accurately and on time.
Ensure operation of equipment by calling for repairs.
Ensure production boards are checked hourly for rate attainment, scrap, down time, down time reason.
Ensure regulatory compliance while promoting safe working methods and a safe environment.
Ensure replacement / upgrade of manufacturing equipment's.
Ensure team members have clear goals and performance expectations.
Ensure that the employees respect set work sequences.
Ensure the backup of operational supervision during week shift when needed.
Ensure the safe use of equipment and schedule regular maintenance.
Ensure timely and accurate staging and sterilization of supplies / equipment.
Establish
Establish or adjust work procedures to maintain production schedules.
Establish, set and maintain process standards and capacity, measuring performance to plan.
Evaluate
Evaluate departmental labor efficiencies and provides input into annual standard setting process.
Evaluate employee performance and provide feedback.
Facilitate
Facilitate corrections to malfunctions within process control points.
Focus on
Focus on achieving results.
Follow
Follow ISO14001 guidelines as they relate to specific job activities.
Follow-up with
Follow-up with each employee to discuss performances regarding HST, GMP\u0026rsquo.
Foster
Foster a positive work environment and promote teamwork.
Foster Collaboration and Teamwork.
Gather
Gather additional data from appropriate areas.
Handle
Handle general employee inquiries and solve problems.
Hire
Hire and retain a diverse, highly qualified staff and provides ongoing performance feedback.
Identify
Identify and eliminate potential hazards.
Identify and resolve production bottlenecks.
Identify appropriate functional groups for involvement.
Identify appropriate resources to resolve routine issues.
Identify personal career wants / needs and evaluate against the business needs.
Implement
Implement and enforce company policies and procedures.
Implement and maintain standard operating procedures (SOPs).
Implement and monitor lean manufacturing principles.
Implement continuous improvement processes and cost savings.
Implement cost reduction strategies.
Implement strategies to enhance productivity and efficiency.
Influence
Influence others to support a course of action.
Initiate
Initiate paper work maintaining discipline as needed.
Interact with
Interact directly with regulatory agencies and provides information as required.
Interact with clients during initial and subsequent manufacturing campaigns.
Interact with peers in operations and within other cross-functional groups.
Interface with
Interface with Micro and Quality Assurance on environmental issues, investigations & audits.
Interview
Interview candidates for positions on the direct staff.
Lead
Lead continuous improvement initiatives.
Lead investigations for production, quality, safety, and environmental incidents.
Lead with Integrity and Respect.
Maintain
Maintain all records relevant to equipment, cleaning and processes.
Maintain a safe and professional work environment.
Maintain equipment per manufactures' recommendations for preventive maintenance.
Maintain good housekeeping and keeps all equipment in good operating condition.
Maintain and improve 5-S principles.
Maintain inventory of all cleanroom garments.
Maintain orderly lab spaces.
Maintain plant policies and procedures.
Maintain professional and technical knowledge by attending educational workshops.
Maintain time and production records.
Maintain time and production records for direct reports.
Maintain workflow by monitoring steps of the process.
Make
Make budgetary recommendations on capital expenditures and direct / indirect labor.
Manage
Manage and control production budgets.
Manage and review production data with team members and resolve any manufacturing related issues.
Manage, coach and report on employee productivity.
Manage inventory of cellular products and laboratory supplies.
Manage manufacturing operations through SAP functions.
Manage set-up, adjustments, and removal of dies within stamping press.
Manage the releasing of material from internal and external vendors.
Manage training, attendance, safety awareness and performance evaluations for your team.
Mentor
Mentor and develop lower level supervisors.
Monitor
Monitor and manage inventory levels.
Monitor and report progress of safety objectives, performance against schedule and number of defects.
Monitor compliance to safety rules, work expectations and housekeeping standards.
Monitor employee productivity and provide constructive feedback.
Monitor employees' work levels and review work performance.
Monitor production processes to identify areas for improvement.
Monitor product quality, react to quality incidents, and coordinate corrective actions as necessary.
Monitor the production process.
Notify
Notify proper person and Supervisor when W.I.P. stock shortage exists.
Operate
Operate Filter integrity devices to confirm the integrity of filters pre and post use.
Organize
Organize and follow customer visits and audits.
Organize ideas, prepares A / V aids, keeps to time frame and present persuasively.
Oversee
Oversee Manufacturing Associates to assure they are working in a cGMP-compliant and safe manner.
Oversee safety of operations.
Oversee the 2nd shift Cleaning crew and Compounders.
Own
Own and deliver long term overtime management plan.
Participate
Participate in interviews for new hires.
Participate in proactive team efforts to achieve departmental and company goals.
Participate in process transfer activities from process development to manufacturing.
Perform
Perform audit of operators in their section twice per shift.
Perform other duties as assigned.
Perform other related tasks as assigned.
Perform other responsibilities as directed / assigned by management.
Perform routine administrative tasks (SOP, CAPA, CC, Deviations).
Perform the set-up, operation, cleaning and break-down of process equipment.
Plan
Plan and administers procedures and budgets.
