Main Responsibilities and Required Skills for Supply Chain Manager
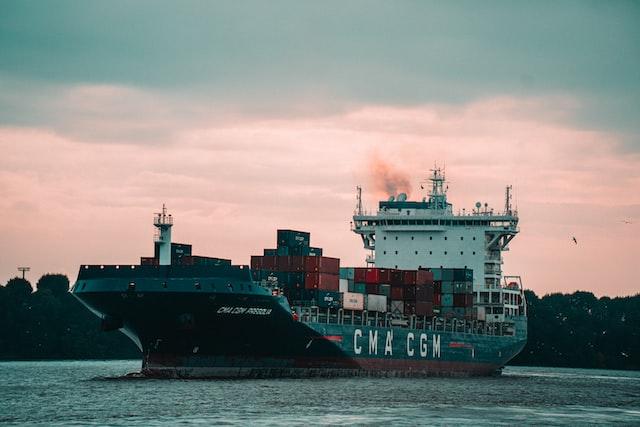
A Supply Chain Manager is a professional who plans, develops and implements purchasing policies and procedures. They maintain best practices associated with managing supply chains and negotiate and maintain relationships with key suppliers. In this blog post we describe the primary responsibilities and the most in-demand hard and soft skills for Supply Chain Managers.
Get market insights and compare skills for other jobs here.
Main Responsibilities of Supply Chain Manager
The following list describes the typical responsibilities of a Supply Chain Manager:
Accept
Accept input, assess differing viewpoints objectively, gains alignment with minimal noise.
Align
Align with process and seasonal capacity requirements.
Analyze
Analyze information about supplier performance and procurement program success.
Analyze inventory data to anticipate future needs, reduce waste, and improve business profitability.
Analyze needs to anticipate demand.
Anticipate
Anticipate stops and starts of ranges of products as well as the obsolete components.
Arrange
Arrange, execute and communicate all supply chain activities for development and clinical programs.
Articulate
Articulate clear vision and goals.
Assess
Assess competition and market opportunities and threats.
Assess and anticipates customer needs.
Assess supply chain risks, develop risk mitigation strategies, and execute plans to minimize risk.
Assist in / Assist with
Assist in ensuring policies are adhered to and operated efficiently.
Assist in managing shipment and custom activities for import services.
Assist in training and on boarding of new employees.
Assist with product sourcing.
Balance
Balance and prioritize inventory needs across all 3 business models.
Build
Build and maintain good relationships with vendors.
Build coalitions and partnerships.
Build deep and resilient relationships with our suppliers.
Build the transparent relationship with 4PL-operator.
Can
Can present without undue tension and nervousness.
Capture
Capture or proposal lead experience.
Check
Check product and wastage data for potential issues.
Collaborate with
Collaborate cross-functionally stakeholders (finance, marketing and category team).
Collaborate with colleagues and peers.
Collaborate with Innovative 3Mers Around the World.
Collaborate with Operations and Customer Service teams.
Collaborate with various supply chain teams to deliver.
Communicate
Communicate a compelling vision to staff.
Communicate forecasts to vendors to ensure acceptable inventory levels.
Consolidate
Consolidate various components from numerous suppliers with efficiency and accuracy.
Coordinate
Coordinate planning meetings, assuring part scheduling.
Coordinate serialization activity with the APU team and ITS team.
Coordinate weekly production follow up meeting.
Coordinate with Buying & Merchandising to plan in-line with future growth and flow of goods.
Coordinate
Coordinate with Marketing on product colors, attributes and addressing slow moving materials.
Counsel
Counsel employees on career growth.
Create
Create and maintain key performance indicators.
Create POs and coordinate shipment with international suppliers.
Define
Define standard and custom product requirements.
Design
Design and develops company policies for area of responsibility and anticipates their impact.
Design the first iteration of supplier portfolio.
Determine
Determine and maintain adequate safety stock for all products.
