Main Responsibilities and Required Skills for Maintenance Lead
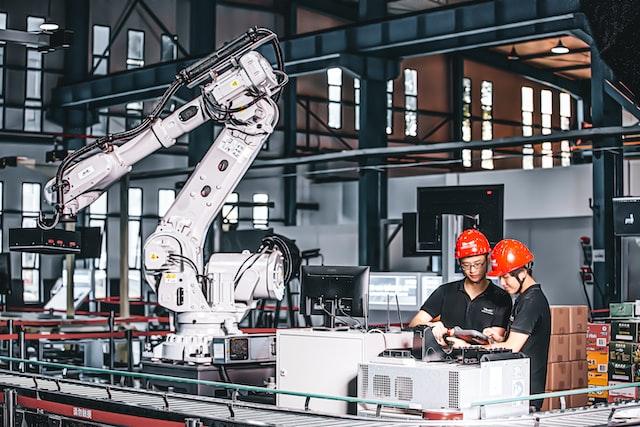
A Maintenance Lead is a professional who troubleshoots, maintains, and repairs electrical and mechanical equipment. They schedule and perform regular maintenance and ensure compliance to governmental regulatory and safety programs and processes. In this blog post we describe the primary responsibilities and the most in-demand hard and soft skills for Maintenance Leads.
Get market insights and compare skills for other jobs here.
Main Responsibilities of Maintenance Lead
The following list describes the typical responsibilities of a Maintenance Lead:
Adhere to
Adhere to all Occupational Health and Safety Standards.
Adhere to GMP's and Health and safety rules as outlined in employee handbook.
Analyze
Analyze the needs of business partners and clearly identify project terms of reference.
Apply
Apply all applicable OSHA and related local safety requirements to all assigned work.
Arrange
Arrange annual equipment inspections (Cranes, CO monitors, Fire equipment).
Assess
Assess and minimize the impact of projects on work flow.
Assess building systems to plan work assignments and project schedules.
Assist with
Assist Chief Engineer with daily departmental operations and projects.
Assist in the ordering of mechanical components and maintaining the inventory of critical parts.
Assist other departments with moving furniture and unloading and storing supplies.
Assist with commissioning new equipment.
Assist with installing new equipment and systems.
Assist with the coordination and manages equipment and work site.
Assume
Assume a leadership role in identifying possible productivity improvements projects.
Attend
Attend meetings and trainings as required.
Carry out
Carry out maintenance of buildings and technical installations.
Check
Check all employees are performing duties in a safe manner.
Clean
Clean equipment, inside and outside windows, stock rooms and restrooms.
Clean HVAC / Exhaust units and roof of debris.
Clean or lubricate shafts, bearings, gears, or other parts of machinery.
Collaborate with
Collaborate with other workers to repair or move machines, machine parts, or equipment.
Collaborate with Specialty Snow Removal Supervisor and Team Leaders to plan maintenance activities.
Complete
Complete daily / weekly close out reports in office setting on desktop computer.
Complete repairs and maintenance of all equipment and facility to ensure all warranty needs are met.
Complete tasks as assigned by maintenance supervisor.
Comply with
Comply with all company safety and risk management policies and procedures.
Comply with departmental policy for the safe storage, usage, and disposal of hazardous materials.
Conduct
Conduct monthly department and weekly Safety Tool Box meetings.
Conduct performance evaluations that are timely and constructive.
Conduct preventative maintenance programs and keep accurate maintenance records.
Conduct site assessments to understand the technical risks associated with the maintenance program.
Contribute to
Contribute to keeping areas in and around facilities clean and hazard free.
Control
Control and coordinate the procurement of parts and maintenance consumables.
Coordinate
Coordinate daily / weekly / monthly / quarterly / annual PM schedules.
Coordinate employees involved in carrying out projects.
Coordinate Installation and / or Movement of Equipment.
Correct
Correct minor operational issues with baggers.
Create
Create plans to fix any ongoing production issues and present to sr. management.
Create reports and documentation.
Define
Define and implements maintenance processes.
Develop
Develop and execute Preventative Maintenance Program for automated equipment.
Develop when required specific training and development opportunities for employees.
Diagnose
Diagnose problems, replace or repair parts, test and adjust.
Direct
Direct the performance of contracted maintenance work as needed.
Direct the setup and maintenance of equipment related to snow and ice maintenance.
Document
Document all machine maintenance activities and communicate with other staff.
Document all work in the CMMS system.
Document and follow up with tram accident reports as needed.
Enable
Enable a high performance culture through leading, developing and coaching employees.
Enforce
Enforce a zero tolerance to unsafe working practices to target a zero-accident rate.
Ensure
Ensure 5S and Lean Manufacturing practices being executed.
