Main Responsibilities and Required Skills for Plant Manager
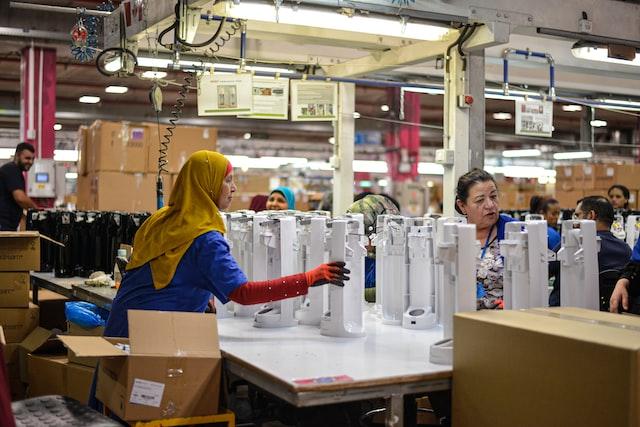
A Plant Manager is a professional who is responsible for overseeing the daily operations of a manufacturing or production facility. They manage staff, ensure production targets are met, monitor quality control, maintain equipment and machinery, and make strategic decisions to optimize the plant's performance and profitability. In this blog post we describe the primary responsibilities and the most in-demand hard and soft skills for Plant Managers.
Get market insights and compare skills for other jobs here.
Main Responsibilities of Plant Manager
The following list describes the typical responsibilities of a Plant Manager:
Abide by
Abide by district policies and procedures.
Adhere to
Adhere / comply with company policies and procedures.
Administer
Administer all company policies in a fair, consistent and reasonable manner.
Allocate
Allocate resources effectively and fully utilize assets to produce optimal results.
Anticipate
Anticipate and provide direction on future capital projects and equipment needs.
Appraise
Appraise customers' requirements for all materials and make sure they are satisfied.
Arrange
Arrange warehouse, goods, plan routes and process shipments.
Assess
Assess system maturity for all plant activities and drive the maturity improvement plan.
Assign
Assign tasks to employees as necessary.
Assist in
Assist in development of training materials, data sets to support department functions.
Assist in Managing all plant Operations.
Assure
Assure that facility is maintained in a safe and comfortable manner.
Assure that the plant meets all environmental and safety standards.
Build
Build a safety culture focused on diligence to best practice and good housekeeping.
Build strong relationships on a foundation of trust, loyalty and authenticity.
Coach
Coach and develop department managers and teams.
Commit
Commit to plant safety procedures.
Communicate
Communicate and maintain positive relationships with the local community.
Communicate and support adherence to all corporate policies.
Communicate business results and identify gaps for improvement of key metrics.
Communicate job expectations.
Communicate with engineers responsible for planning and design of production lines.
Complete
Complete all other work as assigned and provide all other assistance as required by management.
Complete and / or assist in the duties of all jobs related to production as needed.
Compute
Compute rate, ratio and percent, and draw and interpret bar graphs.
Conceive
Conceive, develop and evaluate on-the-job and classroom training in operations-related subjects.
Coordinate
Coordinate all production schedules to ensure staffing coverage and efficiency of plant operations.
Coordinate daily production through most efficient use of equipment, materials and employees.
Coordinate internal resources and third parties / vendors for the flawless execution of projects.
Coordinate maintenance and repairs to ensure a safe working environment.
Coordinate, sets up and implements standard operating procedures for all production operations.
Coordinate the set up and room management to ensure production team meets daily start up metrics.
Create
Create presentations to outline new production strategies.
Create robust, dynamic processes and systems to enable continuous improvement.
Define
Define and manage the execution of the site manufacturing by effective management of the site.
Delegate
Delegate production and food safety compliance responsibility to the Supervisor and QC staff.
Design
Design and implement Safety and Continuous Improvement programs for the manufacturing operators.
Determine
Determine amount of necessary resources (workforce, raw materials etc.).
Determine KPIs and measure them on a regular basis including OEE and Waste.
Develop
Develop and communicate site strategies aligned with corporate strategy and initiatives.
Develop and control profits, plans and budgets.
Develop and drive continuous improvement initiatives.
Develop and fosters plans for the efficient use of materials, machines and employees.
Develop and implement Standard Operating Procedures.
Develop and maintain an effective and committed management team.
Develop and maintain nutrient regime.
Develop and / or approves all plant operating policies.
Develop annual operating plan and capital requirements.
Develop equipment maintenance schedules and recommend the replacement of machines.
Develop manufacturing budgets and plans to meet production goals within budget?.
Develop production schedules and maintain an inventory of raw materials and finished products.
Develop skills in the operations group to build quality into the production process.
Develop strategic direction for the local team complimenting company goals.
Develop team within their individual areas of responsibility.
Develop tools to monitor plant Key Performance Indicators.
Devise
Devise strategies to make production more efficient.
Direct
Direct implementation of departmental objectives, goals and policies.
Direct and manage plant operations for production, maintenance, quality and shipping and receiving.
Direct the testing and assessment of various treatment processes / phases.
