Main Responsibilities and Required Skills for a Continuous Improvement Manager
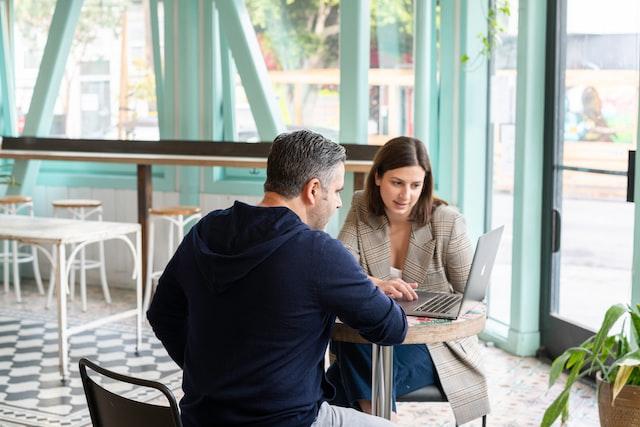
A Continuous Improvement Manager is a professional who plays a crucial role in driving organizational excellence by identifying and implementing continuous improvement initiatives. This role involves analyzing processes, identifying areas for improvement, and implementing strategies to optimize efficiency and effectiveness within an organization. In this blog post, we will describe the primary responsibilities and the most in-demand hard and soft skills for Continuous Improvement Managers.
Get market insights and compare skills for other jobs here.
Main Responsibilities of a Continuous Improvement Manager
The following list describes the typical responsibilities of a Continuous Improvement Manager:
Advocate
Advocate for product quality and keep the development team accountable.
Analyze
Analyze and correct quality issues each week.
Analyze and report on marketing analytics and business development metrics.
Analyze data to understand down time and create mitigation tactics.
Assist in
Assist in collecting and monitoring Key Performance Indicators for the organization.
Assist in designing new methods and procedures for operational processes.
Assist in maintaining bills of material for all machine components and parts.
Assist in the facilitation of Manufacturing Fundamentals and other, similar, key programs.
Assist with administrative tasks, projects and the organization of department files and supplies.
Build
Build and maintain all Standard Operating Procedures and Work Instructions across multiple functions.
Build and manage a deployment roadmap of Continuous Improvement at the group level.
Build a team that champions continuous improvement.
Champion
Champion activities required to reduce unscheduled downtime.
Champion any new Technology UX initiatives.
Champion continuous improvement projects using Lean Manufacturing methods.
Coach
Coach and mentor LEAN Project Champions to lead and support projects.
Coach and train leaders in continuous improvement and lean manufacturing.
Coach and trains staff in the use of continuous improvement tools.
Coach, guide and / or lead cross-functional teams to achieve resolution of assigned projects.
Coach extended teams on Lean Six Sigma tools & continuous improvement methodology.
Coach team members and management on the consistent Lean behaviors.
Collaborate with
Collaborate with IT teams to implement technological solutions for process optimization.
Collaborate with other PMO team members on local PMO processes.
Collaborate with stakeholders to ensure buy-in and support for improvement initiatives.
Collaborate with the Production and Support teams to identify waste in the manufacturing process.
Collaborate with the three divisions within Sonoco.
Collaborate with various teams to generate high quality, cost effective solutions in short.Communicate
Communicate the status and results of projects to key stakeholders.
Conduct
Conduct all Job Tasks in a Safe and Responsible manner.
Conduct change management activities to support process improvements.
Conduct gap analysis to "best in class” to understand where we need to improve to support our vision.
Conduct process assessments and analyze data to identify areas of improvement.
Conduct regular audits to assess compliance and identify areas for improvement.
Conduct regular performance reviews and provide feedback to team members.
Conduct root cause analysis to identify underlying issues.
Contact
Contact all membership leads by phone where possible and also by email and text when required.
Contribute to
Contribute to strategic planning at the plant level.
Contribute to the Continuous Improvement network development.
Coordinate
Coordinate activities related to new tooling / mold / system testing.
Coordinate prototype drawings for products or processes with necessary support personnel.