Plan and schedule production activities.
Plan, manage and monitor all manufacturing projects.
Prepare
Prepare and submit reports.
Prioritize
Prioritize workloads based on urgency or availability of inventory.
Provide
Provide annual budget recommendations and perform routine variance analysis.
Provide a pipeline of productivity ideas for future.
Provide assistance with Engineering Samples and tooling development tests.
Provide budget recommendations, perform cost reduction and variance analysis.
Provide day-to-day operations and logistics support for wafer Fab, DFAB / ASSM, and Test areas.
Provide direct supervision to production hourly employees.
Provide feedback to individuals on productivity and quality of workmanship.
Provide leadership and direction to an assigned manufacturing team.
Provide ongoing coaching and feedback consistent with employee needs.
Provide proper components, W.I.P. stock, and packaging to line as needed.
Provide support to maintenance or the die repair teams as needed.
Provide support to senior manufacturing staff as needed.
Provide technical leadership and training as needed.
Raise
Raise issues to the appropriate level for resolution.
Reach
Reach with hands and arms.
Read
Read drawings and Shop Orders.
Receive
Receive direction from Manager and implement initiatives with respect to overall objectives.
Receive instructions through oral and written communications accurately and quickly.
Recognize
Recognize accomplishments within department through reward and recognition programs.
Recommend
Recommend and requisition assemblers for temporary manufacturing staff.
Recommend measures to improve productivity and product quality.
Recommend personnel actions.
Recommend personnel actions, such as hires, promotions, transfers, or disciplinary measures.
Recommend process changes to improve productivity.
Recommend the hiring & termination of hourly employees as necessary.
Reconcile
Reconcile count discrepancies and input count data.
Report
Report environmental incidents immediately to supervisor of the affected area.
Reset
Reset equipment as needed.
Resolve
Resolve conflicts or issues that arise within the production team.
Review
Review and approves Master Manufacturing Work Orders.
Review and processing of work orders to production floor.
Review manufacturing documentation (batch records, etc.).
Review status of production schedules to identify and resolve problems.
Review, understanding, and compliance with ArcherDX HIPAA Security policies and procedures.
Select
Select, supervise, and trains employees, in compliance with company standards, and policies.
Select the country where you are applying for employment, and review.
Stay updated with
Stay informed about emerging technologies and their potential impact on manufacturing processes.
Stay updated with industry trends and advancements in manufacturing techniques.
Streamline
Streamline communication between 2nd shift employees and Plant Manager.
Supervise
Supervise 4-5 extrusion machine operators.
Supervise the packing teams and the packaging process.
Supervise TM personnel in day to day functions.
Supervise, train, lead and mentor employees.
Support
Support all development and technical transfer manufacturing projects.
Support Autonomous maintenance.
Support / backup of Manufacturing Manager.
Support new product development activities by delivering custom products upon request.
Support production staff in understanding company policies and practices.
Support the Manufacturing Manager on the annual budget building and follow-up, and CAPEX management.
Support the Manufacturing Manager on the mid and long-term deliverables of the department.
Train
Train and mentor new employees.
Train direct labor associates on job responsibilities and priorities.
Understand
Understand detailed area operations (function specific).
Update
Update and approve time sheets.
Use
Use various computer applications to enable efficient planning and scheduling.
Verify
Verify that master test parts verification was performed on jobs.
Work
Work on the production team, as needed, to deliver product in a timely manner.
Work toward continuous improvement within their area to meet company goals.
Work with compliance to ensure department is meeting and exceeding quality goals.
Work with employees to meet their development needs.
Work with Facilities and Validation to maintain manufacturing equipment.
Work with Operations and Shipping and Receiving to coordinate storage of materials.
Most In-demand Hard Skills
The following list describes the most required technical skills of a Manufacturing Supervisor:
Proficiency in production planning and scheduling software.
Knowledge of quality management systems (e.g., ISO standards).
Strong understanding of manufacturing processes and equipment.
Experience with lean manufacturing principles and methodologies.
Proficiency in data analysis and statistical tools (e.g., Six Sigma).
Knowledge of supply chain management and logistics.
Familiarity with computer-aided design (CAD) software.
Proficiency in inventory management software.
Technical expertise in the specific industry or manufacturing sector.
Knowledge of safety regulations and compliance.
Most In-demand Soft Skills
The following list describes the most required soft skills of a Manufacturing Supervisor:
Strong leadership and managerial skills.
Excellent communication and interpersonal skills.
Problem-solving and decision-making abilities.
Effective time management and organizational skills.
Adaptability and flexibility in a dynamic work environment.
Teamwork and collaboration skills.
Conflict resolution and negotiation skills.
Attention to detail and quality orientation.
Ability to motivate and inspire the production team.
Strong analytical and critical thinking skills.
Conclusion
Being a Manufacturing Supervisor requires a diverse skill set that combines technical expertise, leadership abilities, and effective communication. By understanding the primary responsibilities and acquiring the most in-demand hard and soft skills, Manufacturing Supervisors can excel in their role and contribute to the success of the manufacturing process.