Drive
Drive and support continual improvement processes.
Drive positive employee relations through Employee engagement and enablement activities.
Drive quality programs to ensure product meets or exceeds customer expectations.
Drive lean manufacturing initiatives.
Drive success within the daily operations of their business unit.
Drive / Support execution and support initiatives around people and talent development, market.
Drive the use of Lean manufacturing techniques to reduce waste and cycle times within the Plant.
Encourage
Encourage and promote employee engagement to resolve business challenges.
Enforce
Enforce health and safety precautions and actively participate to Health & safety committee.
Ensure
Ensure all compliance needs are met.
Ensure all safety policies and procedures are adhered to Maintain supply and repair budgets.
Ensure all safety procedures and health and safety regulations are met.
Ensure a safe work environment through strict adherence to company safety policies and procedures.
Ensure a smooth and efficient hand off with QA and production teams each day.
Ensure compliance to IATF - 16949 systems and procedures.
Ensure efficiency of operations by optimizing resources.
Ensure good working order of all equipment and facilities on site.
Ensure government and environmental compliance of operations.
Ensure highest quality of handling, processing and storage of raw materials.
Ensure output meets quality standards.
Ensure quality standards are adhered to by all finish goods production departments.
Ensure strong relationships are developed and maintained with key customers and vendors.
Ensure that all personnel are aware of and effectively practice the policies and procedures.
Ensure the appropriate standard operating procedures.
Ensure the site's compliance to SHE, quality and regulatory procedures.
Establish
Establish clear goals that align the plant's efforts with the organization's vision.
Establish operational efficiency objectives and achieve them via a performance review.
Establish workforce and capital requirements to meet business strategies.
Evaluate
Evaluate their performance while motivating them to achieve personal and professional goals.
Examine
Examine product samples and review finished product data.
Facilitate
Facilitate and monitor outbound shipments (BOL processing).
Foster
Foster a culture of continuous improvement and optimize the lean production system in place.
Help
Help meet operational efficiency goals.
Help provide engineering support to solve production issues or process improvements.
Hire
Hire new plant employees.
Identify
Identify training needs.
Identify and develop high potential employees and encourage their professional growth.
Identify and fabricate infrastructure to support safe and efficient operation of new equipment.
Identify and mitigate risks in manufacturing operations that may impact consumer safety.
Identify areas of weakness, train, and document.
Identify quality issues and develop solutions to maximize first-time quality and minimize waste.
Implement
Implement and maintain a 5S program for optimal workplace organization.
Implement and maintain Preventive Maintenance programs.
Implement and monitor processes immediately upon realization of quality control issues.
Implement company directives, policies and procedures.
Improve
Improve communication and flow between departments.
Inspect
Inspect, analyze and recommend ways of improving quality and efficiency.
Inspect, analyze and recommend ways of improving quality and efficiency in production activities.
Interpret
Interpret analytical results to determine necessary changes in treatment parameters.
Issue
Issue Task Analysis directives.
Keep
Keep accurate records of supplies and maintenance of equipment.
Lead
Lead a comprehensive safety program to prevent injuries.
Lead continuous improvement and lean manufacturing activities.
Lead efforts to reduce cost through structured projects that reduce waste and increase productivity.
Lead facility Strategic and Operational planning activities.
Lead rapid improvement events (RIE) to deliver target improvements.
Lead strong internal control process and maintain full compliance with business and government.
Lead the EHSR process by setting a good example.
Liaise with
Liaise as with other departments to ensure all plant expectations are met.
Maintain
Maintain all licenses associated with the operations of the facility.
Maintain and update Work Flow document (Work Order Cycle) as appropriate.
Maintain a positive, proactive labor environment.
Maintain clean and safe plant.
Maintain company records in a manner compliant with operating permits or federal laws.
Maintain existing plant facilities and equipment.
Maintain individual and department performance for established standards.
Maintain metrics and analyze data to assess performance and implement improvements.
Maintain mother plants for research, tissue culture and future production.
Maintain ongoing client interface to keep client informed and enhance client relations.
Maintain production and inventory records.
Make
Make key decisions on plant layout and equipment changes.
Manage
Manage all manufacturing activities in coordination with planning manager.
Manage all supervision functions on a 4 shift operation.
Manage and direct the activities of multiple supervisors and indirectly 200+ hourly associates.
Manage and engage his / her staff based on Cascades' values and business strategy.
Manage capital asset maintenance.
Manage Capital Expenditure, Capacity, and Technology Planning processes.
Manage compliance to all Federal / State / corporate environmental or safety regulations.
Manage continuous improvement integration and cost reduction methods.
Manage labor deployment based on demand and scheduling requirements (manufacturing and warehouse).
Manage production and support activities to ensure that operations sustain.
Manage staff (about 30 people) and social relations within the entity.
Manage team, including performance management, coaching, development.
Measure
Measure productivity by analyzing performance data, financial data, and activity reports.
Monitor
Monitor accident frequency and history and analysis injury data.
Monitor and control capital assets, operating expenses, manpower, wages and salaries.
Monitor operations and trigger corrective actions.