Coordinate the implementation of engineering change order requests for all related departments.
Coordinate tooling / mold / system / product design reviews and / or changes.
Create
Create periodic format presentations on company implementation progress to management.
Define
Define, create and report KPIs to measure the end-to-end health of Supply Chain operations.
Define project scopes, objectives, and deliverables.
Design
Design Layout and Production Line Configuration of Facilities and Staffing Requirements.
Develop
Develop and deliver presentations on continuous improvement progress and results.
Develop and implement improvement strategies and action plans.
Develop and improve visual SOPs and work instructions.
Develop and maintain annual value stream mapping efforts, CI plans, and calendars.
Develop and maintain metrics to measure process performance.
Develop and manage improvement budgets and resource allocation.
Develop and manage quality and continuous improvement team.
Develop and / or oversee quality control specification drawings for products.
Develop and write sequence of operations as well as time estimates for each operation specification.
Develop a set of KPIs that track progress of Lean initiatives.
Develop change management materials to support successful project implementation.
Develop comprehensive metrics for measuring operational effectiveness.
Develop continuous improvement strategies for the plant.
Develop internal Lean capabilities at all levels.
Develop, manage and lead implementation of Quality at Source program.
Develop, plans, and schedules, for projects to improve existing processes.
Develop Preventative Maintenance program for existing and new equipment.
Develop prioritized improvement action plans.
Develop project implementation plans and budgets to ensure successful opportunity realization.
Develop the overall CI strategy for APAC business in alignment with companywide strategy.
Develop tools and systems to support testing or development.
Direct
Direct supervise China Continuous Improvement initiatives with site support.
Document
Document all new procedures, workflows, approaches, and goals.
Document and works with the site controller to measure and validate the impact of improvements.
Drive
Drive a culture of continuous improvement throughout the organization.
Drive and engage technology team members to write technology blog posts.
Drive cultural change and lead foundation principles such as 5S, GEMBA, LEAN Principles.
Drive data driven failure analysis, identification, and resolution.
Drive the adoption of Serve Management, CI and UX across IT.
Drive the customer value proposition.
Drive the implementation of quality management systems.
Drive the performance improvement in different business fields of Precision Diagnosis.
Eliminate
Eliminate waste of time, ingredients, supplies and equipment.
Employ
Employ process improvement methodologies and the application of innovative thinking.
Engage
Engage with all of our partners on our goals and strategies.
Ensure
Ensure 2-way communication throughout the continuous improvement organization.
Ensure Artwork implementation compliance.
Ensure compliance with quality standards and regulations.
Ensure continuous improvement of work practices.
Ensure production goals are followed and achieved.
Ensure that the products comply with the specifications and meet the Goodfood.
Ensure the cleaning of each workstation and equipment is completed at the end of each shift.
Ensure through audits that tools are appropriately and effectively used.
Establish
Establish and maintain relationships with external partners and vendors.
Establish improve, sustain and report KPI performance.
Evaluate
Evaluate and decide upon key investments in equipment, infrastructure, and talent.
Execute
Execute and oversee several continuous improvement work streams.
Facilitate
Facilitate cross-functional teams to address process improvement projects.
Facilitate Lean best practices / knowledge sharing across the entire organization.
Facilitate training and continuous improvement discovery and design events.
Follow
Follow the standard improvement expectations.
Follow-up
Follow-up with operations ensuring successful implementation of Future State plans.
Forecast
Forecast future needs of clients and proactively strategize solutions.
Foster
Foster a collaborative environment that encourages innovation and idea sharing.
Help
Help build organizational Standard Operating Procedures (SOP's) to drive continuous improvement.
Help drive the organization to one that is supportive of and operating at the Least Wasteful Way.
Help lead and drive the culture shift required in ITO.
Help train new employees and aim to empower them in their work.
Identify
Identify actions, initiatives, and opportunities to grow and improve Productivity.
Identify and resolve barriers and roadblocks to improvement initiatives.
Identify, evaluates and present projects aligned with the operating or strategic agendas.
Identify needs for specific skills training.