Determine and report on key supply chain KPIs.
Determine key supply chain OKRs.
Develop
Develop a 1-3-5 year strategic plan for all Supply Chain activities.
Develop analytical reports to deliver information to business partners and stakeholders.
Develop and administers training on CSOS business processes.
Develop and implement effective strategic sourcing initiatives.
Develop and implement QA processes for our vinyl toy manufacturing.
Develop and maintain excellent relationships with our manufacturing and logistics partners.
Develop and maintain rolling 12 month product forecast.
Develop and negotiate new product development contracts and production commercial contracts.
Develop and / or implement solutions in a timely manager.
Develop a new inventory management system.
Develop / Enhance Supply Chain processes leveraging cost to service mindset.
Develop, manages, coordinates global sourcing processes and practices with internal stakeholders.
Develop Master Production Schedules that optimize inventory investment and manufacturing resources.
Develop reports on budgets and control costs within established standards as required.
Develop risk mitigation analysis and plans.
Discuss
Discuss contracts with clients.
Drive
Drive cross departmental S& OP and Value Stream Mapping.
Drive Integrated Business Planning (IBP) process for the APU (Site S&OP Process).
Drive supplier improvement initiatives to continually lower risk and reduce lead times.
Drive supplier negotiations, contracts and agreements to ensure Delta's business success.
Drive value and savings for categories.
Engage with
Engage with suppliers to improve productivity, quality, and efficiency of operations.
Ensure
Ensure company and our vendors meet or exceed regulations.
Ensure high performance in our daily supply chain utilizing the resources and budget allocated.
Ensure NDA, SOW's and Supply Agreements are positioned appropriately.
Ensure planning of Visual inspection, All Star packing and Blister packing.
Ensure proper on hand supply quantities across all centers nationwide.
Ensure proper supply of all packaging material as per MRP based on Net Demand in Athena.
Ensure qualified clinicians are accountable to the organization.
Ensure staff technical training and proficiency.
Ensure strategies pertaining to seasonal demand fluctuations are executed by colleagues.
Ensure supply, production, and customer requirement needs are met.
Ensure that all suppliers meet the established quality standards.
Ensure that their Team members adhere to the Thales Group Purchasing policies.
Ensure timely issuance of orders with good inventory balance across multiple warehouses.
Ensure timely PO creation and audit of same.
Establish
Establish a method to monitor the execution of the his / her team member activities.
Establish and drive E2E cost saving and / or cost avoiding initiatives throughout total business.
Establish and maintains good working relationships with vendors.
Establish and monitor operational performance via KPIs such as in stock rate and inventory turns.
Evaluate
Evaluate vendors' qualification, work with buyer to conduct factory audit.
Faster
Faster DNA results improve lives.
Focus on
Focus on Customer - Acts with urgency to address service issues.
Focus on next generation ideas that enable and deliver on strategic focus.
Forecast
Forecast demand, place orders and ensure stock availability.
Foster
Foster Collaboration and Teamwork.
Foster strong inter-departmental communication practices.
Help
Help talent grow and develop.
Help to define and monitor the schedule and deliverables associated with the acquisition.
Help us deliver solutions that ensure Life Is On everywhere, for everyone and at every moment.
Hire
Hire and retain a diverse, highly qualified staff and provides ongoing performance feedback.
Historical
Historical and forecasted, using appropriate metrics.
Identify
Identify resource needs and develops supporting justifications for them.
Identify and Achieve Service Excellence as Defined by our Customers.
Identify and help with the implementation of Best Practice supply chain processes in the channel.
Identify needs and implement more as needed.
Identify opportunities and implement processes to reduce costs and improve timelines.
Identify process bottlenecks and implement solutions.
Identify process bottlenecks and improvements in a timely manner.
Implement
Implement a framework for best practices in supply chain and inventory management.
Implement, lead and manage Campbell's Supply Chain initiatives.
