Main Responsibilities and Required Skills for a Depot Manager
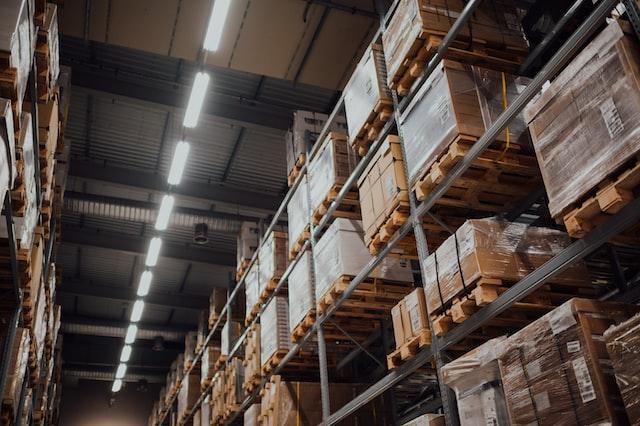
A Depot Manager is a professional who oversees the efficient operation of a depot or warehouse, ensuring that goods and materials are stored, organized, and distributed effectively. They play a crucial role in managing the logistics and supply chain processes within the depot, ensuring that everything runs smoothly and efficiently. In this blog post, we will describe the primary responsibilities and the most in-demand hard and soft skills for Depot Managers.
Get market insights and compare skills for other jobs here.
Main Responsibilities of a Depot Manager
The following list describes the typical responsibilities of a Depot Manager:
Achieve
Achieve Inventory Accountability objectives.
Analyze
Analyze data and generate reports on key performance indicators.
Approve
Approve and forward all monthly invoices to the AP department promptly.
Arrive
Arrive at Depot on time to ensure timely support is provided to SDAs.
Assist with
Assist with customer or retailer service issues.
Book
Book travel events while being responsible and cost effective (company credit card will be issued).
Check
Check fire extinguishers annually to ensure proper working order.
Collaborate with
Collaborate with other departments to optimize overall business operations.
Collaborate with suppliers and vendors to negotiate favorable terms and pricing.
Communicate
Communicate business, product, POS and promotional activities to SDAs in a timely manner.
Communicate SDA(s) information, questions and concerns to the management team in a timely manner.
Communicate with the manager any feedback or ideas for the thrift shops.
Conduct
Conduct regular inspections to ensure proper maintenance of equipment and facilities.
Conduct regular performance evaluations for team members.
Contribute
Contribute towards improvements in processes & flows.
Coordinate
Coordinate and oversee the receiving, storage, and distribution of goods.
Coordinate with transportation providers for timely delivery of goods.
Count
Count and balance all inventory on a daily basis to ensure proper inventory levels.
Create
Create a positive environment in Depot at load times to support the engagement levels for our IDPs.
Create designated areas that are protected from debris to store marketing material.
Create opportunities to develop "on the job” technical competence through inter-associate learning.
Define
Define accurate MIN MAX levels per site by using tools within AX and PowerBI.
Deliver
Deliver the sales plan through Depot Technician consultations with clients.
Develop
Develop and implement cost-saving initiatives.
Develop and implement strategies to optimize depot operations.
Develop and maintain strong relationships with suppliers and vendors.
Develop a travel schedule that will be approved by the Director of Distribution.
Develop and execute plans to broaden team completion of technical certifications.
Develop relationships with key stakeholders and clients.
Distribute
Distribute & bill product to SDAs based on their daily orders.
Educate
Educate the team on the expectations of product quality when pulling orders and samples.
Enforce
Enforce a regular inventory count in each yard to verify physical counts match the inventory in AX.
Ensure
Ensure all employees are properly trained for their position.
Ensure a safe work environment for both employees and customers.
Ensure company and customer assets and physical inventory is secured.
Ensure compliance with legal and regulatory requirements.
Ensure compliance with safety regulations and maintain a safe working environment.
Ensure inventory is placed in the correct location.
Ensure smooth operations of the Material Depot.
Ensure that all materials are accurately labeled.
Ensure that the material depot is organized.
Establish
Establish and maintain service excellence by assigning the highest priority to customer satisfaction.
Evaluate
Evaluate project plans and ensure Depot information is accurate and timelines can be met.
Evaluate staff performance and provide constructive feedback.
Facilitate
Facilitate resolution of project conflicts based upon geographical and resource requirements.
Forecast
Forecast future demands and plan accordingly.
Foster
Foster a positive and motivating work environment.
Foster Collaboration and Teamwork.
Identify
Identify and implement process improvement initiatives.
Implement
Implement and enforce company policies and procedures.
Implement and enforces HSE requirements on site with the support of HSE team representatives.
Implement quality control measures to ensure product integrity.
Issue
Issue stale / unsaleable credit to Distributors in accordance with company policy.
Keep
Keep all equipment in proper working condition.
Keep depot free of clutter and trip hazards from all working areas.
Keep records and schedule maintenance for equipment.
Keep thrift shops stocked with clothes, and other items as required by the volunteers.
Keep track of all material and tools that are checked out.
Lead with
Lead with integrity and respect.
Liaise with
Liaise with Depots, Depot Management and Site QA on any client quality / service complaints.
Maintain
Maintain accurate forklift certification records for the team at each site.