Identify opportunities for process improvement and cost reduction.
Identify trainer options, and may lead training as required.
Implement
Implement and utilize process improvement software and tools.
Implement corrective actions and audit to ensure compliance to new processes and procedures.
Implement lean methodologies and tools to drive process optimization.
Implement new tools, methods, standards and processes to eliminate those wastes.
Implement the Automation Strategy to a high standard of quality.
Improve
Improve and manage the Quality Management System (QMS) as required.
Integrate
Integrate Continuous Improvement ideas as part of the process and drive teams towards standard work.
Interact
Interact, supports, facilitates, and lead multi-functional work teams.
Invent
Invent, design, and implement engineering solutions to complex processing efficiency problems.
Keep
Keep those ambitions in sights and imagine where JLL can take you....
Lead
Lead and manage CI projects that deliver a best-in-class customer experience.
Lead and manage the M& S Exec in the Management of the Projects Portfolio.
Lead continuous improvement initiatives across the organization.
Lead cross functional teams and work effectively with all levels of the organization.
Lead effort to implement best practices, ensuring adherence to the principles of lean manufacturing.
Lead large cross functional initiatives related to the development and delivery of the next.
Lead multiple projects to achieve improvements in safety, quality, efficiency, and cost.
Lead process mapping and value stream analysis exercises.
Lead projects and initiatives from idea generation to strategic execution.
Lead / supports key initiatives as needed.
Lead team meetings, document clear actions and enable timeline achievement.
Lead Value Stream Steering Committee and manage the transformation plan.
Lead workshops resulting in tangible key performance indicator improvements.
Leverage
Leverage data to prioritize actions and drive continuous improvement.
Liaise with
Liaise with other Global CI Teams, Corporate Engineering staff on Best Practices sharing.
Maintain
Maintain and continue to expand personal knowledge of Lean Six Sigma methods and tools.
Maintain Automation Strategy documents with direction from Technical Leads.
Maintain Bills of Material.
Maintain compliance of Medical Device Design History and Risk Management Files.
Maintain good working relationships and motivate employees.
Make
Make your mark in the fight against cancer.
Manage
Manage, and develop plans, schedules, and budgets for projects to improve existing processes.
Manage and lead process team to achieve desired results.
Manage and train project teams in regards to process improvement methodology.
Manage / assist with sites savings targets for CI efforts.
Manage / assist with sites savings targets for continuous improvement efforts.
Manage multiple projects, and support plant process improvement teams as needed.
Manage own time to meet agreed upon targets.
Manage Quality, Continuous Improvement, and Maintenance staff.
Manage vendor quality issues and work with purchasing on developing vendor Quality Scorecard.
Map
Map current processes, define, implement and measure improvements.
Measure
Measure and report the return on investment (ROI) of improvement projects.
Mentor
Mentor and support Lean-Six Sigma, DMAIC and TPM processes as needed.
Mitigate
Mitigate ongoing CFR issues by ensuring continuity of supply.
Monitor
Monitor and analyze customer feedback to identify improvement opportunities.
Monitor and track progress of improvement projects.
Monitor industry best practices and trends in continuous improvement.
Offer
Offer technical expertise to company on statistics, Six Sigma methodology, tools and practices.
Organize
Organize and manage projects.
Oversee
Oversee a team of Quality Lab Techs.
Participate in
Participate in different meetings and make suggestions for situations to improve.
Prepare
Prepare staff schedules and approve their hours.
Present
Present our plans to our partners and ensure that there is agreement on an approach.
Process
Process measurement, documentation, analysis, and improvement.
Produce
Produce required reporting according to needs of stakeholders.
Promote
Promote and apply continuous improvement / lean Six Sigma practices.
Promote the maintenance of workplaces and clean and safe equipment.
Promote the use of metrics and data to drive project focus.
Provide
Provide cost estimates and capital expenditure justification as necessary.
Provide input to development of the capital budget for each site.
Provide regular project status update reports to Project Team and Senior Management.
Provide risk and Issues identification and mitigation.
Provide training and coaching to employees on continuous improvement methodologies.