Monitor process KPIs and convert results into PDCA cycle.
Monitor and approve expenditures.
Monitor overall plant performance for production and quality standards.
Motivate
Motivate people, assess and develop employee skills.
Operate
Operate within the approved budget for the plant.
Optimize
Optimize blends based on incoming raw materials.
Optimize process to increase efficiency, product quality and reduce scrap.
Oversee
Oversee all equipment set-ups and troubleshoot quality and machine problems.
Oversee daily floor operations.
Oversee plant operations and ensures compliance with federal and state regulations.
Oversee daily operation and tasks in plant to make sure goals are met or exceeded.
Oversee testing of plant systems and components executed by on-site staff and / or by contractors.
Oversee the development, submission and execution of plant related CAAP's.
Perform
Perform outbound material audits to ensure a quality product is being delivered to the customer.
Plan
Plan and track the shipment of final products according to requirements.
Plan, organize, direct and run day to day operations for an Open-End Yarn Spinning facility.
Plan, organize, direct, and run optimum day-to-day operations.
Prepare
Prepare and execute investment and asset maintenance plans, and meet return on investment targets.
Prepare and manage the plant's budget.
Prepare and submits annual expense and capital budgets.
Prepare, implement and control preventative maintenance programs for all equipment.
Print and review production reports.
Produce
Produce and effectively uses materials and services.
Promote
Promote a Manufacturing Excellence culture that supports employee engagement and continuous.
Promote his / her team's motivation and work environment.
Promote Safety at all times with a strong safety presence on the plant floor.
Provide
Provide an environment which ensures and provides for open and healthy communications.
Provide coaching and direction to ensure success in meeting required outputs and schedules.
Provide direction, supervision and feedback to employees.
Provide facility maintenance and preventive maintenance programs and training.
Provide inspired leadership for the organization.
Provide leadership and training to accomplish Agropur goals and objectives.
Provide leadership, direction, guidance and support to management team and plant personnel.
Provide safety initiatives and promotes safety and housekeeping initiatives.
Put in place
Put in place activities to promote employee mobilization and empowerment.
Recommend
Recommend replacements or adjustments to plant facilities and equipment when necessary.
Recommend organizational changes to enhance the effectiveness of managers and subordinates.
Recruit
Recruit, manage and develop plant staff.
Recruit, train and supervise all direct reports.
Report
Report need for major repairs or maintenance to the central maintenance department.
Research
Research feasibility and application of major equipment changes or facility upgrades.
Review
Review all reports as assigned and take corrective actions as required.
Review and evaluates work products, methods, and procedures.
Review detailed labor standards by cost center to support annual budgeting process.
Review, document and approve all PTO and time cards prior to submitting to payroll.
Review, evaluate, and approve specifications for issuing and awarding bids.
Revise
Revise production schedules and priorities as a result of equipment failure or operating problems.
Schedule
Schedule plant operation to meet production plan.
Set
Set and monitor Plant production, quality and cost goals consistent with Group goals.
Set up and execution of annual safety training with the aid of CSR Manager and RO Manager.
Share
Share a trusting relationship with workgroup and recruit, manage and develop plant staff.
Solve
Solve day-to-day operational issues and achieves short- and long-term performance goals.
Support
Support and mentor two supervisors and other employees on the floor on a regular basis.
Support Profitable Sales Growth in line with Global business strategy.
Support safety programs, policies and practices that foster a safe work environment.
Support supplier management, and support the management of working and non-working inventory.
Support the application and use of the site CMMS (Computer Maintenance Management System).
Support the head of manufacturing in planning and overseeing Ontario Knife Company?.
Take
Take complete ownership and accountability for overall plant operations with a desire to win.
Take corrective actions as necessary and in a timely manner, in accordance with company policy.
Take part in customer visits and audits.
Train
Train and coach associates engaged in CMM operations for future career advancement.
Train and coach employees.
Train, develop and motivate plant personnel.
Understand
Understand the nuances of dealing with structured and unstructured data.
Use
Use the "Go and See” approach when making decisions or taking action on root cause.
Utilize
Utilize Continuous Improvement tools to enhance the overall plant performance.
Work with
Work and learn from direct reports.
Work closely with Senior Operations Manager and Safety Director to develop winning safety culture.
Work well with a team and understands how to manage different generations.
Work with production and purchasing to ensure inventory accuracy.
Write
Write up reports of production activity and employee performance.
Most In-demand Hard Skills
The following list describes the most required technical skills of a Plant Manager:
Manufacturing
Management
Plant Management
Quality
Business
Continuous Improvement
Lean Manufacturing
Production
MS Outlook
Electrical
Operations
Resource Allocation
Strategic Planning
Food Manufacturing
Microsoft Office
Operations Management
Communications
Most In-demand Soft Skills
The following list describes the most required soft skills of a Plant Manager:
Written and oral communication skills
Leadership
Organizational capacity
Interpersonal skills
Problem-solving attitude
Attention to detail
Analytical ability
Decision-making skills
Planning
Results-oriented
Self-starter
Innovative
Team building
Team leadership
Active listener
Communications
Detail-oriented
People management