Maintain a safe and clean depot to adhere with OSHA guidelines.
Maintain a safe, clean depot at all times, both inside and outside the depot.
Maintain communication with ZSMs regarding cuts, shorts and product quality concerns.
Maintain consistent communication with DSMs, SDAs and management.
Maintain proper light and fix or replace any electrical source.
Maintain sanitation standards as outlined in CPOESAN an OSHA Compliance reports.
Maintain sufficient POS inventory at all times to support promotional activity.
Manage
Manage and oversee the maintenance of equipment and vehicles.
Manage and resolve conflicts among team members.
Manage budgets and control expenses.
Manage Depot expenses, particularly utility expenses, to control costs and adhere to budget.
Manage reporting and analysis of Metric and KPI's, and inventory reports required by the client.
Manage the order process, inventory of Ancillary projects with 3rd party providers.
Manage time off requests and schedules in coordination with the yard coordinator.
Monitor
Monitor and maintain inventory levels to meet customer demands.
Monitor and manage diagnosis and repair quality to prevent rework.
Monitor the proper turn of inventory onsite (IE, oldest shipped first).
Optimize
Optimize space utilization within the depot.
Order
Order and maintain adequate supply of dry product inventory.
Oversee
Oversee one of our operational depots and supporting out bases.
Participate in
Participate in depot audit activities - documentation tracking, information retention.
Perform
Perform quarterly reviews of the yard coordinators to ensure expectations are being met.
Plan
Plan and schedule the movement of goods within the depot.
Print and communicate all SDA billings and reports via Depot HHC (daily / weekly).
Process
Process Improvement Focus.
Promote
Promote a positive team environment.
Promote detailed updates in ETS to keep all associates & customers informed of progress.
Provide
Provide accurate and consistent billing information for IDPs.
Provide proper first aid and blood clean-up kit.
Purchase
Purchase all required PPE and train the team on proper use.
Receive
Receive invoices, order supplies, create purchase orders.
Report
Report any depot repair work needed and arrange for the work to be done in a timely manner.
Report any plant service or transportation issues (late trucks, product cuts, etc.).
Represent
Represent the employer in MBL negotiations regarding its own area of responsibility.
Resolve
Resolve customer complaints or issues in a timely manner.
Rotate
Rotate dry product to maintain fresh inventory, eliminating losses.
Secure
Secure the lawn maintenance contracts per site if required.
Secure vendors for maintenance and repairs to existing equipment.
Shape
Shape new practices and define the strategy of the depot.
Stay updated on
Stay informed about technological advancements in warehouse management systems.
Stay updated on industry trends and advancements.
Supervise
Supervise and train depot staff to ensure efficient workflow.
Take
Take the opportunity to work with one of America s best-loved and well-recognized brand icons.
Take the opportunity to work with one of America's best-loved and well-recognized brand icons.
Test
Test planning in coordination with the production and the consortium member.
Track
Track dollies to ensure minimal losses, in accordance with Dollie Management Program guidelines.
Track, monitor and analyse Depot metrics on a weekly basis and drive operational excellence.
Travel
Travel to all assigned distribution yards.
Validate
Validate counts when onsite by spot checking several items.
Validate the team is keeping the yard from debris (IE, shrink wrap, bags, connectors, pallets).
Work with
Work with yard coordinators on yard layouts to increase loading and unloading efficiencies.
Most In-demand Hard Skills
The following list describes the most required technical skills of a Depot Manager:
Proficiency in warehouse management systems.
Strong knowledge of inventory control and management.
Familiarity with transportation and logistics operations.
Understanding of safety and regulatory compliance.
Ability to analyze data and generate meaningful reports.
Expertise in cost management and budgeting.
Knowledge of lean management principles.
Proficiency in using warehouse equipment and machinery.
Strong computer skills, including proficiency in MS Excel and inventory management software.
Experience in implementing process improvement methodologies.
Knowledge of import/export regulations and documentation.
Familiarity with quality control procedures.
Ability to analyze supply chain data and identify optimization opportunities.
Understanding of demand forecasting and planning techniques.
Proficiency in project management principles and tools.
Knowledge of continuous improvement methodologies like Six Sigma or Kaizen.
Ability to interpret and apply relevant laws and regulations.
Experience in managing and optimizing warehouse layouts.
Understanding of vendor management and negotiation.
Knowledge of health and safety protocols and procedures.
Most In-demand Soft Skills
The following list describes the most required soft skills of a Depot Manager:
Excellent leadership and team management abilities.
Strong communication and interpersonal skills.
Effective problem-solving and decision-making skills.
Ability to work under pressure and meet deadlines.
Exceptional organizational and multitasking skills.
Adaptability and flexibility to handle changing situations.
Strong analytical and critical thinking abilities.
Customer-focused mindset and ability to build strong relationships with clients.
Effective negotiation and conflict resolution skills.
Ability to motivate and inspire team members.
Conclusion
A successful Depot Manager must possess a combination of technical expertise and interpersonal skills. They need to have a deep understanding of warehouse operations, logistics, and inventory management. Additionally, they should have the ability to lead a team, make informed decisions, and adapt to the dynamic nature of the industry. By mastering both the hard and soft skills required for the role, Depot Managers can ensure the smooth functioning of the depot and contribute to the overall success of the organization.