Ensure compliance to governmental regulatory OSHA and safety programs and processes.
Ensure equipment is properly input into Megamation for all equipment.
Ensure GMP's and safe food handling practices are being followed.
Ensure maintenance and repair work is completed safely, effectively, and in a timely manner.
Ensure part control and traceability.
Ensure PM schedules are being executed on time and to expectations.
Ensure positive relationships with internal and external customers and contractors.
Ensure proper care in the use and maintenance of equipment and supplies.
Ensure satisfactory performance of preventative maintenance schedules.
Ensure that all OEE and 5S measures are in place and updated as required.
Ensure that approaches and solutions are clearly presented in the proposal.
Ensure that established OEE quality standards are achieved within the assigned processes.
Ensure that issues are formulated strategically to mitigate risks.
Ensure that operators use standard work and associated tools to meet standards.
Ensure that safety standards are identified, communicated and achieved within the assigned processes.
Ensure the facility is maintained in clean and orderly fashion and complies with AIB guidelines.
Ensure the sustainable and responsible development of the units.
Ensure timely communication to Affiliates about upcoming workload.
Escalate
Escalate complaints to management when necessary.
Establish
Establish strong relationships with all work groups and works with a collaborative style.
Estimate
Estimate costs to repair machinery, equipment, or building structures.
Examine
Examine machinery or mechanical equipment.
Fabricate
Fabricate, install, and maintain photography and inspection workstations as required.
Follow
Follow all company safety policies and procedures to ensure a safe working environment.
Follow and adhere to the all policies and procedures.
Follow Fair Housing regulations.
Follow guidelines for preventative maintenance of production or mechanical equipment.
Guide
Guide and mentor existing, as well as new shift mechanics.
Guide new and seasonal employees during peak production months.
Handle
Handle discipline and termination of employees as needed and in accordance with company policy.
Help
Help determine the department's needs for purchasing and inventory management.
Identify
Identify reasons for malfunction and complete repairs and / or maintenance.
Identify training needs and establishes technical expertise within the business unit.
Identify and prequalify outside subcontractors to help where required.
Identify areas of improvement and offers suggestions to improve the community.
Implement
Implement technical solutions to improve equipment up-time and asset utilization.
Inspect
Inspect, operate, or test machinery or equipment to diagnose machine malfunctions.
Install
Install, replace, or change machine parts and attachments, according to production specifications.
Instruct
Instruct operators in the use and care of equipment.
Insure
Insure the availability of an adequate operating inventory of tools and supplies.
Insure that Preventative and Predictive Maintenance programs are executed as scheduled.
Keep
Keep work area clean and clear of hazards.
Lead
Lead and develop the team of experienced electricians.
Lead a team of Building operators and Maintenance workers.
Lead Root Cause Analysis (RCA) for mechanical failures.
Maintain
Maintain a clean and safe working environment as per company requirements.
Maintain a clean and safe workplace.
Maintain a friendly and personable attitude.
Maintain a high level of personal Customer Service.
Maintain Best Practices and cross-organizational consistency.
Maintain component records.
Maintain detailed records of repair and maintenance tasks completed.
Maintain maintenance tools in good working condition and stores them properly when not in use.
Maintain Safety Lock-out tags.
Maintain service and inspection records of repairs on all equipment.
Maintain s Maintenance / Sanitation Activity Tags Log book and provide updates.
Maintain Tool / Parts Area.
Maintain work area in safe and clean manner.
Make
Make sure employees have the required skills.
Make sure projects comply with the standards, regulations and procedures in effect.
Manage
Manage and monitor construction and repair projects.
Manage contractor's performance during their assigned shift.
Manage defects and equipment failures.
Manage office furniture reconfigurations, furniture moves and office moves, as requested.
Meet
Meet with partners and customers to discuss strategic agreements.
Mentor
Mentor and trains less experienced staff in all aspects of the job.
Model
Model and teach finding cost effective solutions to tasks.
Monitor
Monitor and coordinate external subcontractors.
Monitor and test equipment needed to perform maintenance and repair activities.
Monitor department vacation and schedules coverage as required to meet the needs of the business.
Negotiate
Negotiate and update all service contracts.
Operate
Operate cutting torches or welding equipment to cut or join metal parts.
Operate Electrical equipment (general building technology, EMA, BMA).
Operate equipment as required.
Optimize
Optimize & standardize work processes.
Organize
Organize and oversee the schedules and work of maintenance and janitorial staff.
Patrol
Patrol the roads to identify work that needs to be done and stay current with area activities.
Perform
Perform additional duties as requested, including energy usage tracking and reporting.
Perform bi-annual reviews of maintenance personnel.
Perform coaching to maintenance associates assigned to their specific shift.