Implement new or improved supply chain processes.
Implement supply chain processes and procedures.
Improve
Improve relationships with key suppliers and negotiate terms in accordance with business goals.
Inspire
Inspire trust and supports others through own authenticity and following up on commitments.
Interview
Interview and make staffing recommendations.
Keep up-to-date
Keep up-to-date testing information on all new products.
Lead
Lead and facilitates Monthly Demand Planning and Monthly Supply Planning Meetings.
Lead and oversees the purchasing of goods and services.
Lead a small team that includes a Buyer / Planner and two Materials Associates.
Lead Change - Takes initiative.
Lead, coach and mentor the supply chain team.
Lead, drive and sustain continuous improvement utilizing established tools and methodologies.
Lead interdepartmental communication as the operations leader.
Lead meetings with Operations and Design Engineering teams.
Lead price and contact negotiation with raw material, MRO and services suppliers.
Lead Production Planning / Scheduling, Purchasing, Materials Management and Logistics.
Lead the development of functional strategy.
Lead with Integrity and Respect.
Lead yellow belt projects to improve effectiveness and / or efficiency (Kaizen Activities).
Liaise with
Liaise with internal resource contacts and external stakeholders.
Maintain
Maintain best practices associated with managing clinical supply chains.
Maintain inventory levels for purchased goods.
Maintain optimum inventory levels as aligned with Supply Chain leadership.
Manage
Manage 3rd party logistics partner.
Manage all satisfaction, utilization, and ROI calculations of the solutions delivered.
Manage and continuously improve purchasing process.
Manage and decrease inbound cost such as freight cost, custom, and truck delivery.
Manage and mentor a team of Supply Chain Associates.
Manage and operate MRP / ERP systems including SAP IBP.
Manage capacity planning to identify medium to long-term resource requirements.
Manage cross-functional projects against plans and objectives to meet commitments and goals.
Manage current store and offsite capacities looking to reduce reliance where required.
Manage existing supply chain and determine key supply chain KPIs.
Manage finished goods, raw materials, and packaging inventory levels against the supply plan.
Manage forward buy / bulk order processes.
Manage guesstimation settings liaising with the wider business.
Manage issues and expectations across a broad range of skill sets and locations.
Manage item forecasts by DC.
Manage key stakeholders through the bid and mobilization activity.
Manage operational performance and change management support.
Manage product storage, handling and distribution.
Manage sourcing of comparators with third parties as needed to support studies.
Manage supplier contracts and pricing.
Manage supplier selection process based on price, quality, support, capacity and reliability.
Manage the budget, monitor and optimize project planning and control resources.
Manage the planning and supply of components through the MRP system.
Manage the Regulatory bodies' customs reqmts as required.
Manage the safety stock level by business planning.
Manage weekly forecasts and replenishment planning for all material categories.
Minimize
Minimize Logistics expenses while maximizing customer fill rates.
Monitor
Monitor and correct inventory levels at warehouses to maximize working capital.
Monitor monthly KPIs (backlog, WIP, efficiency, .).
Monitor on-time shipment and shipping quality and accuracy.
Monitor vendor performance in accordance to SCM guidelines.
Negotiate
Negotiate an accepted portfolio meeting the most strategic needs of the category.
Negotiate and maintain relationships with key suppliers.
Negotiate blanket purchase orders when appropriate and monitors costs during time period.
Negotiate competitive rates with existing and new vendors for long-term collaboration.
Negotiate pricing for materials.
Negotiate sea and air freight quotes with carriers.
Oversee
Oversee and manage the metal reconciliation process and metal forecasting.
Oversee and prepare Request for Quotation (RFQ) packages and vendor and contractor proposal.
Oversee the S&OP process with marketing / sales and develops monthly and annual demand forecasting.
Oversee the analysis of data and information.
Oversee the evaluation of the cost and quality of goods or services.
Oversight
Oversight on all Financial Control Activities of the scope described in the general mission.
