Main Responsibilities and Required Skills for Line Leader
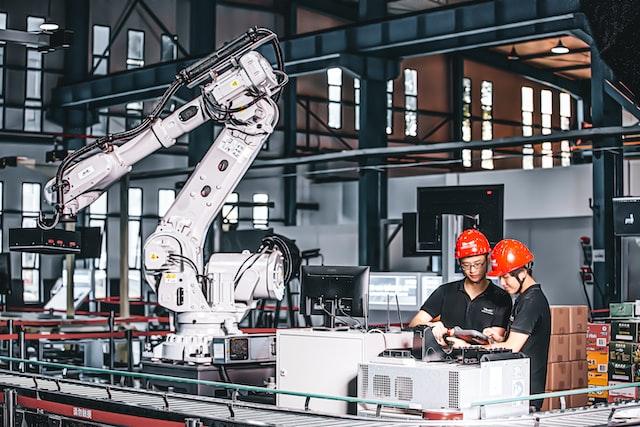
A Line Leader is responsible for supervising line members in a production environment. They ensure that requirements for each position on the line are met and pan production operations. In this blog post we describe the primary responsibilities and the most in-demand hard and soft skills for Line Leaders.
Get market insights and compare skills for other jobs here.
Main Responsibilities of Line Leader
The following list describes the typical responsibilities of a Line Leader:
Actualize
Actualize and train operators on operational instructions.
Adhere to
Adhere to employee health and safety guidelines.
Administer
Administer a technically sound Environmental Monitoring Program, updating as appropriate.
Anticipate
Anticipate and drive proper alignment and prioritization between the lab and production teams.
Assist in
Assist and assure that department training needs are being addressed.
Assist and support peers with change projects.
Assist in developing personnel.
Assist in maintaining an operating budget for the QA laboratories.
Assist in problem solving efforts related to analytical or microbial issues.
Assist in resource management processes and recruitment.
Assist in tracking CAPA, CASR and LIR's for laboratory equipment and facilities.
Assist management in managing these.
Assist Shift Leader in ensuring KPIs are met daily.
Assure
Assure cleaning execution and / or validation are conducted as required.
Assure test methods are followed.
Assure the compliance with safety, environmental regulation and safety equipment.
Attend
Attend plant MBR meetings to communicate and oversee lab issues.
Attract
Attract and retain suitable technical experts for the business centre.
Champion
Champion Continuous Improvement efforts to drive positive results compared to goals.
Check
Check tare weight of scale and ensure tare weight is being maintained during packaging process.
Coach
Coach, develop and mentor employees in areas of responsibility.
Collect
Collect accurate data for PRE, PROD, and POST production.
Communicate
Communicate any inaccuracies, problems, trends, investigate and resolve issues immediately.
Communicate effectively both verbally and in writing with managers and colleagues.
Communicate to laboratory associates daily while maintaining a constant lab presence.
Communicate to line personnel daily while maintaining a constant line presence.
Communicate to the Production supervisor issues with the line or personnel.
Communicate with assigned line crew regarding daily schedule.
Complete
Complete Daily Line Production Report.
Complete forklift operational checks at the beginning of each shift.
Conduct
Conduct assigned safety investigations and ensuring completion of resultant actions.
Conduct Line Clearance as per SOP.
Conduct regular project audits and reviews of final deliverables within the BC.
Contact
Contact Indirect Labor Material Handler to bring additional components for production line as needed.
Contact with vendors and / or their technical support staff.
Coordinate
Coordinate corrective action with minimal supervision.
Coordinate execution of the Environmental Monitoring program.
Coordinate operators and assign tasks.
Coordinate packaging needs (proper size, type, and timing) with appropriate batching employee.
Coordinate packaging needs (proper size, type, and timing) with appropriate batching person.
Create
Create a positive and inclusive work environment that embraces diversity.
Create a positive work environment by developing a rewarding recognition program.
Define
Define shop expectations.
Deliver
Deliver on Brand Promises through team execution.
Determine
Determine key differentiators that enable our value proposition.
Develop
Develop and Coordinate Workflow.
Develop plans for efficient use of material, machines and labour.
Discuss
Discuss where the run is at and any issues encountered.
Drive
Drive a culture of engagement through the team and department.
Drive lab efficiencies and MSP (Master Schedule Performance) performance.
Engage
Engage in drafting own goals, lead the process of development of team goals and growth planning.
Enhance
Enhance and stand for quality, integrated design, collaborative practice and design excellence.