Perform duties of a general maintenance person.
Perform electrical diagnostics.
Perform function of PRM role in support of AMO (Approved Maintenance Organization .).
Perform general cleaning duties of buildings or properties.
Perform maintenance and repairs on electrical assets, machinery and equipment.
Perform miscellaneous job-related duties as assigned.
Perform plumbing repairs including faucets, sinks, urinals, toilets, drains, and valves.
Perform routine maintenance on the equipment.
Perform special projects as assigned.
Prepare
Prepare site for installation (Electrical, Air, Gas, Water, Network, Lighting).
Prepare weekly work schedules.
Promote
Promote and support Continuous Improvement activities in Manufacturing.
Promote a safe work environment through personal actions and identifying any safety concerns.
Promote sound occupational health and safety management.
Provide
Provide daily direction to the associates within the department.
Provide feedback to Supervisor on labor, material and equipment demands needed to achieve schedule.
Provide troubleshooting and support for plant in the assigned area 24hrs / 7days a week.
Reach
Reach with hands and arms, grip and squeeze hands.
Read
Read and understand control schematics.
Receive
Receive parts and consumables from Vendors.
Recommend
Recommend additional training for shift mechanics as needed.
Record
Record production, repair, and machine maintenance information.
Remain
Remain Product "expert” through ongoing product knowledge training.
Repair
Repair and maintenance costs and budget development and management for the line.
Repair and maintenance of Material Handling Equipment.
Repair and maintenance of refrigerated warehousing production equipment.
Repair and maintain current equipment and systems as needed.
Replace
Replace worn or damaged parts such as hoses, wiring, and belts, in small machines and equipment.
Report
Report any broken, damaged, or missing tools to your supervisor.
Report any concerns and / or problems to supervisor through daily written and verbal reporting.
Report any foreign material findings to your supervisor.
Report any injury, unsafe act or condition, equipment failure, or potential failure.
Report any unsafe conditions, incidents or injuries to Supervisor immediately.
Report potentially unsafe conditions.
Represent
Represent the company in a professional and courteous manner with internal and external customers.
Resolve
Resolve problems / issues in an effective and timely manner.
Resolve customer and associate opportunities with GSM / DM and HR Manager.
Respond to
Respond to building emergencies on after hours on-call schedule.
Respond to notifications provided by the Team Leader and planning an appropriate responses.
Review
Review full scope of work performed by on site maintenance staff.
Run
Run daily meetings - to plan out shift duties and projects.
Schedule
Schedule and perform regular maintenance, cleaning, and repairs on all process equipment.
Schedule preventive and floating maintenance, if applicable.
Schedule the planning meetings for planned shutdowns.
Spot
Spot checking inventory status periodically will be required.
Supervise
Supervise multiple jobs for quality and efficiency.
Supervise and implement the preventative maintenance program.
Supervise team of up to 3 full-time employees.
Support
Support innovation objectives to ensure the company's long-term success.
Support innovation and new product development to create added value for the client.
Take
Take out and empty trash compactor.
Take responsibility for our actions and learn from our mistakes.
Train
Train and provide direction of employees within the department.
Train new employees in the safe, quality-oriented operation of production equipment and systems.
Train or manage maintenance personnel or subcontractors.
Train / coach the operators to correct and prevent defaults.
Train new employees on the proper way to stack product on pallets.
Train team members to troubleshoot and resolve problems.
Troubleshoot
Troubleshoot, maintain, and repair industrial electrical and electronic control systems and devices.
Troubleshoot equipment or area issues promptly and is part of the solution and remedy.
Understand
Understand and adhere to Good Manufacturing Practices.
Update
Update and maintain a real time backup of all PLCs, HMIs, and VFD program.
Upgrade
Upgrade equipment when necessary to ensure optimal performance.
Use.
Use all prescribed personal protective equipment.
Use instructions and established guidelines to perform the functions of the job.
Work
Work efficiently independently as well as part of a team.
Work organization and planning.
Work to meet all the set KPIs by the maintenance manager.
Work with a sense of urgency to complete tasks safely, effectively and efficiently.
Work with EHS to produce Safe Work procedure.
Work with the supervisor to develop longer term goals.
Most In-demand Hard Skills
The following list describes the most required technical skills of a Maintenance Lead:
Maintenance
Most In-demand Soft Skills
The following list describes the most required soft skills of a Maintenance Lead:
Written and oral communication skills
Organizational capacity
Interpersonal skills
Analytical ability
Multi-task
Time-management
Problem-solving attitude
Attention to detail
Diplomatic
Leadership
Professional maturity
Work with minimum supervision
Competent
Confident
Critical thinker
Detail-oriented with demonstrated accuracy
Inspire others
Motivated leader