Own
Own direct customer contact with customer supply chain personnel.
Participate
Participate in budgeting exercises for the PA site.
Participate in vendor qualifications, quality agreements and audits / inspections.
Perform
Perform liaison role between production team, engineering team, customers and vendors.
Perform other similar and related duties as required.
Place
Place purchase orders to carry adequate safety stock.
Plan
Plan, develop and implement purchasing policies and procedures.
Plan, organize, direct, control and evaluate daily operations.
Plan purchases of materials considering the demand forecast, product assortment and lead times.
Prepare
Prepare and present inventory reports.
Promote
Promote positive relationships.
Provide
Provide cover / back up to the Supply Chain team.
Provide leadership and mentorship to department.
Provide planning, procurement, logistics, customs support and oversight for all assigned products.
Provide recommendations on packaging design and distribution.
Provide support in a fast-paced healthcare environment.
Provide weekly reports to upper management for these goals.
Provide weekly status for WOR reviews, risk to PLT and Revenue plan.
Recommend
Recommend / maintain proper staffing levels to execute required activities.
Reconcile
Reconcile tolling quantity, calculate, post and review resulting MUVs and P&L entries monthly.
Represent
Represent supply chain in cross-functional CMC Team Meetings.
Review
Review and lead the Demand Planning and Customer Service processes.
Review and management of slow moving and distressed inventory.
Review and reconcile demand forecast vs.
Review part availability including quality approval prior to scheduling.
Seek
Seek out new suppliers to drive product / cost improvements or diversify our supply chain.
Support
Support expedite requests.
Support management of the Business Process Management Community.
Support procurement & replenishment component for OEM suppliers.
Support Sales in driving successful JBP.
Support self-inspection, problem solving and identifying corrective actions to improve performance.
Support supplier relationship and supplier performance management initiatives.
Support the acquisition and distribution for critical need products.
Take
Take ownership of the Daily Bread Food Fund and the annual budget for food purchasing.
Track
Track deliveries and shipments to update inventory in addition to document it in system.
Track performance metrics to identify opportunities and challenges.
Train
Train and evaluate others, and provide constructive feedback.
Transact
Transact all receipts, transfers, and finished good builds in ERP system in a timely manner.
Understand
Understand store specific needs and manage stock flow solution requirements accordingly.
Understand 'what good looks like' and maintain standards through leading by example.
Work
Work closely with Hardware Engineering to influence technical design decisions.
Work closely with managers scheduling production to maintain a 'just-in-time' level of inventory.
Work closely with our Supply Chain Lead to tender valuable negotiations with new suppliers.
Work closely with the head of production to set production goals.
Work to clarify long term organizational goals.
Work with accounts payable and IT on process improvements.
Work with finance, sales, and manufacturing team to determine best vendors and distributors.
Work with freight forwards and transportation companies to achieve best outcomes.
Work within the Export / International Channel.
Work with manufacturing to ensure that there are sufficient resources to fulfil customer demand.
Work with our engineering and finance team to reduce costs and reduce cash tied up in inventory.
Work with the Future Aircrew Training (FAcT) capture team to develop the aviation solution.
Most In-demand Hard Skills
The following list describes the most required technical skills of a Supply Chain Manager:
Procurement
Business
Manufacturing
Purchasing
Management
Manufacturing Environment
MS Office
Materials Management
Operations
APICS
Change Management
Customer Service
ERP
Marketing
Operations Management
Most In-demand Soft Skills
The following list describes the most required soft skills of a Supply Chain Manager:
Written and oral communication skills
Interpersonal skills
Analytical ability
Problem-solving attitude
Leadership
Organizational capacity
Attention to detail
Team player
Negotiation
Time-management
Presentation
Self-starter
Decision-making
Organized
Critical thinker
Teamwork
Multi-task
Continuous improvement
Work independently with little direction
Creative
Integrity
Management