Ensure
Ensure achievement of production throughput against stated capacity targets.
Ensure all records are completed appropriately.
Ensure all required samples are being pulled.
Ensure animal feed is bagged, sealed, neatly stacked, and recorded at shift-end.
Ensure bags are being scaled to the correct weight.
Ensure completion of required training for all employees.
Ensure compliance with all HR practices, policies and procedures.
Ensure employees are following SOPs and delivering a high-quality product.
Ensure pallets are neatly stacked.
Ensure production line standards are met.
Ensure production runs are executed efficiently, with high quality and minimal waste.
Ensure production schedules are met and deals with problems that may occur.
Ensure product rotation process meets corporate guidelines.
Ensure quality and efficiency standards are met.
Ensure skid ticket information is accurate.
Ensure that batch records are completed and submitted for auditing in a timely manner.
Ensure the accurate and timely fulfillment of the orders within department.
Ensure the area meets required hygiene standards.
Ensure we can achieve our KPIs and targets.
Escalate
Escalate production issues to Area Manager or Production Manager as needed.
Escalate production issues to Shift Lead / Production Manger as appropriate.
Establish
Establish / communicate job performance standards and work procedures.
Evaluate
Evaluate impact analysis on solution options and assess and manage associated risks.
Execute
Execute department batch audit and release procedures.
Follow
Follow and communicates clear daily action plans on specific goals and objectives.
Follow and enforce all GMP's and Safety Procedures as outlined by FGF.
Follow through with oven speeds and adjust when necessary.
Generate
Generate business value for the Group and deliver best-in-class solutions to our Customers.
Guide
Guide, motivate and develop direct subordinates within HR policies.
Identify
Identify and communicate some preventive maintenance needs.
Identify and implement quality, productivity and organizational improvements.
Identify areas of downtime and work on continuous improvement to smooth out issues.
Identify improvement opportunities.
Initiate
Initiate, manage, and make decisions which impact production scheduling.
Interface
Interface with store leadership regarding inventory discrepancy and product flow issues.
Keep
Keep the line clean, organized and free of any dust, debris at all times.
Keep the work area clean and organized.
Lead
Lead and drive the relationship with the key stakeholders, COE and Regional CC and ITS CC teams.
Lead by example and fosters an environment of mutual respect and team work among Team Members.
Lead by example and train, develop, and inspire the production team.
Lead efforts required to deliver quality and compliance performance for the shift.
Lead Root Cause Problem Solving (RCPS) discussions and activities.
Lead, coach, mentor and train Leaders and Team Members.
Lead the development of goal setting for the team and individuals on the team.
Lead the production team for a full production line or multiple lines.
Lead tracking and trending of KPI s including implementation of corrective actions.
Lead workshops resulting in tangible key performance indicator improvements.
Learn
Learn to operate and maintain all equipment in department.
Maintain
Maintain 100% ad in stock throughout the Grocery and General Merchandise areas.
Maintain accurate records.
Maintain a clean and organized workstation and line.
Maintain a high level of product quality and traceability during product assembly.
Maintain and improve housekeeping / hygiene levels.
Maintain and sustain right first-time batch culture, by following BOM's and weighing out correctly.
Maintain a safe and clean work environment by educating and directing personnel on proper GMP.
Maintain back room organization in Grocery and General Merchandise areas.
Maintain clean work environment (all zones).
Maintain clean work environment (Production Floor).
Maintain effective employee relations.
Maintain process flow and documentation according G. M. P. and Quality Standards.
Maintain proper staffing levels on production shift.
Maintain visible lead for adherence to procedures and instructions.
Make
Make one annual presentation at a conference or event attended by current or future clients.
Make appropriate adjustments to daily staffing levels based on work load.
Make sure local and contractual agreements are followed.
Manage
Manage budget accountability for Headcount, Overtime, and direct expenses for a shift and / or line.
Manage challenging customer escalations and non-conformities.
Manage / leads front line employees as well as potentially exempt employees.
Manage personnel and processes to ensure laboratory meets all associated quality standards.
Manage production assembly lines.
Manage the Throughput, Quality and Line Staff.
Mobilize
Mobilize expertises and internal / external resources in a matricial and international context.
Monitor
Monitor all phases of the production line and quality of product being produced.
Monitor and maintain all safety equipment and tools.
Monitor break times of operators on line.
Monitor change over and / or line set up efficiency.
Monitor equipment / process to ensure that products are manufactured within specification.
Monitor team member work practices and providing corrective action where necessary.
Monitor the Quality of product by completing the In-Process Tests throughout the production run.