Pursue
Pursue, achieve and exceed cost, revenue and margin targets.
Reduce
Reduce the cost of quality.
Report
Report any accidents, incidents and unsafe / hazardous conditions to your Manager.
Report any damages of property and machinery to your Manager.
Review
Review and Analysis of Production Schedules, Processes, Specifications.
Scope
Scope the project implementations of business systems within the work unit.
Secure
Secure adherence to State Street's internal Project Management methodologies and standards.
Secure prioritization and time management to support multiple projects / tasks in parallel.
Settle
Settle first level conflicts by being fair and equitable.
Solve
Solve highly complex problems and prioritizes actions in a timely manner.
Support
Support and meets Departmental, Plant and Corporate HS&E goals.
Support capital projects as needed – design, quotes, and help manage AFE through completion.
Support and help Integrate new Business and NPDI.
Support strategic and operational planning on the warehousing and fulfillment function.
Support the Production Manager by completing visual performance board.
Teach
Teach and models tools and concepts of Lean Thinking and Six Sigma, facilitates Kaizen events.
Train
Train team members on Lean principles and other CI tools.
Understand
Understand all environmental policies and significant environmental impact of job activities.
Understand all safety policies and significant safety impact of job activities.
Utilize
Utilize project management methodologies to ensure successful project execution.
Work with
Work closely with and report to the site lead.
Work closely with Leadership to execute the ITSM / CI and UX Strategy.
Work closely with other CI Managers to share best practices.
Work with partner teams on feature scope, deliverables, and timeline.
Work with the Director of Operations on delivering Strategic Operational Results via OGSM.
Work with the learning and development team to roll out new processes through engaging training.
Work with the team in charge of 5S to ensure we are sustaining and improving to be audit ready.
Work with various multi-disciplinary teams to reduce process and business variations.
Most In-demand Hard Skills
The following list describes the most required technical skills of a Continuous Improvement Manager:
Lean Six Sigma methodologies and tools.
Process analysis and mapping techniques.
Statistical analysis and data-driven decision-making.
Project management principles and methodologies.
Root cause analysis and problem-solving techniques.
Change management strategies and techniques.
Quality management systems (e.g., ISO, TQM).
Performance measurement and metrics.
Process improvement software and tools (e.g., Minitab, Visio).
Advanced knowledge of Excel and data analysis tools.
Value stream mapping and optimization.
Risk assessment and mitigation strategies.
Cost analysis and financial modeling.
Knowledge of manufacturing processes and systems.
Supply chain management and logistics.
Agile methodologies and continuous delivery practices.
IT systems and software implementation.
Compliance and regulatory requirements.
Knowledge of industry-specific standards and best practices.
Effective utilization of ERP (Enterprise Resource Planning) systems.
Most In-demand Soft Skills
The following list describes the most required soft skills of a Continuous Improvement Manager:
Strong leadership and the ability to influence others.
Excellent communication and presentation skills.
Effective problem-solving and critical thinking abilities.
Collaborative and team-oriented mindset.
Strong analytical and data interpretation skills.
Flexibility and adaptability to changing environments.
Strategic thinking and long-term planning.
Effective negotiation and conflict resolution skills.
Strong project management and organizational skills.
Ability to work well under pressure and meet deadlines.
Decision-making skills based on data and analysis.
Continuous learning and self-improvement mindset.
Excellent interpersonal and relationship-building skills.
Empathy and ability to understand and address diverse perspectives.
Ability to facilitate and lead cross-functional teams.
Resilience and ability to handle setbacks and challenges.
Attention to detail and a focus on quality.
Time management and prioritization skills.
Ability to inspire and motivate others towards continuous improvement.
Ethical and professional conduct.
Conclusion
Continuous Improvement Managers are vital for organizations striving to optimize processes and drive efficiency. They bring together technical expertise, analytical thinking, and strong interpersonal skills to lead improvement initiatives. By embracing the responsibilities and developing the necessary hard and soft skills, Continuous Improvement Managers can make a significant impact on an organization's success and its ability to adapt to changing market demands.