Monitor the consistency of the product (watch for color changes or color variation during a run).
Operate
Operate forklift, if forklift-operating requirements met.
Operate some machinery on the production line when needed.
Oversee
Oversee personnel and processes to ensure full compliance with internal and external regulations.
Oversee personnel and processes to ensure production meets all associated quality standards.
Oversee that employees are working within safety guidelines and using required PPE at all times.
Palletize
Palletize product as it comes off the various production lines.
Participate in
Participate in site evaluation of PIER's (Planning Investment Electronic Request).
Participate in Tier 1 and production OEE progressive review meeting.
Partner
Partner with the Maintenance Mechanic to troubleshoot mechanical problems and repairs.
Perform
Perform above items while doing direct labor in assigned area.
Perform daily T2 huddle as required.
Perform in-process checks and inspections within specified time frames.
Perform periodic bag seal inspections.
Perform periodic checks on product yield / recovery during the run.
Perform Quality checks of the line.
Perform root cause analysis and resolve problems.
Place
Place scoops in cans / jars / buckets and place lids on cans / jars / buckets.
Plan
Plan production operations, establishing priorities and sequences for manufacturing products.
Prepare
Prepare daily process performance documentation such as (shift summary, OEE, downtime reports).
Prepare for the following days production.
Process
Process, raw material inventory management, supplier delivery performance, and team projects.
Promote
Promote a safe work environment throughout the store.
Provide
Provide direction to Packagers.
Provide information to employees and management, participate in and lead meetings.
Provide leadership and line management to the team.
Provide leadership during problem solving situations related to laboratory issues.
Provide mentorship, motivation, and performance management in a business environment.
Provide on the job training to new employee.
Provide product expertise within team, and respond to operator queries.
Provide timely coaching, counseling and feedback.
Read
Read ingredients and count how many bags are on a pallet.
Reduce
Reduce waste and energy consumption on line.
Report
Report all unsafe work areas.
Retain
Retain responsibility for product from initial assembly to final distribution.
Review
Review completed PBR's each shift for document accuracy.
Review daily schedules to work load.
Review, monitor, and evaluate individual production and quality.
Review total labour charges for line.
Review work order for assembly instruction.
Serve
Serve as a role model for future leaders.
Set-up
Set-up the manufacturing equipment and process safely and efficiently.
Share
Share in the preparation of the annual budget and any updating reviews.
Stop
Stop any observed unsafe acts and obey facility safety rules and procedures.
Supervise
Supervise line members to ensure that requirements for each position on the line are met.
Supervise store operations overnight.
Supervise, train, and develop subordinates.
Support
Support Corrective and Preventive Action (CAPA) investigations, planning and implementation.
Support quality system expectations; and ensure adherence to cGMPs.
Support safety policies and programs.
Support weekend operations in lieu of the team leader as require.
Take
Take that first one by applying to be a Line Lead.
Train
Train Line Workers on the procedure to assemble products per assigned role for the day.
Understand
Understand and effectively use the rewards and recognition programs.
Understand equipment on his / her line and troubleshooting some mechanical problems.
Update
Update production metrics on hourly production whiteboard.
Use
Use of all hand tools as needed.
Utilize
Utilize the OMS system to help achieve production targets.
Verify
Verify components on work order to ensure correct number of components are available for production.
Verify daily schedule to assign priorities upon discussion with PCT Leader or Team Leader Improver.
Work with
Work closely with the Business Unit Leads to drive improvements and deliver departmental targets.
Work in conjunctions with other departments for positive production results.
Work well with multiple departments.
Work with cross-functional groups to identify, address and evaluate impact of distressed inventory.
Work with shift foremen to have consistency on all shifts.
Work with the appropriate recruitment agency to deal with staffing issues (eg) absence reporting.
Most In-demand Hard Skills
The following list describes the most required technical skills of a Line Leader:
Business
Manufacturing
Manufacturing Environment
Most In-demand Soft Skills
The following list describes the most required soft skills of a Line Leader:
Written and oral communication skills
Interpersonal skills
Leadership
Organizational capacity
Attention to detail
Problem-solving attitude
Time-management
Solve problems
Accountable
Accuracy in work
Adapt to a changing environment quickly
Dealing with others
Follow written, verbal and diagrammatic instructions
Identifying issues
Positively influence other team members
Presentation
Provide current, direct, complete, and "actionable” positive and corrective feedback to others
Provide leadership
Think independently
Work effectively at all levels in a collaborative team environment